Linear tables with open shaft guidance system
Features
Linear tables LTS are suitable for moderate loads and long stroke lengths.
Linear tables LTS have higher load capacity in the compressive direction, due to the supported guidance shafts, than for example linear tables LTE with open shaft guidance system.
Basic design
The basic design of linear tables LTS has no drive and comprises:
- a carriage unit made from aluminium alloy with four linear ball bearings KBO lubricated via two lubrication nipples on each side of the carriage unit
- two shaft and support rail units. The shaft and support rail units are composite units comprising an aluminium support rail and a shaft made from quenched and tempered steel to rolling bearing quality. The shafts are hardened and ground
- bellows fitted as optional.
The linear ball bearings have an initial greasing, are sealed and can be relubricated.
With trapezoidal screw drive
Linear tables LTS with trapezoidal screw drive comprise the basic design plus the following additional components:
- a rolled trapezoidal screw spindle with a cylindrical bronze nut
- on the drive side: a locating bearing in a shaft support block; depending on the table size, the locating bearing comprises one double row angular contact ball bearing or two single row angular contact ball bearings
- on the opposite side: a non-locating bearing in a shaft support block; the non-locating bearing comprises one single row ball bearing.
The spindle support bearings are sealed and lubricated for life. The spindle nut has an initial greasing, is sealed and can be relubricated via a lubrication nipple in the carriage unit.
With ball screw drive
Linear tables LTS with ball screw drive comprise the basic design plus the following additional components:
- a rolled ball screw spindle with a cylindrical single nut M. In the case of some pitch values, preloaded double nuts MM are also possible
- on the drive side: a locating bearing in a shaft support block; the locating bearing comprises a preloaded double row angular contact ball bearing ZKLN and a lubrication nipple
- on the opposite side: a non-locating bearing in a shaft support block; the non-locating bearing comprises a needle roller bearing NA and a lubrication nipple.
The spindle support bearings and spindle nuts have an initial greasing, are sealed and can be relubricated. The spindle nuts can be relubricated via a lubrication nipple in the carriage unit.
With bellows
Linear tables LTS can be equipped with two sets of bellows, excluding LTS12.
The bellows are attached by means of Velcro tape.
For the same stroke length, the total length of a linear table with bellows is greater than the total length of a linear table without bellows.
Screw drive
The spindle thread has a pitch value of between 3 mm and 50 mm, see table. As standard, single nuts with an axial clearance dependent on the pitch are used. In the case of some pitch values, the ball screw drive can be supplied with preloaded double nuts.
Screw drive variants
Screw drive variants | Trapezoidal screw drive | Ball | Suffix | ||
---|---|---|---|---|---|
Pitch | 3 | mm | ● | ‒ | 3 |
4 | mm | ● | ● | 4 | |
5 | mm | ● | ● | 5 | |
6 | mm | ● | ‒ | 6 | |
8 | mm | ● | ‒ | 8 | |
10 | mm | ● | ● | 10 | |
20 | mm | ‒ | ● | 20 | |
40 | mm | ‒ | ● | 40 | |
50 | mm | ‒ | ● | 50 | |
Single nut (cylindrical) | ● | ● | M | ||
Double nut (cylindrical) | ‒ | ● | MM | ||
Without drive (no spindle), | ‒ | ‒ | OA |
Drive elements
For linear tables, Schaeffler also supplies components such as couplings, coupling housings, servo motors and servo controllers, ➤ Figure. The range is supplemented by servo controllers for effective drive and control of the motors.
Linear table
with open shaft guidance system
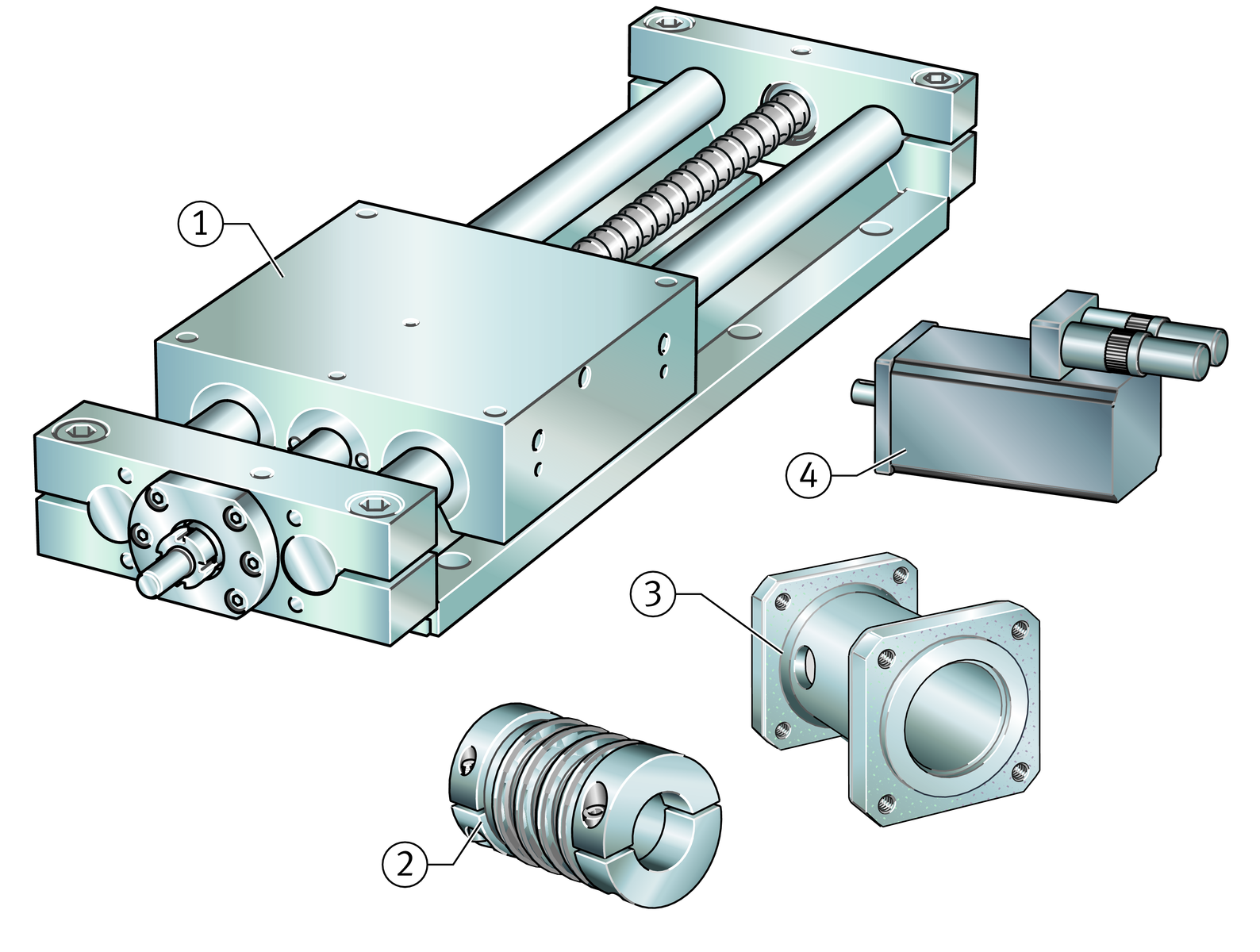




Proven drive combinations
For vertical and horizontal applications, the necessary drive components can be combined as a function of the mass to be moved, the acceleration and the travel velocity of the carriages.
ATTENTION
The bearing load in the linear tables must be checked; it is not taken into consideration in dimensioning of the motor. For vertical mounting, motors with a holding brake must be used.
If different loading and kinematic criteria apply, the least favourable operating conditions should be used for calculation of the drive motor and design of the gearbox, coupling and servo controller.
Special designs
Special designs are available by agreement. Examples of these are linear tables LTS with
- guidance shafts and spindles with anti-corrosion protection
- bellows resistant to welding beads
- a rolled ball screw spindle to accuracy class 25 μm per 300 mm
- a trapezoidal screw drive with a left hand thread
- special table designs according to customer requirements.
Design and safety guidelines
The information on design and safety guidelines for linear tables LTS substantially matches the information on design and safety guidelines for linear tables LTE. The following pages describe exclusively the differences between the linear tables LTS and the linear tables LTE.
Main load direction of linear tables with linear ball bearings
The effective load rating of a linear ball bearing is dependent on the position of the load direction in relation to the position of the ball rows.
In the case of linear tables LTS, the linear ball bearings are fitted in a specific alignment. As a result, the basic load rating relating to the mounting position of the linear ball bearing is specifically defined, ➤ Figure.
