Table of contents
Drawn cup needle roller bearings
- Bearing design
- Load carrying capacity
- Compensation of angular misalignments
- Lubrication
- Sealing
- Speeds
- Noise
- Temperature range
- Cages
- Internal clearance
- Dimensions, tolerances
- Suffixes
- Structure of bearing designation
- Dimensioning
- Minimum load
- Design of bearing arrangements
- Mounting and dismounting
- Legal notice regarding data freshness
- Further information
Drawn cup needle roller bearings
The bearings:
- are particularly suitable for applications with a very small radial section height on account of their very low cross-sectional height ➤ Figure
- are used if the housing bore is not suitable as a raceway for needle roller and cage assemblies
- can support high radial loads (are pure radial bearings) ➤ Figure, ➤ Figure, ➤ Figure, ➤ Figure
- require a considerably smaller radial design envelope than machined needle roller bearings ➤ Figure
- usually run directly on the shaft (no inner ring) ➤ Figure, ➤ Figure
- permit relatively high speeds
- are easy to mount ➤ section
- require no additional means of axial retention (as a result of which the housing bore is easy to produce) ➤ section
- can be readily used to close off the shaft ends of bearing positions (drawn cup needle roller bearings with closed end) ➤ Figure
- result in particularly compact, cost-effective and economical bearing arrangements
Comparison of radial design envelope
|
![]() |
Bearing design
Design variants
Drawn cup needle roller bearings with open ends are available as:
- standard drawn cup needle roller bearings with open ends and cage ➤ Figure and ➤ Figure
- full complement drawn cup needle roller bearings with open ends ➤ Figure
- special bearings ➤ link and ➤ link
Drawn cup needle roller bearings with closed end are available as:
- standard drawn cup needle roller bearings with closed end ➤ Figure
- special bearings ➤ link and ➤ link
- universal joint bearings ➤ link
Drawn cup needle roller bearings
The outer rings are thin‑walled and produced by forming methods
Drawn cup needle roller bearings are part of the group of radial needle roller bearings. These ready-to-fit bearing arrangement elements are rolling bearings with a very small radial section height. They comprise thin-walled, drawn cup outer rings and needle roller and cage assemblies which together form a complete unit ➤ Figure, ➤ Figure, ➤ Figure, ➤ Figure. The cage guides the needle rollers parallel to the axis in pockets.
For bearing arrangements with a very small radial design envelope
Due to the thin-walled outer cup and the absence of an inner ring, the bearings have a very low cross-sectional height ➤ Figure. As a result, they are particularly suitable for applications with a very small radial design envelope. The majority of the bearings are of a single row design and do not have a lubrication hole.
Drawn cup needle roller bearings can also be combined with inner rings IR or LR
Due to the absence of an inner ring, drawn cup needle roller bearings require a hardened and ground bearing raceway on the shaft ➤ section. If the shaft cannot be produced as a rolling bearing raceway, the bearings can be combined with inner rings IR or LR ➤ Figure. If wider inner rings are used, these can also serve as the running surface for sealing rings G and SD ➤ Figure.
Drawn cup needle roller bearings with open ends and inner ring
|
![]() |
Standard drawn cup needle roller bearings with open ends and cage
In contrast to drawn cup needle roller bearings with closed end, the bearings are open
Drawn cup needle roller bearings of this design are open at both ends and have the basic designation HK ➤ Figure and ➤ section. They are supplied with needle roller and cage assemblies. Bearings with needle roller and cage assemblies allow higher speeds than the full complement designs. The bearings are available in open and sealed versions ➤ Figureand ➤ section. Double row designs have a lubrication hole in the outer cup and the suffix ZW ➤ Figure.
Single row drawn cup needle roller bearings with open ends Fr = radial load
|
![]() |
Double row drawn cup needle roller bearing with open ends Fr = radial load
|
![]() |
Full complement drawn cup needle roller bearings with open ends
Particularly high load carrying capacity within a very small radial design envelope
Full complement drawn cup needle roller bearings with open ends have the basic designation HN ➤ Figure. As these bearings have the maximum number of needle rollers, they offer extremely high load carrying capacity. However, they do not permit the speeds that are possible when drawn cup needle roller bearings with open ends are used in conjunction with rolling elements retained by a cage.