Main load direction
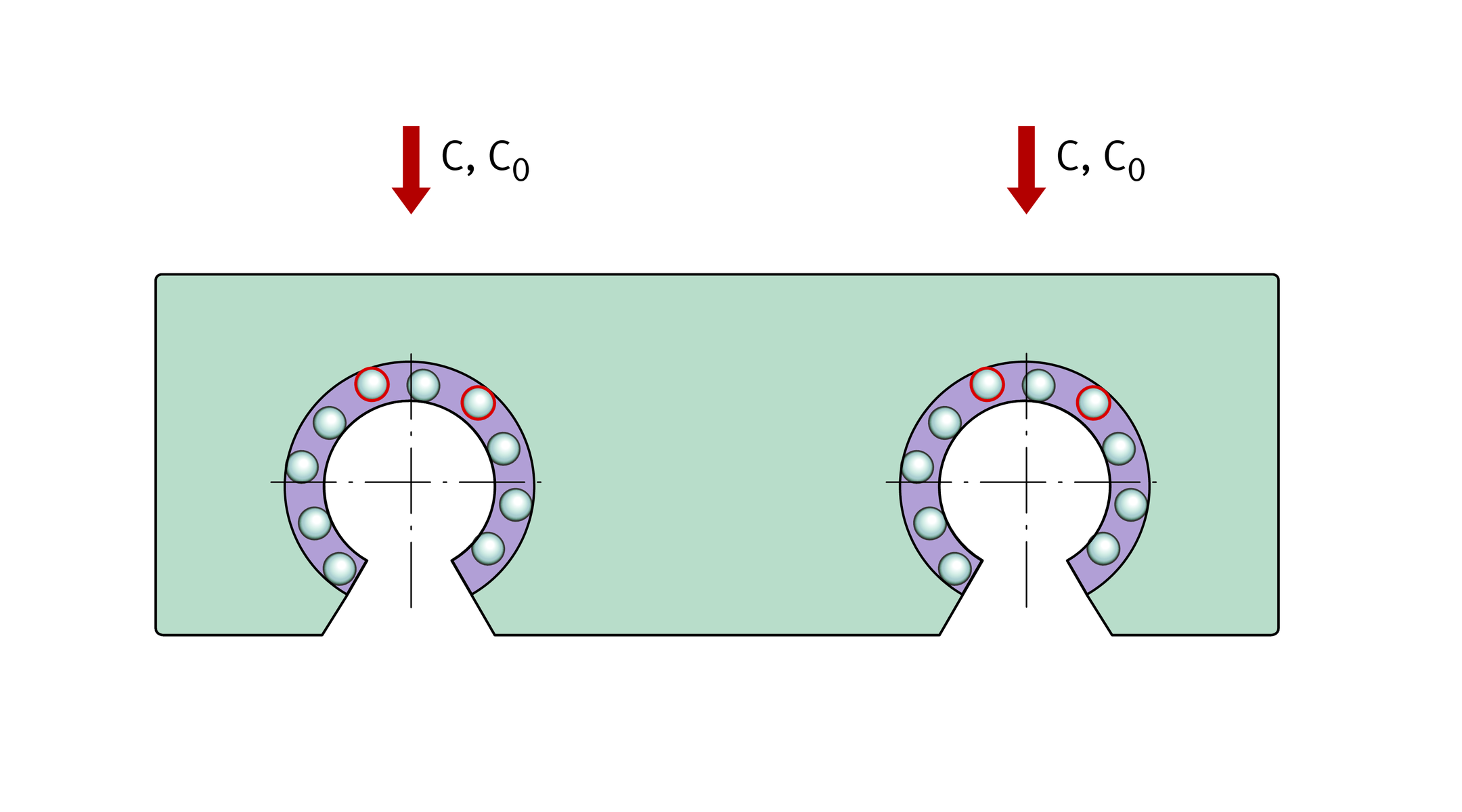
Deflection
The deflection of linear tables LTS is essentially dependent on the adjacent construction. It is not therefore possible to provide data or diagrams for the deflection.
Length calculation
of linear tables
The length calculation of linear tables is based on the required effective stroke length NH. The effective stroke length NH must be increased by the addition of safety spacing values on both sides of the travel distance. It is only if bellows are present that the effective length BL must be added.
The total length Ltot of the linear table is determined from the effective stroke length NH, the safety spacings S, the carriage unit length L and the lengths of the end plates L4 and L5.
Parameters required for length calculation
GH | mm | Total stroke length |
NH | mm | Effective stroke length |
S | mm | Safety spacing, see table |
L | mm | Length of carriage plate |
Ltot | mm | Total length of linear table |
L4 | mm | Length of end plate |
L5 | mm | Length of end plate |
L20 | mm | Screw head of end plate |
L21 | mm | Thickness of end plate |
FBL | Effective length factor according to linear table type | |
BL | mm | Effective length of bellows |
BB | mm | Length of bellows fastener. |
Total stroke length GH
The total stroke length GH is determined from the required effective stroke length effective stroke length NH and the safety spacings S, which must correspond to at least the spindle pitch P.
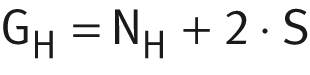
Maximum lengths of linear tables
The maximum length of linear tables LTS without bellows is dependent on the size, the drive type and the maximum length of the bellows, see table.
ATTENTION
In the case of a total length Ltot < 2 · L + 30, not all fixing holes in the support rail will be accessible, so please consult us.
Maximum lengths without bellows
Designation | Ltot | Designation | Ltot | Designation | Ltot |
---|---|---|---|---|---|
mm | mm | mm | |||
LTS12 | 6 000 | ‒ | ‒ | ‒ | ‒ |
LTS16 | 6 000 | LTS16..-TR | 2 900 | LTS16..-KGT | 2 900 |
LTS20 | 6 000 | LTS20..-TR | 2 900 | LTS20..-KGT | 5 850 |
LTS25 | 6 000 | LTS25..-TR | 2 900 | LTS25..-KGT | 5 850 |
LTS30 | 6 000 | LTS30..-TR | 2 900 | LTS30..-KGT | 5 850 |
LTS40 | 6 000 | LTS40..-TR | 2 900 | LTS40..-KGT | 5 850 |
LTS50 | 6 000 | LTS50..-TR | 2 900 | LTS50..-KGT | 5 850 |
Maximum lengths with bellows
Designation | Ltot | Designation | Ltot | Designation | Ltot |
---|---|---|---|---|---|
mm | mm | mm | |||
LTS12 | ‒ | ‒ | ‒ | ‒ | ‒ |
LTS16 | 3 000 | LTS16..-TR | 2 900 | LTS16..-KGT | 2 900 |
LTS20 | 3 800 | LTS20..-TR | 2 900 | LTS20..-KGT | 3 800 |
LTS25 | 4 400 | LTS25..-TR | 2 900 | LTS25..-KGT | 4 400 |
LTS30 | 5 400 | LTS30..-TR | 2 900 | LTS30..-KGT | 5 400 |
LTS40 | 6 000 | LTS40..-TR | 2 900 | LTS40..-KGT | 5 600 |
LTS50 | 6 000 | LTS50..-TR | 2 900 | LTS50..-KGT | 5 600 |
Total length Ltot
The following ➤ equtions are designed for one linear table. The parameters and their position can be found in ➤ Figure and ➤ Figure as well as in the table.