Full complement drawn cup needle roller bearing with open ends Fr = radial load |
![]() |
Drawn cup needle roller bearings with closed end
In contrast to drawn cup needle roller bearings with open ends, the bearings are closed at one end
Drawn cup needle roller bearings of this design are closed at one end ➤ Figure. They are thus suitable for closing off the shaft ends of bearing positions. This gives protection against injury by rotating shafts and protects the bearings against contamination and moisture. Depending on the size, the base is either smooth or lock-beaded (stiffened). The profiled base can also support small axial guidance forces. Drawn cup needle roller bearings with closed end are available in open and sealed versions ➤ Figure and ➤ section.
Drawn cup needle roller bearings with closed end Fr = radial load
|
![]() |
Special bearings
In addition to the standard catalogue range, special designs are available by agreement:
- with enveloping circle Fw from 2 mm to 100 mm
- for special noise requirements (bearings with special noise testing)
Universal joint bearings
For universal joints, universal joint bearings of series BU and BBU are available by agreement.
Load carrying capacity
The bearings are pure radial bearings
Drawn cup needle roller bearings can support high radial forces, but may only be subjected to radial load. If the bearing position is also required to support axial forces, the bearings can, for example, be combined with axial needle roller bearings AXW ➤ Figure.
Drawn cup needle roller bearing with open ends combined with axial needle roller bearing Fr = radial load Fa = axial load
|
![]() |
Compensation of angular misalignments
The bearings are not suitable for the compensation of shaft misalignments relative to the housing
Drawn cup needle roller bearings are not suitable for the compensation of angular misalignments. The extent to which a misalignment of the shaft can be tolerated relative to the housing bore is dependent on factors such as the design of the bearing position, the size of the bearing, the operating clearance and the load. For this reason, it is not possible to give a guide value for misalignment.
In all cases, misalignments cause increased running noise, place increased strain on the cages and have a harmful influence on the operating life of the bearings.
Lubrication
Greased bearings
Sealed bearings are greased with a lithium complex soap grease to GA08. The grease filling is measured so that it is sufficient for the entire operating life of the bearing. As a result, the bearings are maintenance-free.
Greased bearings should not be washed out or heated to temperatures of > +80 °C prior to mounting.
Ungreased bearings
Ungreased bearings must be lubricated with oil or grease. The majority of single row bearings do not have a lubrication hole.
Compatibility with plastic cages
When using bearings with plastic cages, compatibility between the lubricant and the cage material must be ensured if synthetic oils, lubricating greases with a synthetic oil base or lubricants containing a high proportion of EP additives are used.
Observe oil change intervals
Aged oil and additives in the oil can impair the operating life of plastics at high temperatures. As a result, stipulated oil change intervals must be strictly observed.
Lubrication of full complement drawn cup needle roller bearings with open ends
The needle rollers are retained by a special grease
Since the needle rollers in full complement bearings are not retained by mechanical means (no cage is present), they are retained for transport and fitting by means of a special grease (DIN 51825-K1/2K-30). However, this grease does not have an adequate long term lubrication capacity. Relubrication is therefore recommended after fitting.
If there is any uncertainty regarding relubrication, please consult Schaeffler.
Bearings of special design
The following special designs are available by agreement:
- unsealed bearings, greased using a lithium complex soap grease to GA08 (suffix GA08)
- bearings with a lubrication hole for sizes from HK0609 (suffix AS1)
Sealing
The bearings are open or sealed
Drawn cup needle roller bearings are available in an open design in accordance with DIN 618:2008 (ISO 3245:2015) and a sealed design in accordance with DIN 618:2008.
Sealed bearings
Integrated seals are particularly space-saving
Under normal operating conditions, contact seals give protection against contamination, spray water and the loss of lubricant. The integration of such seals into the bearing provides a compact, reliable, proven and economical sealing solution.
Unsealed bearings
Provide seals in the adjacent construction
In the case of unsealed bearings, sealing of the bearing position must be carried out in the adjacent construction. This must reliably prevent:
- moisture and contaminants from entering the bearing
- the egress of lubricant from the bearing
Sealing of the bearing position with sealing rings G or SD
Effective sealing elements for use in sealing open bearings
Bearing positions with open drawn cup needle roller bearings can be sealed economically using sealing rings G or SD. The sealing rings are designed as contact seals and are arranged in front of the bearing ➤ Figure, ➤ Figure. They are suitable for circumferential velocities at the running surface of up to 10 m/s and protect the bearing position reliably against contamination, spray water and excessive loss of lubricant. The sealing rings are matched to the low radial dimensions of drawn cup needle roller bearings with open ends. They are very easy to fit, since they are simply pressed into the housing bore.
Sealing of the bearing position with sealing rings G or SD
|
![]() |
Speeds
Limiting speeds and reference speeds in the product tables
Two speeds are generally indicated in the product tables:
- the kinematic limiting speed nG
- the thermal speed rating nϑr
Limiting speed
The limiting speed nG is the kinematically permissible speed of a bearing. Even under favourable mounting and operating conditions, this value should not be exceeded without prior consultation with Schaeffler ➤ link. The values in the product tables are valid for oil lubrication.
Values for grease lubrication
For the grease lubrication of open cage bearings, 60% of the value stated in the product tables is permissible in each case.
Speeds for full complement bearings
Due to the bearing kinematics and higher temperatures within the bearing, the speeds for full complement bearings are lower than for bearings with a cage.
Reference speeds
nϑr is used to calculate nϑ
The thermal speed rating nϑr is not an application-oriented speed limit, but is a calculated ancillary value for determining the thermally safe operating speed nϑ ➤ link.
Bearings with contact seals
For bearings with contact seals, no speed ratings are defined in accordance with DIN ISO 15312:2004. As a result, only the limiting speed nG is given in the product tables for these bearings.
Noise
Schaeffler Noise Index
The Schaeffler Noise Index (SGI) is not yet available for this bearing type ➤ link. The data for these bearing series will be introduced and updated in stages.
Temperature range
Limiting values
The operating temperature of the bearings is limited by:
- the dimensional stability of the bearing rings and rolling elements
- the cage
- the lubricant
- the seals
Possible operating temperatures of drawn cup needle roller bearings ➤ Table.
Permissible temperature ranges
Operating temperature |
Open drawn cup |
Sealed drawn cup needle roller bearings |
|
---|---|---|---|
with sheet steel cage or full complement |
with polyamide cage PA66 |
||
|
–30 °C to +140 °C |
–20 °C to +120 °C |
–20 °C to +100 °C, limited by the lubricant and seal material |
In the event of anticipated temperatures which lie outside the stated values, please contact Schaeffler.
Cages
Sheet steel cages are used as standard
With only a few exceptions, the cages are made from sheet steel. Bearings with a plastic cage have the suffix TV. Other cage designs are available by agreement. With such cages, however, suitability for high speeds and temperatures as well as the basic load ratings may differ from the values for the bearings with standard cages.
For high continuous temperatures and applications with difficult operating conditions, bearings with sheet steel cages should be used. If there is any uncertainty regarding cage suitability, please consult Schaeffler.
Internal clearance
The enveloping circle diameter Fw applies instead of the radial internal clearance
In the case of bearings without an inner ring, the dimension for the inner enveloping circle diameter Fw is used instead of the radial internal clearance. The enveloping circle is the inner inscribed circle of the needle rollers in clearance-free contact with the outer raceway. Once the bearings are mounted, the inner enveloping circle diameter Fw is approximately in tolerance class F8. The precondition for this is that the bore tolerances are observed for bearings without an inner ring ➤ section, ➤ Table and ➤ Table.
Checking the enveloping circle diameter Fw
Fw can only be checked in a mounted condition
In the case of drawn cup needle roller bearings, the inner enveloping circle diameter Fw can only be checked once the bearings are mounted. In order to carry out the check, the bearing is pressed into a steel ring gauge, which has a cylindrical bore with the nominal dimension D and lower deviation of tolerance class N6 (in accordance with ISO 286-2). The ring gauge must have a minimum wall thickness of 20 mm, the minimum width must correspond to the width of the bearing. A plug gauge to ISO 1132-2 is used for checking purposes. The tolerance class of the enveloping circle is within the range of values defined in the table ➤ Table.
Example
Example of checking of Fw
For drawn cup needle roller bearing with open ends HK1010 (Fw = 10 mm), Fw must be between 10,013 mm and 10,031 mm, the ring gauge bore must be 13,980 mm (lower deviation = +13 μm, upper deviation = +31 μm) ➤ Table.
Bearings intended for enveloping circle measurements should not be repeatedly pushed in and out of the gauge. Bearings that have been checked in the ring gauge should not be used again.