Length parameters for linear tables without drive
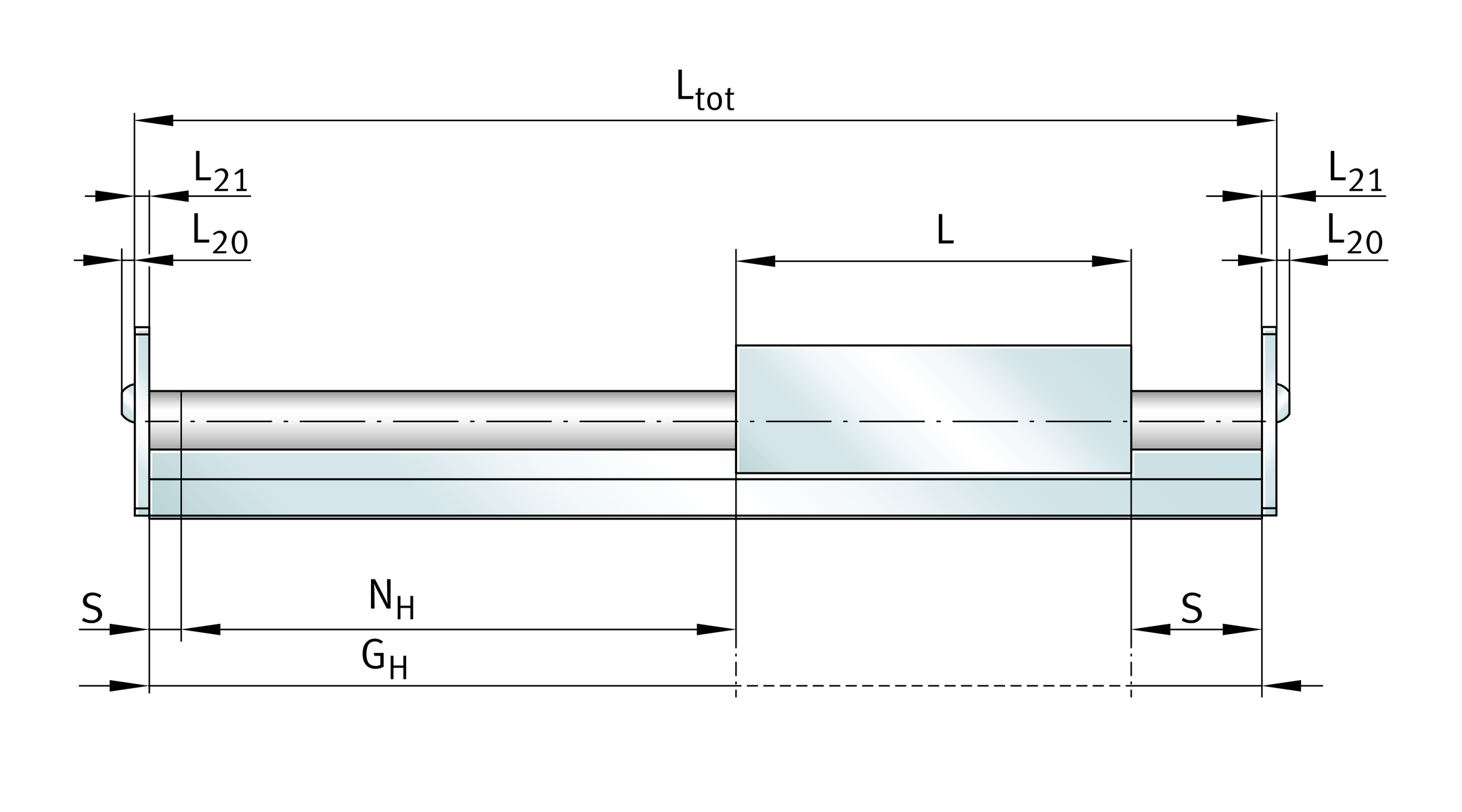
Linear table without bellows
LTS..-OA

Linear table with bellows
LTS..-OA

Length parameters for linear tables with trapezoidal or ball screw drive
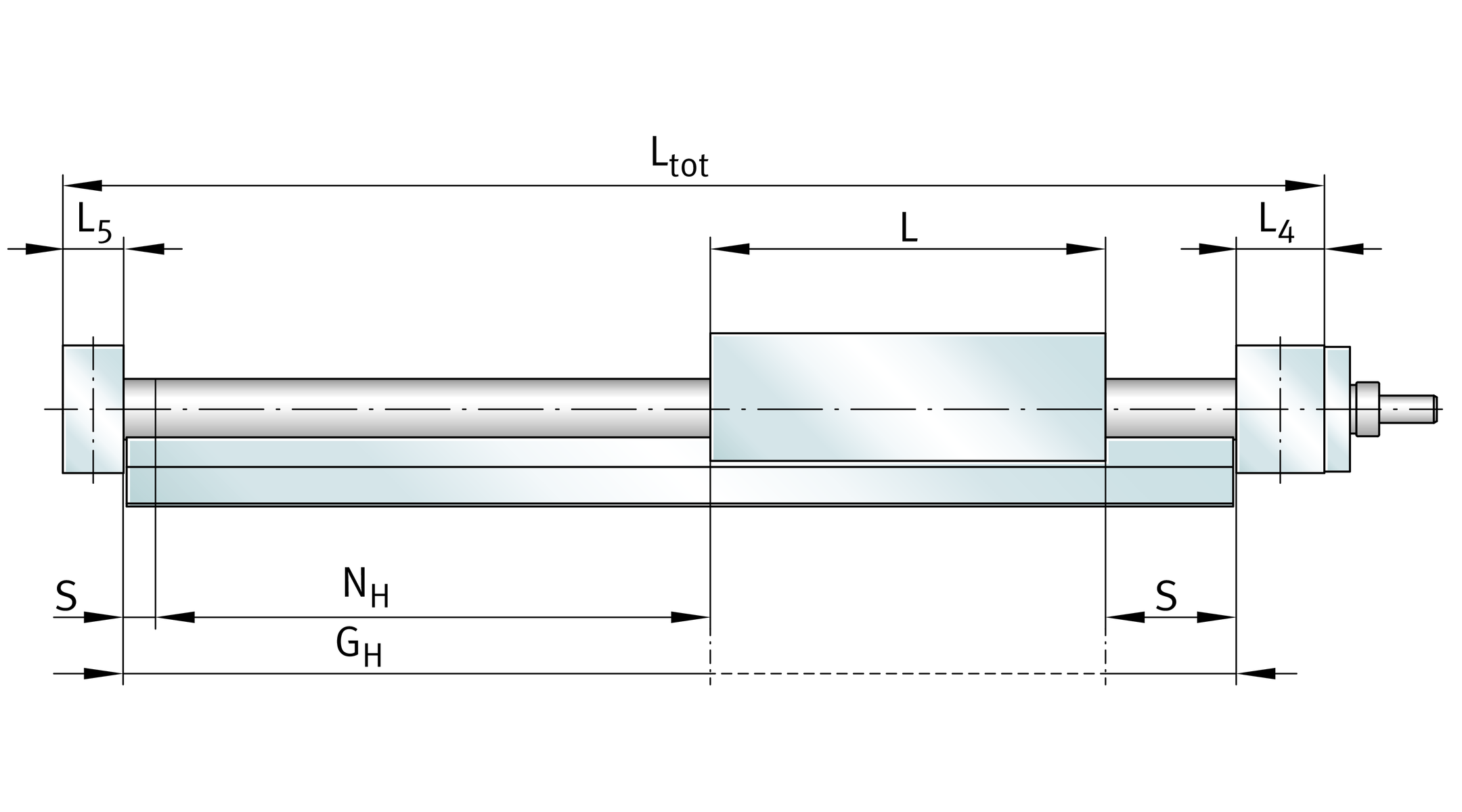
Linear table without bellows
LTS..-TR, LTS..-KGT

Linear table with bellows
LTS..-TR, LTS..-KGT

Length parameters
Designation | L | L4 | L20 | L21 | L5 | S | FBL | BB |
---|---|---|---|---|---|---|---|---|
mm | mm | mm | mm | mm | mm | mm | ||
LTS12-85 | 85 | ‒ | ‒ | ‒ | ‒ | Dependent on application | ‒ | ‒ |
LTS16-100 | 100 | 3,3 | 4 | 1,58 | 29 | |||
LTS20-130 | 130 | 1,43 | 29 | |||||
LTS25-160 | 160 | 1,34 | 29 | |||||
LTS30-180 | 180 | 1,26 | 29 | |||||
LTS40-230 | 230 | 1,27 | 30 | |||||
LTS50-280 | 280 | 1,22 | 30 | |||||
LTS16-100-TR12×3 | 100 | 24 | ‒ | ‒ | 18 | 3 | 1,58 | 21 |
LTS20-130-TR16×4 | 130 | 29 | 20 | 4 | 1,43 | 21 | ||
LTS25-160-TR16×4 | 160 | 33 | 25 | 4 | 1,34 | 21 | ||
LTS30-180-TR20×4 | 180 | 38 | 25 | 4 | 1,26 | 21 | ||
LTS30-180-TR20×8 | 180 | 38 | 25 | 8 | 1,26 | 21 | ||
LTS40-230-TR24×5 | 230 | 39 | 30 | 5 | 1,27 | 22 | ||
LTS40-230-TR24×10 | 230 | 39 | 30 | 10 | 1,27 | 22 | ||
LTS50-280-TR32×6 | 280 | 42 | 30 | 6 | 1,22 | 22 | ||
LTS16-100-1204 | 100 | 24 | 18 | 4 | 1,58 | 21 | ||
LTS16-100-1205 | 100 | 24 | 18 | 5 | 1,58 | 21 | ||
LTS20-130-1605 | 130 | 29 | 20 | 5 | 1,43 | 21 | ||
LTS20-130-1610 | 130 | 29 | 20 | 10 | 1,43 | 21 | ||
LTS25-160-1605 | 160 | 33 | 25 | 5 | 1,34 | 21 | ||
LTS25-160-1610 | 160 | 33 | 25 | 10 | 1,34 | 21 | ||
LTS30-180-2005 | 180 | 38 | 25 | 5 | 1,26 | 21 | ||
LTS30-180-2010 | 180 | 38 | 25 | 10 | 1,26 | 21 | ||
LTS30-180-2020 | 180 | 38 | 25 | 20 | 1,26 | 21 | ||
LTS30-180-2050 | 180 | 38 | 25 | 50 | 1,26 | 21 | ||
LTS40-230-2505 | 230 | 39 | 30 | 5 | 1,27 | 22 | ||
LTS40-230-3210 | 230 | 42 | 30 | 10 | 1,27 | 22 | ||
LTS40-230-3220 | 230 | 42 | 30 | 20 | 1,27 | 22 | ||
LTS40-230-3240 | 230 | 42 | 30 | 40 | 1,27 | 22 | ||
LTS50-280-2505 | 280 | 39 | 30 | 05 | 1,22 | 22 | ||
LTS50-280-3210 | 280 | 42 | 30 | 10 | 1,22 | 22 | ||
LTS50-280-3220 | 280 | 42 | 30 | 20 | 1,22 | 22 | ||
LTS50-280-3240 | 280 | 42 | 30 | 40 | 1,22 | 22 |
Effective length of bellows
The effective length of bellows is the length occupied by the bellows in the fully compressed state. Calculation is based on the total stroke length GH, ➤ Figure, ➤ equation and table.
Effective length calculation
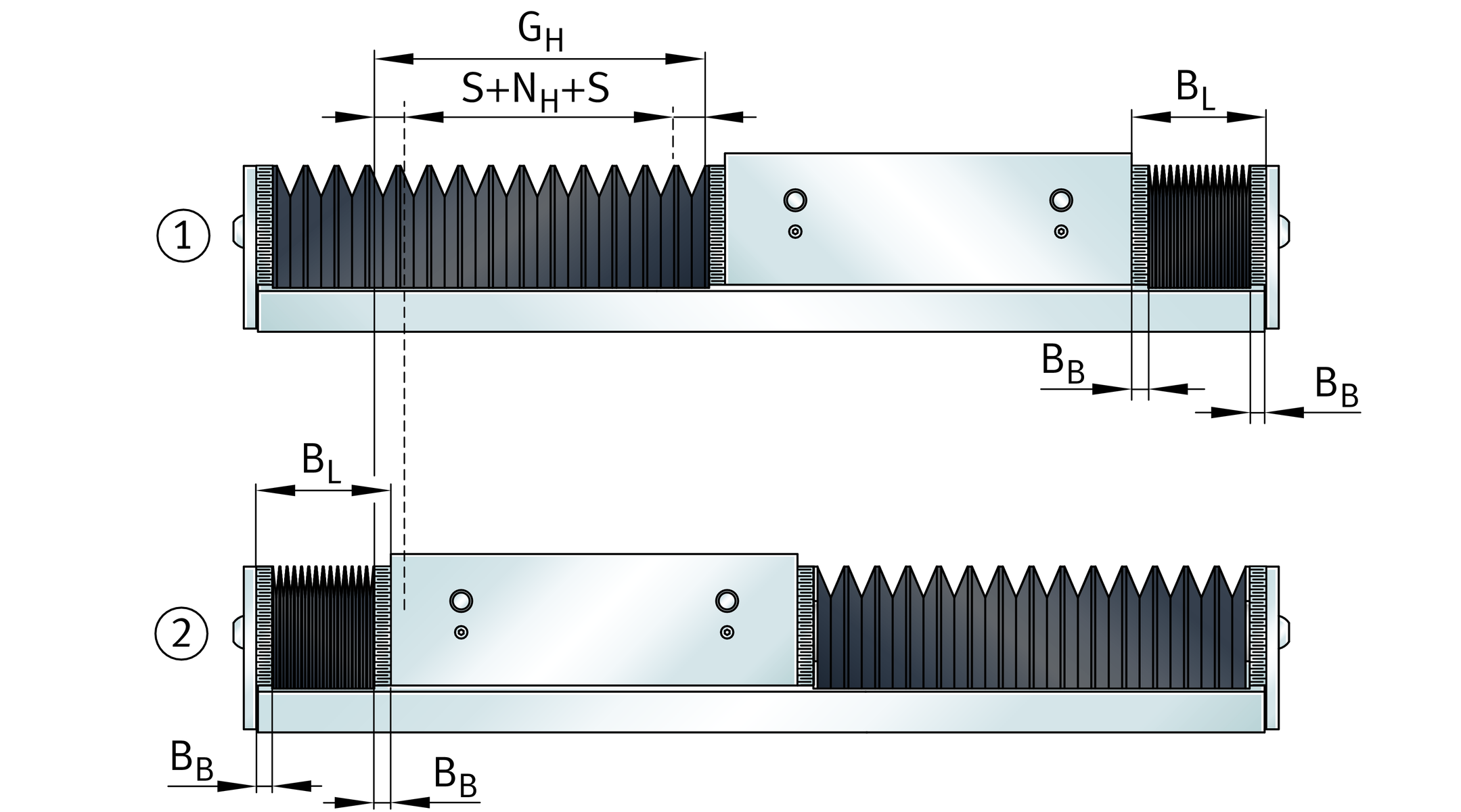


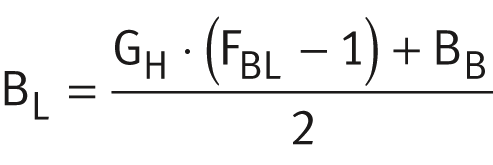
BL | mm | Effective length of bellows |
GH | mm | Total stroke length |
FBL | – | Effective length factor according to linear table type, see table |
BB | mm | Length of bellows fastener. |
Calculation of hole pattern of shaft and support rail units
Shaft and support rail units are supplied as standard with a symmetrical hole pattern. If a symmetrical hole pattern is present: aR = aL. In the following calculation, the values must not be less than the value aR min (aL min).
Parameters for hole pattern calculation
aR, aL | mm | Spacing on right and left between end of shaft and nearest hole centre point |
jL8 | mm | Hole spacing |
Ltot | mm | Total length of table |
n | Number of hole pitches. |
Hole pattern, without drive
The number of hole pitches n is the whole number equivalent to: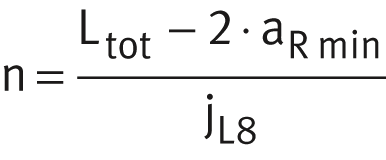

Spacings aR and aL on shaft and support rail units
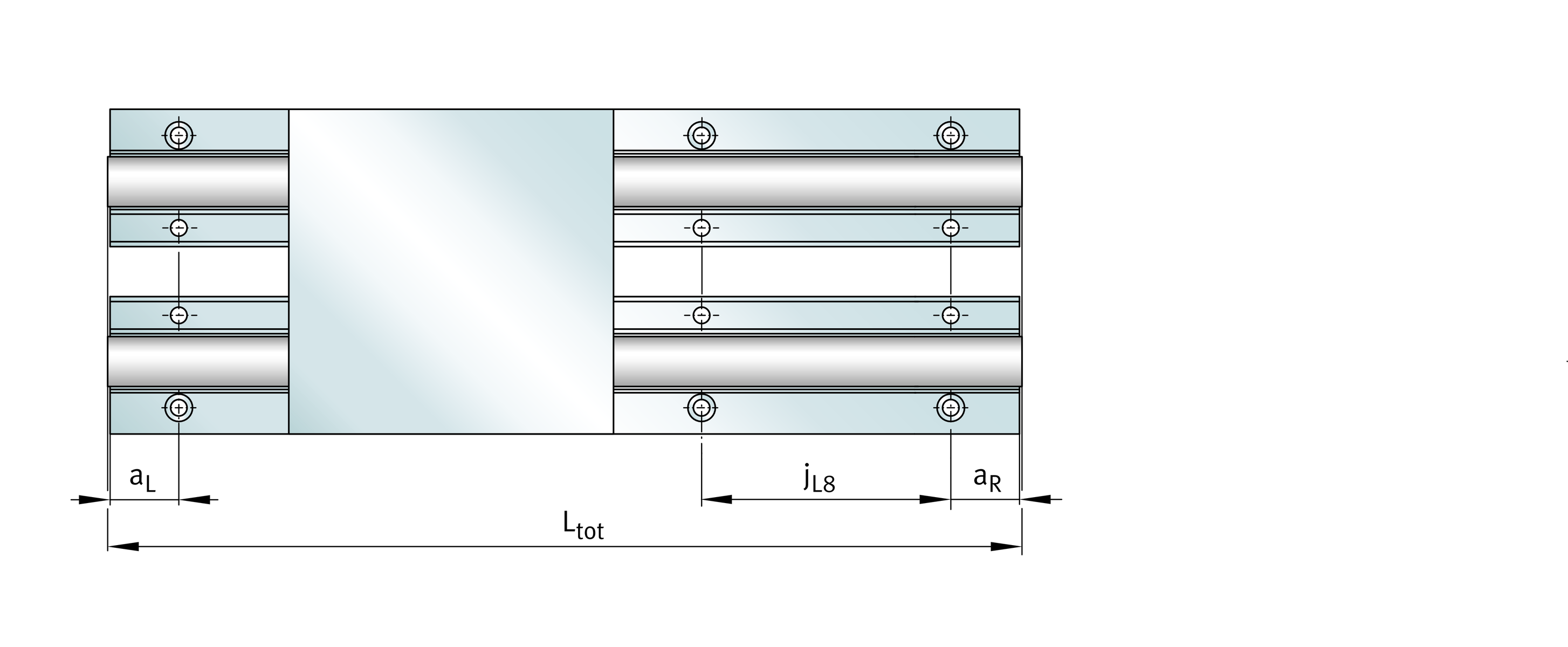
Hole pattern, with drive
The number of hole pitches n is the whole number equivalent to: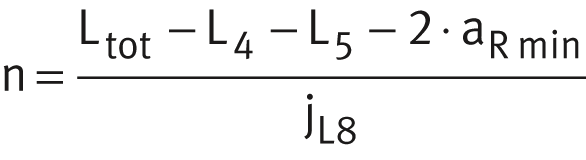

Spacings aR and aL on shaft and support rail units
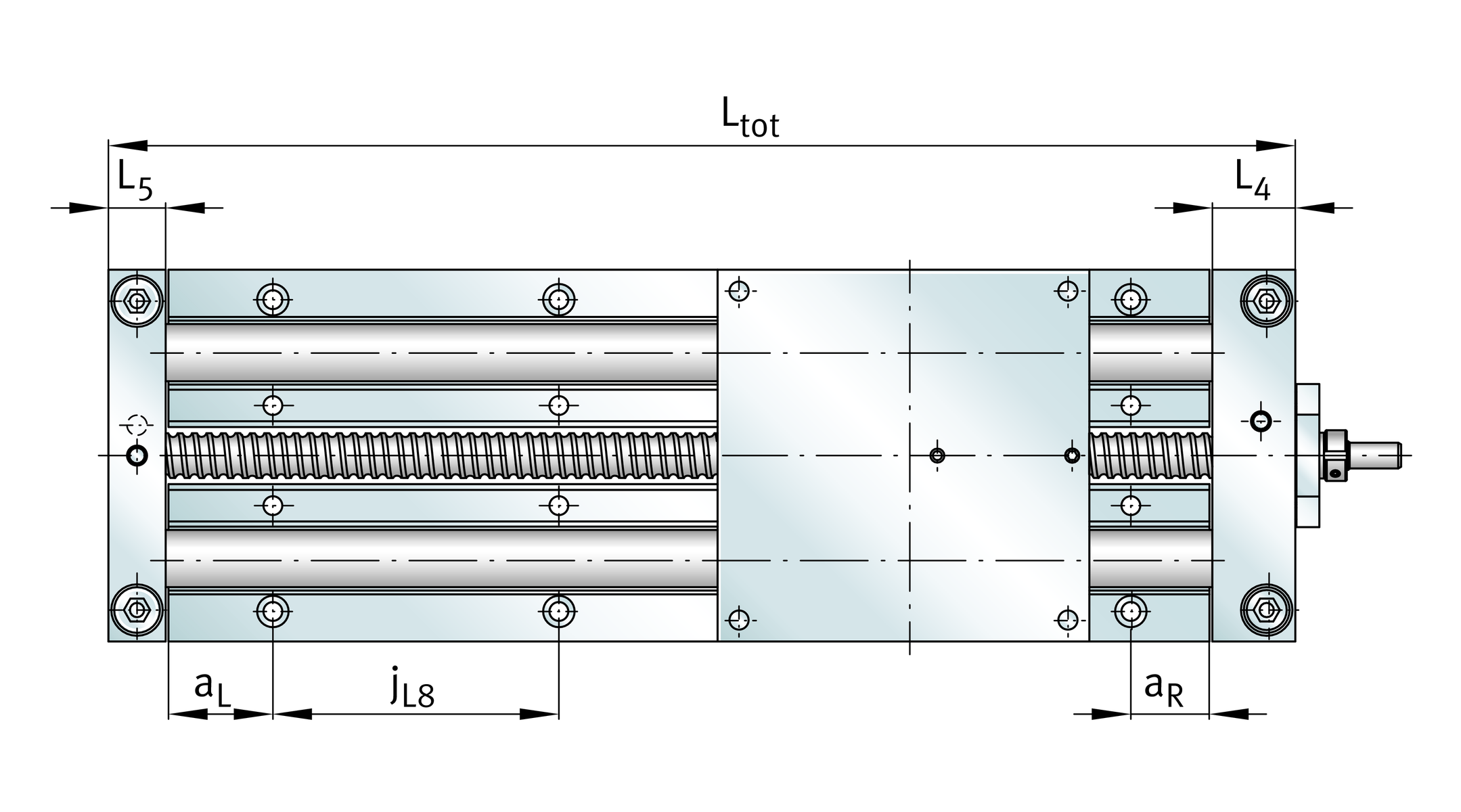
ATTENTION
In the case of a total length L2 < 2 · L + 30, not all fixing holes in the support rail will be accessible, so please consult us.
Mass calculation
The total mass of a linear table is calculated from the mass of the table without a carriage unit and the carriage unit.

Values for mass calculation, linear table without drive
Designation | Mass | |
---|---|---|
Carriage unit | Table without carriage unit | |
mLAW | mBOL | |
≈kg | ≈kg | |
LTS12 | 0,5 | Ltot · 0,003 2 + 0,5 |
LTS16 | 0,8 | Ltot · 0,005 0 + 0,1 |
LTS20 | 1,6 | Ltot · 0,007 6 + 0,14 |
LTS25 | 3 | Ltot · 0,010 6 + 0,21 |
LTS30 | 4,4 | Ltot · 0,015 0 + 0,27 |
LTS40 | 9,1 | Ltot · 0,024 8 + 0,42 |
LTS50 | 16,1 | Ltot · 0,037 8 + 0,62 |
Values for mass calculation, linear table with screw drive
Designation | Mass | |
---|---|---|
Carriage unit** | Table without carriage unit | |
mLAW | mBOL | |
≈kg | ≈kg | |
LTS16..-12 | 0,8 | Ltot · 0,005 8 + 0,46 |
LTS20..-16 | 1,6 | Ltot · 0,008 9 + 0,94 |
LTS25..-16 | 2,9 | Ltot · 0,011 9 + 1,54 |