Ring gauge bore and enveloping circle deviations (to DIN 618:2008)
Enveloping circle |
Outside diameter |
Ring |
Enveloping circle deviation |
|
---|---|---|---|---|
Upper |
Lower |
|||
Fw mm |
D mm |
mm |
μm |
μm |
2 3 |
4,6 6,5 |
4,587 6,484 |
+24 +24 |
+6 +6 |
4 5 6 |
8 9 10 |
7,984 8,984 9,984 |
+28 +28 +28 |
+10 +10 +10 |
7 8 9 10 |
11 12 13 14 |
10,980 11,980 12,980 13,980 |
+31 +31 +31 +31 |
+13 +13 +13 +13 |
12 12 13 14 15 16 17 18 |
16 18 19 20 21 22 23 24 |
15,980 17,980 18,976 19,976 20,976 21,976 22,976 23,976 |
+34 +34 +34 +34 +34 +34 +34 +34 |
+16 +16 +16 +16 +16 +16 +16 +16 |
20 22 25 28 30 |
26 28 32 35 37 |
25,976 27,976 31,972 34,972 36,972 |
+41 +41 +41 +41 +41 |
+20 +20 +20 +20 +20 |
32 35 40 45 50 |
39 42 47 52 58 |
38,972 41,972 46,972 51,967 57,967 |
+50 +50 +50 +50 +50 |
+25 +25 +25 +25 +25 |
55 60 |
63 68 |
62,967 67,967 |
+60 +60 |
+30 +30 |
Dimensions, tolerances
The dimensions of special bearings (F../Z..) may deviate from the standard.
Dimension standards
The main dimensions of the bearings correspond to DIN 618:2008 and ISO 3245:2015, where standardised. Nominal dimensions of bearings ➤ link.
Tolerances
The tolerances correspond to DIN 618:2008 (ISO 3245:2015), where standardised. The inner enveloping circle diameter Fw is approximately in tolerance class F8 ➤ section.
Suffixes
For a description of the suffixes used in this chapter ➤ Table and medias interchange http://www.schaeffler.de/std/1B69.
Suffixes and corresponding descriptions
Suffix |
Description of suffix |
|
---|---|---|
AS1 |
With lubrication hole from HK0609 |
Special design, available by agreement |
GA08 |
Unsealed, greased bearings for operating temperatures from –20 °C to +140 °C |
Special design, available by agreement |
RS |
Contact seal on one side |
Standard |
TV |
Cage made from glass fibre reinforced polyamide PA66 |
Standard |
ZW |
Double row design, with lubrication hole |
Standard |
2RS |
Contact seal on both sides |
Standard |
Structure of bearing designation
The designation of bearings follows a set model. Examples ➤ Figure and ➤ Figure. The composition of designations is subject to DIN 623‑1 ➤ Figure.
Drawn cup needle roller bearing with closed end, open version: designation structure |
![]() |
Drawn cup needle roller bearing with open ends, sealed on both sides: designation structure |
![]() |
Dimensioning
Equivalent dynamic bearing load
P = Fr under purely radial load of constant magnitude and direction
The basic rating life equation L = (Cr/P)p used in the dimensioning of bearings under dynamic load assumes a load of constant magnitude and direction. In radial bearings, this is a purely radial load Fr ➤ section. The bearing load Fr is therefore used in the rating life equation for P (P = Fr) ➤ Equation.
Equivalent dynamic load
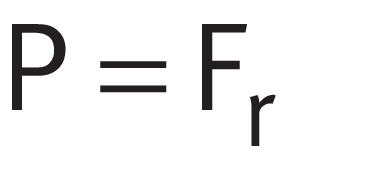
Legend
P | N |
Equivalent dynamic bearing load |
Fr | N |
Radial load |
Equivalent static bearing load
For drawn cup needle roller bearings subjected to static load ➤ Equation.
Equivalent static load
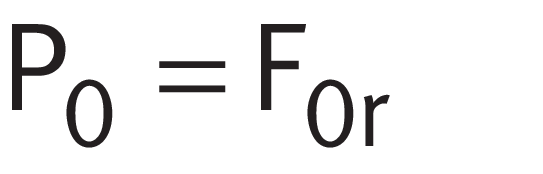
Legend
P0 | N |
Equivalent static bearing load |
F0r | N |
Largest radial load present (maximum load) |
Static load safety factor
S0 = C0/P0
In addition to the basic rating life L (L10h), it is also always necessary to check the static load safety factor S0 ➤ Equation. For drawn cup needle roller bearings, S0 ≧ 3 is necessary.
Static load safety factor
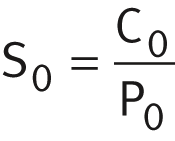
Legend
S0 | - |
Static load safety factor |
C0 | N |
Basic static load rating |
P0 | N |
Equivalent static bearing load |
Minimum load
In order to prevent damage due to slippage, a minimum radial load of P > C0r/60 is required
In order that no slippage occurs between the contact partners, the drawn cup needle roller bearings must be constantly subjected to a sufficiently high load. Based on experience, a minimum radial load of the order of P > C0r/60 is thus necessary. In most cases, however, the radial load is already higher than the requisite minimum load due to the weight of the supported parts and the external forces.