LTS30..-20 | 4,3 | Ltot · 0,017 1 + 2,07 |
LTS40..-25 | 8,8 | Ltot · 0,028 1 + 3,46 |
LTS40..-32 | 9,2 | Ltot · 0,030 5 + 3,64 |
LTS50..-25 | 15,8 | Ltot · 0,041 1 + 4,94 |
LTS50..-32 | 16,3 | Ltot · 0,043 5 + 5,16 |
**Including single or preloaded double nut.
Lubrication
The information on the lubrication of LTS matches the information on the lubrication of LTE. The only differences are in the relubrication quantities and relubrication points.
Relubrication
Relubrication should be carried out wherever possible with several partial quantities at various times instead of the complete quantity at the time of the relubrication interval. Relubrication quantities, see table. The locating and non-locating bearing in the trapezoidal screw drive are lubricated for life.
Relubrication quantities per lubrication nipple
Designation | Linear ball bearing | d0 | P | Trapezoidal screw drive | Ball screw drive | ||||
---|---|---|---|---|---|---|---|---|---|
Threaded nut | Locating bearing | Non-locating bearing | Threaded nut | Locating bearing | Non-locating bearing | ||||
≈g | mm | mm | ≈g | ≈g | |||||
LTS12 | 0,2 | ‒ | ‒ | ‒ | ‒ | ‒ | ‒ | ‒ | ‒ |
LTS16 | 0,3 | 12 | 3 | ‒ | Lubricated | ‒ | Lubricated | ||
4 | ‒ | 0,2 | |||||||
LTS20 | 0,4 | 16 | 4 | 3,5 | ‒ | ||||
5 | ‒ | 0,5 | |||||||
10 | ‒ | 1,3 | |||||||
LTS25 | 1,1 | 16 | 4 | 3,5 | ‒ | ||||
5 | ‒ | 0,5 | |||||||
10 | ‒ | 1,3 | |||||||
LTS30 | 1,3 | 20 | 4 | 6 | ‒ | ||||
5 | ‒ | 0,6 | |||||||
10 | ‒ | 3,1 | |||||||
20 | ‒ | 3 | |||||||
50 | ‒ | 8,6 | |||||||
LTS40 | 2,5 | 24 | 5 | 10 | ‒ | ||||
25 | 5 | ‒ | 0,8 | ||||||
32 | 10 | ‒ | 3,1 | ||||||
20 | ‒ | 6,8 | |||||||
40 | ‒ | 9,5 | |||||||
LTS50 | 5,5 | 25 | 5 | ‒ | 0,8 | ||||
32 | 6 | 15 | ‒ | ||||||
10 | ‒ | 3,1 | |||||||
20 | ‒ | 6,8 | |||||||
40 | ‒ | 9,5 |
**If relubrication is required due to the application, please consult us.
Relubrication points
The linear ball bearings are greased in pairs in each case via a lateral lubrication nipple in the carriage unit. The spindle nuts are supplied with lubricant via a separate lubrication nipple. The spindle bearing arrangement of the ball screw drive in the shaft support blocks is supplied in each case from above via a lubrication nipple, see ➤ Figure, table, ➤ Figure, and ➤ Figure.
Lubrication points on linear table
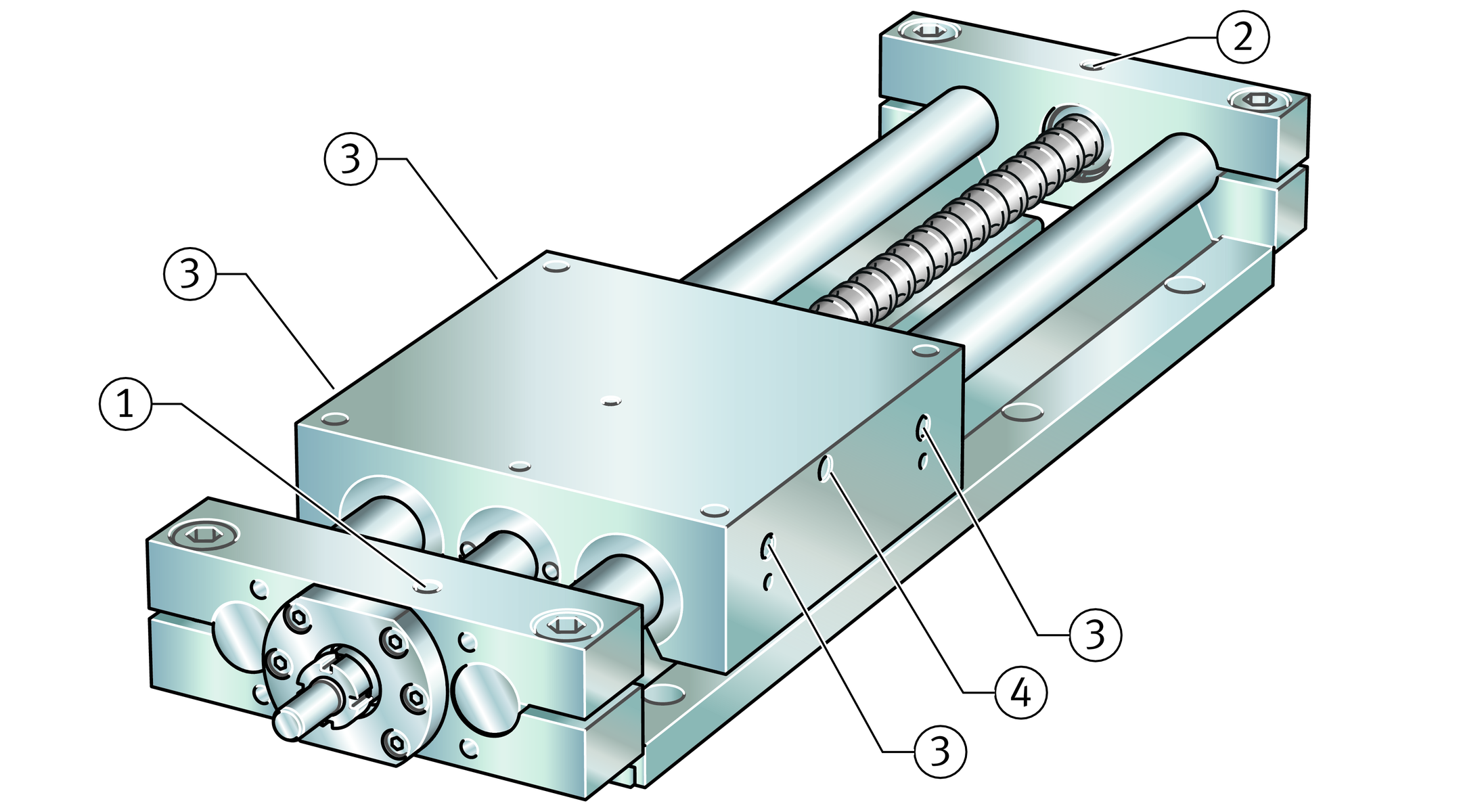




ATTENTION
During lubrication of actuators, all lubrication points on one longitudinal side of a carriage unit must always be provided with lubricant.
Position of relubrication points
Designation | Mounting dimensions | ||||||||||
---|---|---|---|---|---|---|---|---|---|---|---|
Type NIP | Without | With | |||||||||
2×for linear ball bearings | 1×for | 2×for linear ball bearings | Locating bearing | Non-locating bearing | |||||||
h56 | l56 | h56 | l56 | h57 | l57 | b77 | l77 | b78 | l78 | ||
mm | mm | mm | mm | mm | mm | mm | mm | mm | mm | ||
LTS12 | A1 | 10 | 16 | ‒ | |||||||
LTS16 | 14 | 18 | 5,5 | 40 | 14 | 18 | 9,5 | 10,5 | 9 | 9 | |
LTS20 | 15 | 22,5 | 5 | 53,15 | 15 | 22,5 | 12 | 10 | ‒ | 10 | |
LTS25 | A2 | 15 | 29 | 6 | 53,15 | 20 | 29 | 10 | 16 | ‒ | 12,5 |
LTS30 | 20 | 34 | 6 | 56,4** | 20 | 34 | 14 | 14,5 | ‒ | 12,5 | |
LTS40 | 30 | 40 | 8 | 56,4** | 30 | 40 | 13** | 17** | ‒ | 15 | |
LTS50 | A3 | 40 | 50 | 10 | 56,4** | 40 | 50 | ‒ | 17** | ‒ | 15 |
**In the case of a spindle 2020 and 2050, l56 = 52 mm.
**In the case of a spindle 3210 and 3220, l56 = 86 mm.
In the case of a spindle 3240, l56 = 69 mm.
**In the case of a spindle size 25, b77 = 0 mm.
**In the case of a spindle size 25, l77 = 15,5 mm.
Lubrication points
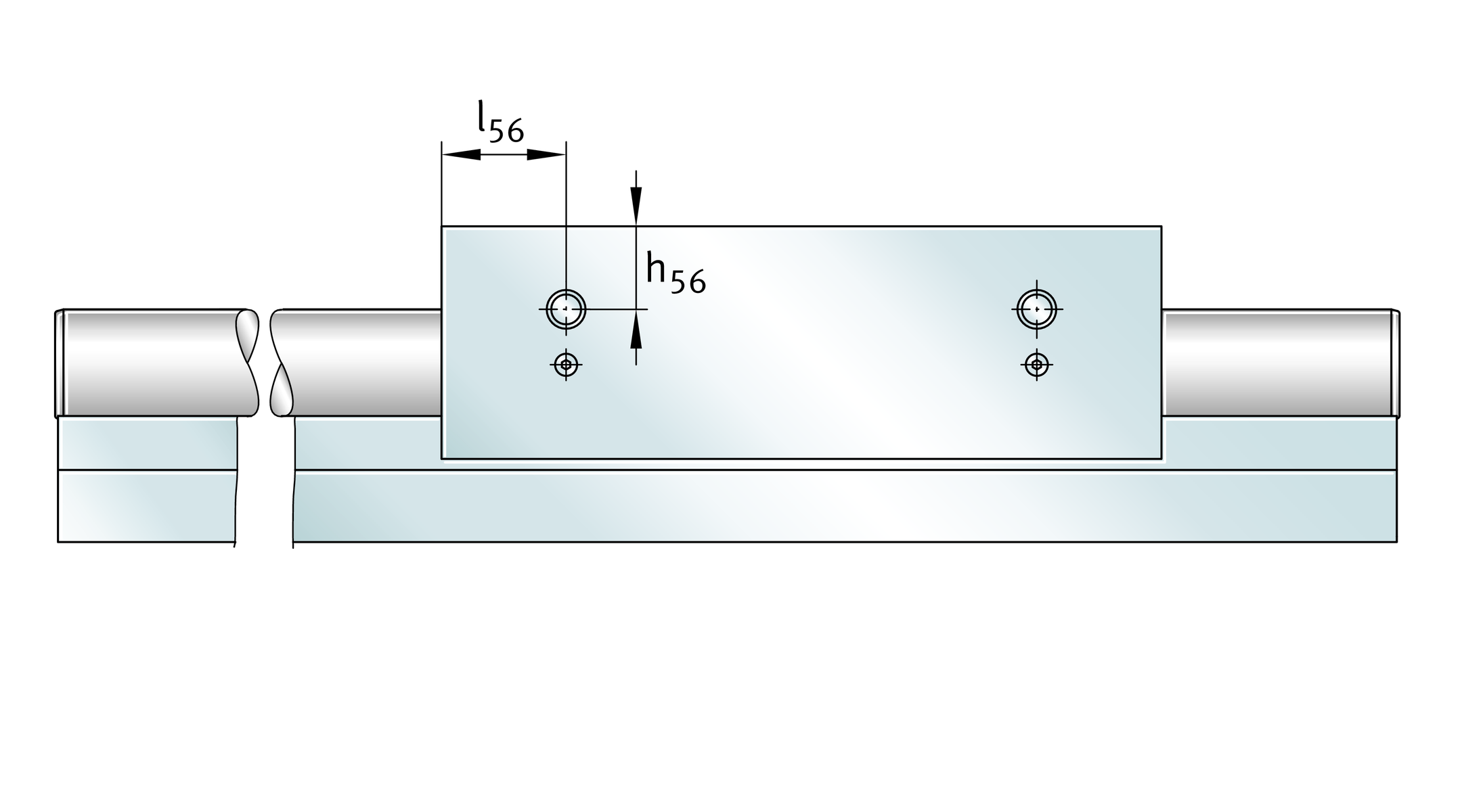
without drive
Position of relubrication points
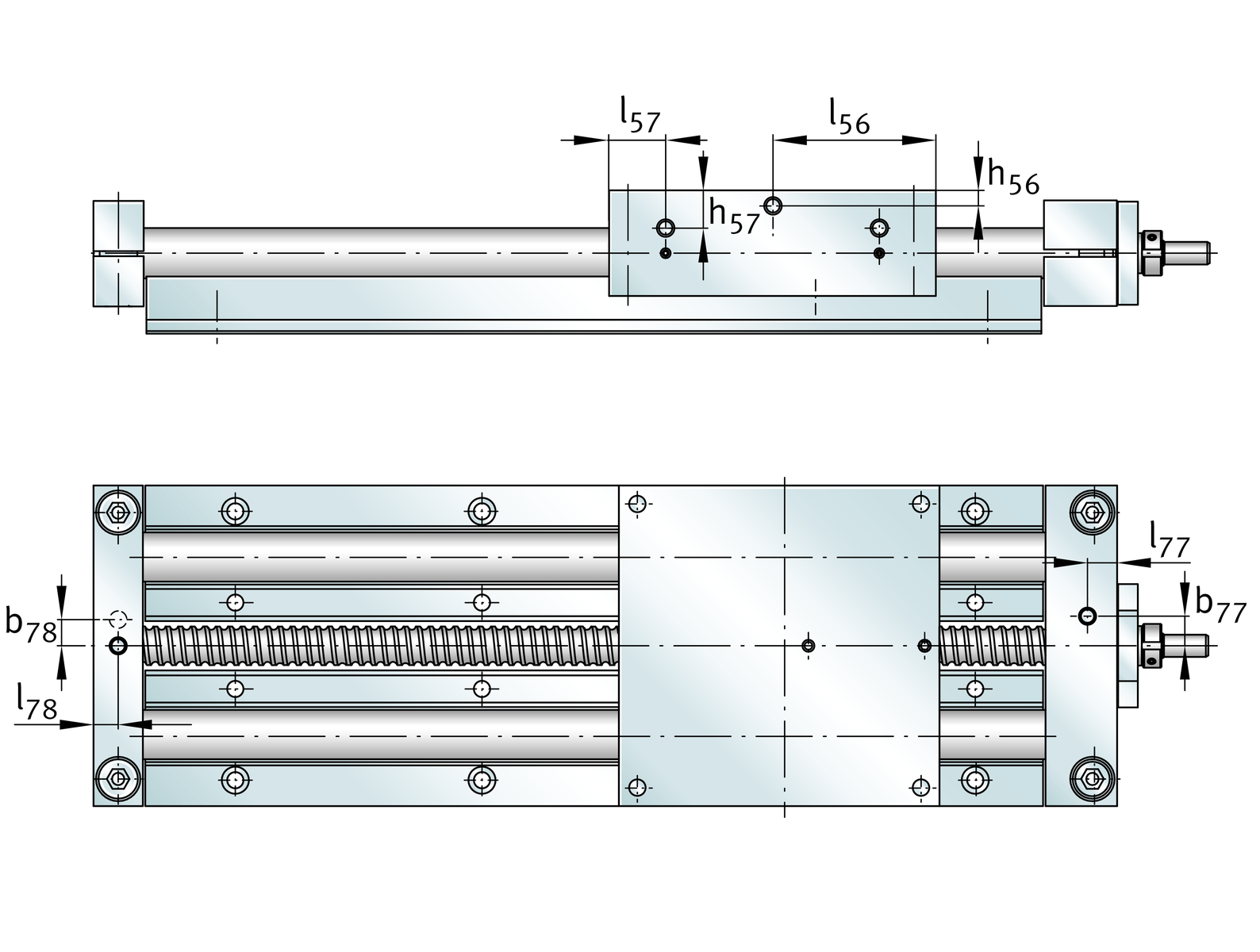
with drive
Maximum permissible spindle speed
Screw drives must not be allowed to run in the critical speed range.