If the minimum radial load is lower than indicated above, please consult Schaeffler.
Design of bearing arrangements
Radial location of bearings
Support outer cup/ inner ring over entire circumference and width
In order to allow full utilisation of the load carrying capacity of the bearings and thus also achieve the requisite rating life, sufficient rigid support must be provided for the thin-walled outer cups in the housing. Due to the thin‑walled outside surface, the bearings only adopt their precise geometry once they have a tight fit. The support for the outer cup in the housing bore can be produced as a cylindrical seating surface. The seating surfaces for the outer cup and the raceway for the rolling elements or inner ring (if the bearing arrangement is not produced as a direct bearing arrangement) should not be interrupted by grooves, holes or other re-cesses. The accuracy of the mating parts must meet specific requirements, the bore tolerances for the housing bore (recommended tolerance classes) are dependent on the housing material ➤ Table. If the housings are not rigid, tests must be carried out to determine which shaft tolerance the desired operating clearance will be achieved with. Numerical values for IT grades ➤ Table. For the bearings to be mounted without damage, the shaft must have a lead chamfer of 10° to 15°.
Tolerance classes and surface design for housings, as a function of the material
Housing material |
Bore tolerance |
Roundness tolerance |
Parallelism tolerance |
Recommended |
---|---|---|---|---|
Ramax (Rzmax) |
||||
max. |
max. |
μm |
||
Steel or cast iron |
N6 Ⓔ |
IT5/2 |
IT5/2 |
0,8 (4) |
Aluminium (Al) |
R6 Ⓔ |
IT5/2 | IT5/2 | 0,8 (4) |
Magnesium (Mg) |
S6 Ⓔ |
IT5/2 | IT5/2 | 0,8 (4) |
Numerical values for ISO standard tolerances (IT grades) to ISO 286-1:2010
IT grade |
Nominal dimension in mm |
|||||||
---|---|---|---|---|---|---|---|---|
over |
– |
3 |
6 |
10 |
18 |
30 |
50 |
|
incl. |
3 |
6 |
10 |
18 |
30 |
50 |
80 |
|
Values in μm |
||||||||
IT3 |
2 | 2,5 | 2,5 | 3 | 4 | 4 | 5 | |
IT4 |
3 | 4 | 4 | 5 | 6 | 7 | 8 | |
IT5 |
4 | 5 | 6 | 8 | 9 | 11 | 13 |
Axial location of bearings
A tight fit is usually sufficient for axial location
If axial locating elements such as shoulders and snap rings are not used, the housing bore can be produced easily and particularly economically. This also gives simplified mounting of the bearings.
Raceway for bearing arrangements without an inner ring (direct bearing arrangement)
Produce the raceway as a rolling bearing raceway
Where drawn cup needle roller bearings run directly on the shaft (without an inner ring), the raceway for the rolling elements must be produced as a rolling bearing raceway (hardened and ground). Design of raceways ➤ Table. The values in the table refer to commonly encountered application examples. If the shaft cannot be produced as a raceway, the bearings can be combined with Schaeffler bearing rings. However, the section height of the bearings will then be increased by the thickness of the rings.
Tolerance class and surface design for the shaft (direct bearing arrangement)
Shaft tolerance |
Roundness tolerance |
Parallelism tolerance |
Recommended mean roughness value |
---|---|---|---|
Ramax (Rzmax) |
|||
max. |
max. |
μm |
|
h6 Ⓔ |
IT3 |
IT3 |
0,2 (1) |
Steels for the raceway (direct bearing arrangement)
Through hardening steels
Through hardening steels in accordance with ISO 683-17 (e. g. 100Cr6) are suitable as materials for rolling bearing raceways in direct bearing arrangements. These steels can also be surface layer hardened.
Case hardening steels
Case hardening steels normally correspond to ISO 683-17 (such as 17MnCr5, 18CrNiMo7-6) or EN 10084 (such as 16MnCr5).
Steels for inductive surface layer hardening
For flame and induction hardening, steels in accordance with ISO 683-17 (such as C56E2, 43CrMo4) or DIN 17212 (such as Cf53) should be used.