The critical speed is essentially dependent on the following factors:
- spindle length
- spindle diameter
- spindle bearing arrangement
- mounting method.
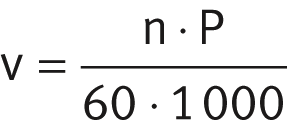
v | m/s | Carriage unit velocity |
n | min–1 | Spindle speed |
P | mm | Spindle pitch. |
The carriage unit velocity v is determined from the spindle speed n and the spindle pitch P. Note the factors influencing the carriage unit velocity, such as maximum values.
Diagram
The diagram shows the relationship for individual series and sizes between the critical speed and the spindle length, ➤ Figure. The diagram takes account of the effective length BL of the bellows cover. Definition of the effective length, see link.
Maximum permissible spindle speed without spindle supports
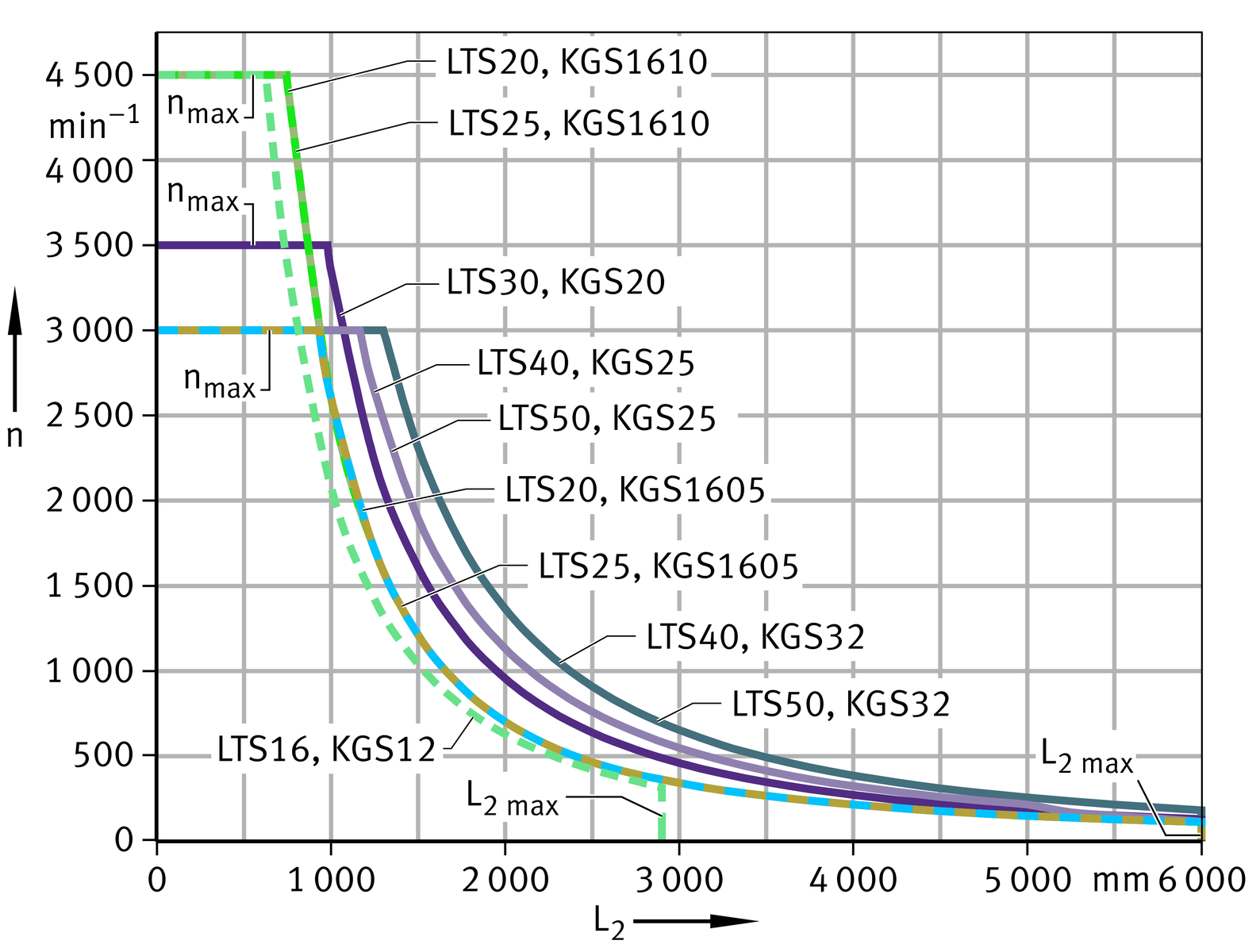
Mounting requirements
The information on the mounting position and mounting arrangement of LTS matches the information on the mounting position and mounting arrangement of LTE. At this point, only deviating or additional information will be covered.
Overlong tables
In the case of very long linear tables LTS, one support rail must first be aligned by means of the shaft and screw mounted in stages. The support rail arranged in parallel is aligned by moving the carriage, thus ensuring the centre spacing of the support rail. In the case of parallel support rails, the linear table must be located by an additional form fit on the adjacent construction. The datum support rail should be clamped against a stop, ➤ Figure.
Alignment of a shaft and support rail unit by means of the shaft
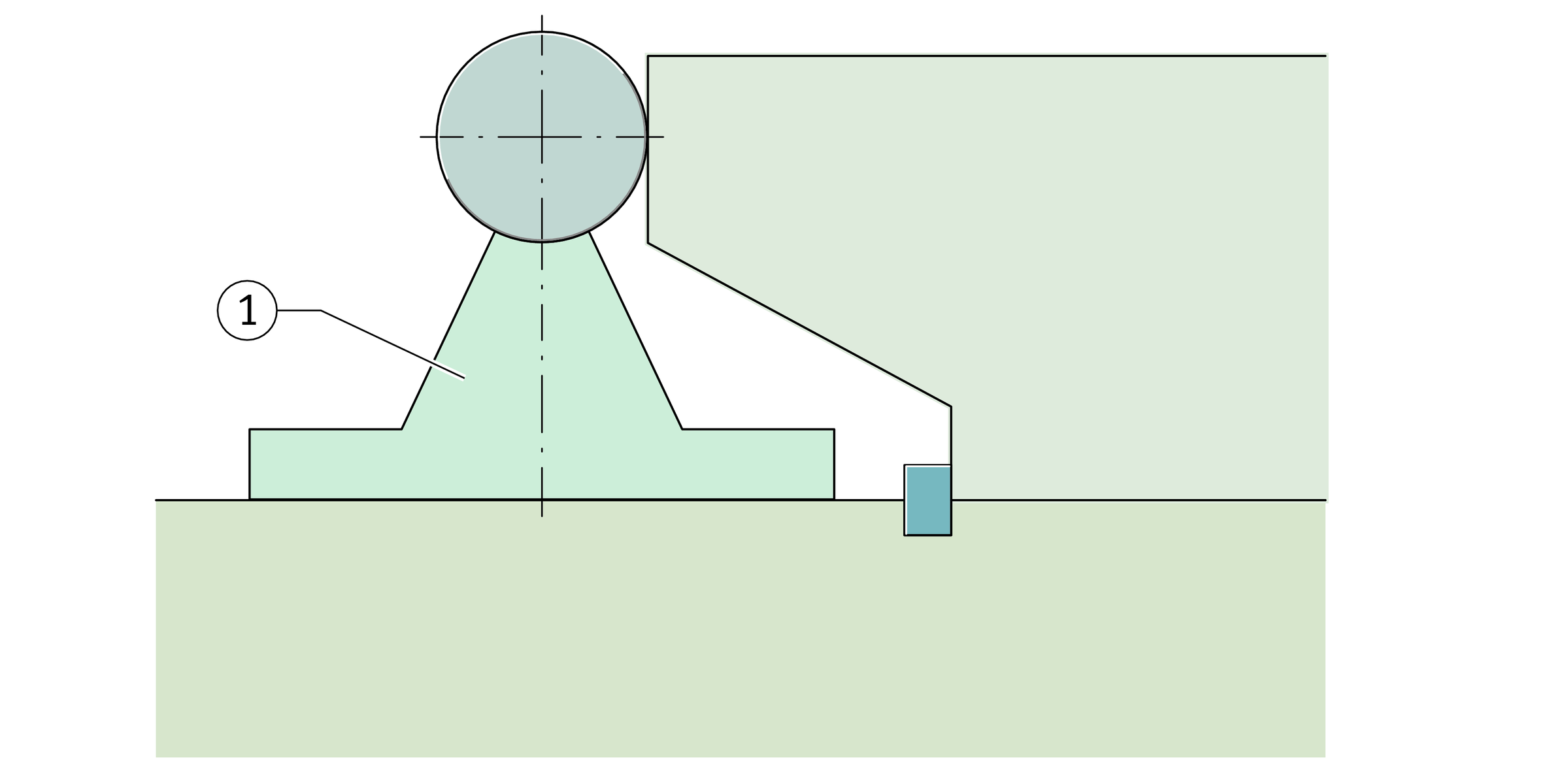

Accuracy
Length tolerances
The length tolerances for linear tables can be taken from ➤ Figure and the table.
Length tolerances
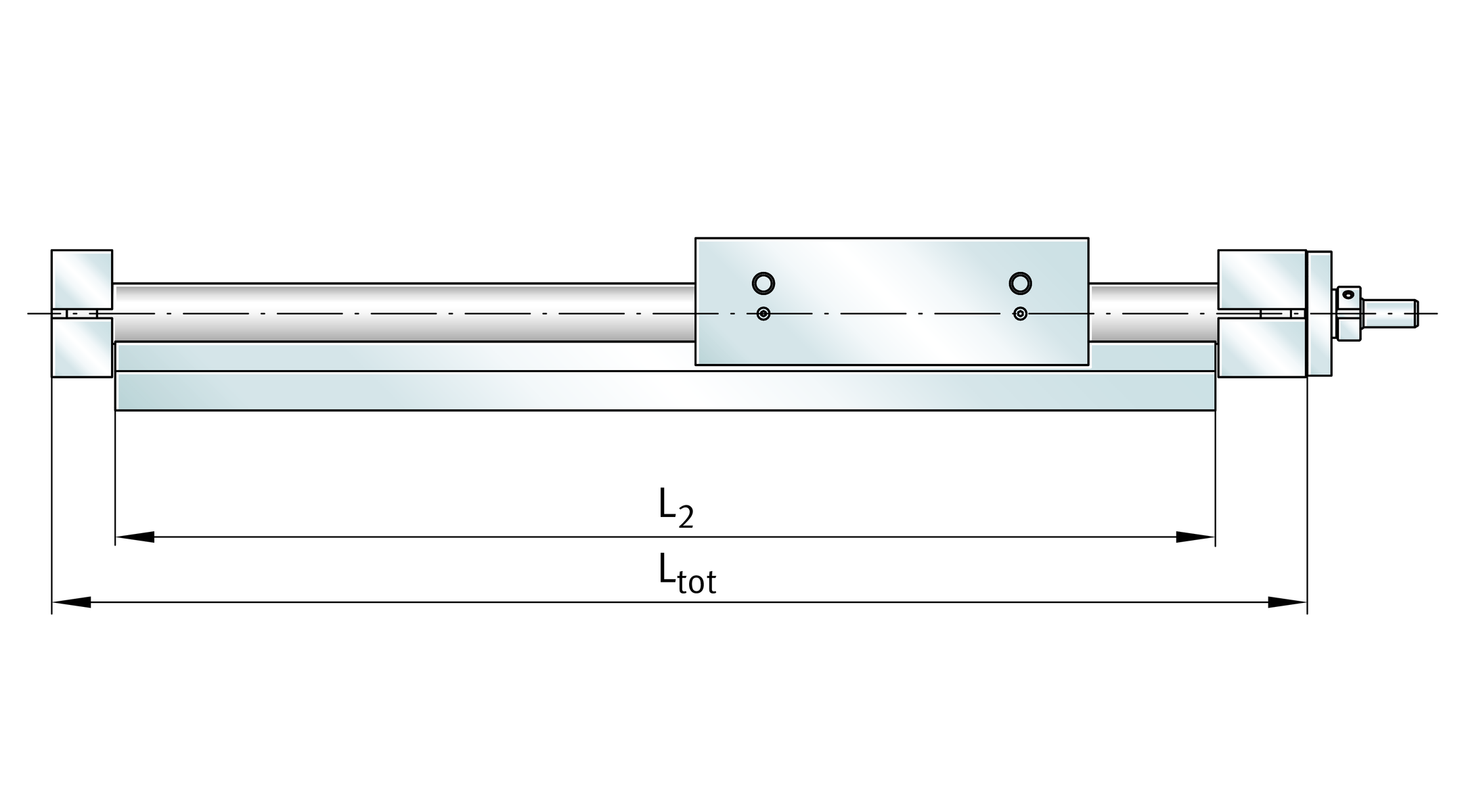
Tolerances
Total length Ltot of linear tables LTS | Tolerance | |||
---|---|---|---|---|
mm | mm | |||
Ltot < | 400 | ±0,5 | ||
400 | ≦ | Ltot < | 1 000 | ±0,8 |
1 000 | ≦ | Ltot < | 2 000 | ±1,2 |
2 000 | ≦ | Ltot < | 4 000 | ±2 |
4 000 | ≦ | Ltot < | 5 850 | ±3 |
Accuracy of the screw drive
Linear tables with trapezoidal screw drive are only available with a single nut with clearance, see table. The pitch accuracy is dependent on the size, see table.
Linear tables with ball screw drive are available with a single nut with clearance, see table. Where higher accuracy requirements are present, preloaded (clearance-free) double nuts are possible for many pitch values, see table.
ATTENTION
In the case of standard linear tables with ball screw drive, the nut unit (double nut) can only be preloaded clearance-free if the spindle pitch P is less than the nominal diameter d0 of the spindle.
Trapezoidal screw drive
Designation | Spindle | Spindle nut | |||||
---|---|---|---|---|---|---|---|
Nominal | Pitch | Single nut | |||||
d0 | P | Accuracy | Suffix | Axial clearance | |||
mm |
mm | μm each 300 mm |
mm | ||||
LTS16 | 12 | 3 | 300 | M | 0,4 | to | 0,5 |
LTS20 | 16 | 4 | 50 | ||||
LTS25 | 16 | 4 | 50 | ||||
LTS30 | 20 | 4 | 50 | ||||
8 | 200 | ||||||
LTS40 | 24 | 5 | 50 | ||||
10 | 200 | ||||||
LTS50 | 32 | 6 | 50 |
Ball screw drive
Designation | Spindle | Spindle nut | |||||
---|---|---|---|---|---|---|---|
⌀ d0 | P | Pitch accuracy | Single nut | Double nut | |||
Suffix | Axial clearance | Suffix | Axial clearance | ||||
mm |
mm | μm each 300 mm |
mm | ||||
LTS16 | 12 | 4 | 50 | M | 0,05 | ‒ | ‒ |
LTS20 | 16 | 5 | 50 | M | 0,05 | MM | Preloaded |
10 | ‒ | ‒ | |||||
LTS25 | 16 | 5 | 50 | M | 0,05 | MM | Preloaded |
10 | |||||||
LTS30 | 20 | 5 | 50 | M | 0,05 | MM | Preloaded |
10 | |||||||
20 | ‒ | ‒ | |||||
50 | |||||||
LTS40 | 25 | 5 | 50 | M | 0,05 | MM | Preloaded |
32 | 10 | ||||||
20 | |||||||
50 | ‒ | ‒ | |||||
LTS50 | 25 | 5 | 50 | M | 0,05 | MM | Preloaded |
32 | 10 | ||||||
20 | |||||||
50 | ‒ | ‒ |