Surface hardness and hardening depth
Nominal surface hardness: ≧ 670 HV
The requisite minimum surface hardness of 670 HV is valid for raceways, axial washers and shaft shoulders. Steels hardened by means of case, flame or induction hardening must have a surface hardness of 670 HV to 840 HV and an adequate hardening depth CHD or SHD.
Raceway softer than 670 HV
If the raceway fulfils the requirements for rolling bearing materials but is softer than 670 HV, the load on the bearing arrangement cannot be as high as the full load carrying capacity of the bearing. In order to determine the dynamic and static load carrying capacity of the bearing arrangement, the basic dynamic load rating C of the bearings must be multiplied by the reduction factor fH (dynamic hardness factor) and the basic static load rating C0r by the reduction factor fH0 (static hardness factor) ➤ Figure and ➤ Figure.
Dynamic hardness factor at reduced hardness of raceways/rolling elements fH = dynamic hardness factor HV, HRC = surface hardness |
![]() |
Static hardness factor at reduced hardness of raceways/rolling elements fH0 = static hardness factor HV, HRC = surface hardness |
![]() |
Determining the case hardening depth
Approximation value for case hardening depth
In order to obtain an approximation value for defining the minimum hardening depth, the relationship in accordance with ➤ Equation can be used as a basis. The reference value for the load present is the equivalent stress in accordance with the distortion energy hypothesis (DEH) as a function of the rolling element diameter Dw and the magnitude of the load.
Case hardening depth

Legend
CHD | mm |
Case hardening depth |
Dw | mm |
Rolling element diameter |
The local hardness must always be above the local requisite hardness, which can be calculated from the equivalent stress.
Determining the surface hardening depth
In these surface hardening methods, the load and contact geometry must be taken into consideration when determining the requisite hardening depth.
Determining the surface hardening depth
The rule of thumb for calculating the surface hardening depth SHD is the relationship in accordance with ➤ Equation.
Surface hardening depth

Legend
SHD | mm |
Surface hardening depth |
Dw | mm |
Rolling element diameter |
Rp0,2 | N/mm2 |
Yield point of base material |
Mounting and dismounting
Ensure that the bearings are not damaged during mounting
The bearings are self-retaining (not separable). They are mounted using a special fitting mandrel ➤ Figure. The shoulder of the fitting mandrel must rest against the marked end face (designation) of the bearing. A toroidal ring should be used to retain the bearing. The length and oversize of the ring must be matched by the customer to the dimensions and mass of the bearing. The forces occurring during pressing-in are dependent on several factors. Mounting must be carried out so that the bearing rib on the end face is not deformed. If the application requires a mounting procedure different from the one described, mounting trials must be carried out in order to ensure that the bearings can be mounted correctly and without causing damage.
Drawn cup needle roller bearings must not be tilted during pressing-in, as this may damage the bearing. If grease lubrication is to be used, the bearings should be lubricated with grease before mounting.
Mounting of a drawn cup needle roller bearing with open ends using a fitting mandrel: design of the fitting mandrel General tolerances to Fw = inner enveloping circle diameter D = bearing outside diameter R = radii of fitting mandrel
|
![]() |
Schaeffler Mounting Handbook
Rolling bearings must be handled with great care
Rolling bearings are well-proven precision machine elements for the design of economical and reliable bearing arrangements, which offer high operational security. In order that these products can function correctly and achieve the envisaged operating life without detrimental effect, they must be handled with care.
The Schaeffler Mounting Handbook MH 1 gives comprehensive information about the correct storage, mounting, dismounting and maintenance of rotary rolling bearings http://www.schaeffler.de/std/1B68. It also provides information which should be observed by the designer, in relation to the mounting, dismounting and maintenance of bearings, in the original design of the bearing position. This book is available from Schaeffler on request.
Legal notice regarding data freshness
The further development of products may also result in technical changes to catalogue products
Of central interest to Schaeffler is the further development and optimisation of its products and the satisfaction of its customers. In order that you, as the customer, can keep yourself optimally informed about the progress that is being made here and with regard to the current technical status of the products, we publish any product changes which differ from the printed version in our electronic product catalogue.
We therefore reserve the right to make changes to the data and illustrations in this catalogue. This catalogue reflects the status at the time of printing. More recent publications released by us (as printed or digital media) will automatically precede this catalogue if they involve the same subject. Therefore, please always use our electronic product catalogue to check whether more up-to-date information or modification notices exist for your desired product.
Further information
In addition to the data in this chapter, the following chapters in Technical principles must also be observed in the design of bearing arrangements: