Table of contents
Radial insert ball bearings
- Bearing design
- Load carrying capacity
- Compensation of angular misalignments
- Lubrication
- Sealing
- Speeds
- Noise
- Temperature range
- Cages
- Internal clearance
- Dimensions, tolerances
- Suffixes
- Structure of bearing designation
- Dimensioning
- Minimum load
- Design of bearing arrangements
- Mounting and dismounting
- Legal notice regarding data freshness
- Further information
Radial insert ball bearings
Radial insert ball bearings are ready-to-fit machine elements. In combination with drawn shafts, they are particularly easy to fit and suitable for the design of economical bearing arrangements. They are highly suitable where predominantly radial loads must be supported.
Radial insert ball bearings with an extended inner ring undergo less tilting and therefore run more smoothly.
Radial insert ball bearings with a spherical outer ring are highly suitable where:
- static angular misalignments of the shaft must be compensated, which are caused by mounting inaccuracies and tolerances in the adjacent construction ➤ section
- very good seals are required in environmental conditions such as dust, contamination, moisture, stone impacts and shocks ➤ section
Radial insert ball bearings with a cylindrical outer ring are highly suitable where:
- a cylindrical housing bore is already present
- the outer ring of the bearings is to be located by means of easy-to-fit snap rings
Radial insert ball bearings with a profiled bore are highly suitable where:
- shafts must transmit very high torques
Radial insert ball bearings with a rubber interliner are highly suitable where:
- vibrations and shocks must be supported
- damping of running noise is required
Compensation of static angular misalignments, available seals with sealing action of different magnitudes η = sealing action |
![]() |
Bearing design
Design variants
The radial insert ball bearings have a spherical or cylindrical outside surface. They are predominantly located on the shaft by means of an eccentric locking collar or grub screws.
The bearings are sealed using a range of available standard seals that are matched to the different application conditions.
Radial insert ball bearings are available in the following designs:
- standard bearings in accordance with ISO ➤ link
- corrosion-resistant bearings in a VA design or with a Corrotect coating in accordance with ISO ➤ link
- Black Series with Durotect BS coating in accordance with JIS B 1558 ➤ link
Radial insert ball bearings are also available in many other designs and sizes, as well as for specific applications, by agreement.
Numerous sizes are supplied in X-life premium quality. These products are indicated in the product tables.
Radial insert ball bearings of X-life premium quality have, for example, a lower roughness Ra and higher geometrical accuracy of the raceways than comparable designs that are not X-life. As a result, these bearings have higher load carrying capacity and longer rating life although their dimensions are identical. In certain applications, this means that it may be possible to design a smaller bearing arrangement.
Radial insert ball bearings of X-life premium quality have an eccentric locking collar of an improved design and the quantity and distribution of the lubricant has been optimised. Housings ASE have additional crosspieces on the underside. For extreme requirements, the cage and seal material in the high and low temperature designs (suffix FA101) has been significantly improved in comparison with earlier versions.
Metric and inch size designs
Radial insert ball bearings are available in metric sizes. Some series have a bore diameter with inch dimensions.
Standard bearings in accordance with ISO
The radial insert ball bearings are based on the deep groove ball bearing series 60, 62 and 63. The numerals identify the ball set and therefore the load carrying capacity of the bearing ➤ section. The inner ring is extended on one or both sides, while the bore has a plus tolerance in most of the designs.
Radial insert ball bearings are particularly easy to fit and are preferentially suitable for drawn shafts of tolerance classes h6 Ⓔ to h9 Ⓔ. For non-locating bearings, shafts of tolerance classes h5 Ⓔ to h7 Ⓔ are recommended.
Spherical outside surface for the compensation of misalignments
Radial insert ball bearings with a spherical outside surface are single row, ready-to-fit units comprising a solid outer ring, cages made from plastic or sheet steel and seals P, R, L or T ➤ Table. Bearings with an inner ring extended on both sides undergo less tilting of the inner ring and therefore run more smoothly.
In combination with a housing matched to the design, bearings with a spherical outside surface can compensate for misalignment of the shaft ➤ section.
With only a few exceptions, radial insert ball bearings can be relubricated. For this purpose, they have two lubrication holes in one plane of the outer ring offset by 180°.
Location on the shaft is by means of an eccentric locking collar, grub screws in the inner ring, an adapter sleeve, a drive slot, fit or profiled bore ➤ Figure.
Cylindrical outside surface for a cylindrical housing bore
Radial insert ball bearings with a cylindrical outside surface are single row, ready-to-fit units comprising a solid outer ring, an inner ring extended on one or both sides, cages made from plastic and seals P or R ➤ Table. Bearings with an inner ring extended on both sides undergo less tilting of the inner ring and therefore run more smoothly.
The radial insert ball bearings are greased and cannot be relubricated.
Their location on the shaft is by means of an eccentric locking collar, fit or profiled bore ➤ link and ➤ link.
Location and design
Locating bearings
Location is by means of eccentric locking collars, grub screws or integrated adapter sleeves ➤ Figure and ➤ Figure. Certain series can be located by means of a fit on the shaft. The extended inner ring on one or both sides is used as a running surface for the seal and prevents significant tilting of the inner ring.
Bearings with vibration damping
For applications where strong vibrations can occur, damping can be achieved using radial insert ball bearings with a thick-walled rubber interliner ➤ Figure.
Non-locating bearings
Radial insert ball bearings with a drive slot in the inner ring are non-locating bearings that are used for low speeds and loads in order to compensate for elongations of the shaft ➤ Figure. The slot allows simple radial location of the bearing on the shaft.
Location methods for radial insert ball bearings
|
![]() |
Design examples of radial insert ball bearings
|
![]() |
Radial insert ball bearings with eccentric locking collar
These "classic" INA radial insert ball bearings are located on the shaft by means of a locking collar ➤ Figure. They are particularly suitable for bearing arrangements with a constant direction of rotation or, under low speed and load, for an alternating direction of rotation.
The locking collar is preferably tightened in the direction of rotation and secured by means of a grub screw. This location method prevents damage to the shaft and can be easily loosened again.
With the exception of a few series, sealed bearings can be relubricated.
Corrosion protection
The inner rings up to d = 60 mm and the locking collars in general have a Corrotect coating and are thus protected against fretting corrosion. This is not valid for the series RALE..-XL-NPP(-B).
Location by means of eccentric locking collar GE..-XL-KRR-B |
![]() |
Radial insert ball bearings with eccentric locking collar and slots in the outer ring
The basic design of series RAE..-XL-NPP-NR is a radial insert ball bearing with an eccentric locking collar and an inner ring extended on one side ➤ Figure.
The outer ring has a cylindrical outside surface and two slots to DIN 616 and ISO 464. The bearings are fitted in cylindrical bores and axially located by easy-to-fit snap rings. The bearing is supplied with one snap ring to DIN 5417 already fitted.
The radial insert ball bearings are greased and cannot be relubricated.
Corrosion protection
Inner rings up to a bore diameter d = 60 mm have a Corrotect coating and are thus protected against fretting corrosion.
Radial insert ball bearing with cylindrical outside surface and two slots in outer ring RAE..-XL-NPP-NR |
![]() |
Radial insert ball bearings with grub screws in the inner ring
In the case of these radial insert ball bearings, the inner ring is located on the shaft by means of two grub screws offset by 120° ➤ Figure. This location method is suitable for bearing arrangements with a constant direction of rotation or, under low speed and load, for an alternating direction of rotation.
The grub screws are self-retaining and have a fine pitch thread with cup point for secure location of the bearings.
With the exception of series AY..-XL-NPP-B, the bearings can be relubricated.
Location by means of grub screws in the inner ring GYE..-XL-KRR-B |
![]() |
Radial insert ball bearings with adapter sleeve
In the case of this series, the inner ring is located on the shaft by means of an adapter sleeve with a locknut and a tab washer ➤ Figure. These radial insert ball bearings are suitable for shafts up to tolerance class h11 Ⓔ.
The bearings can be relubricated.
Suitable for very high speeds
This location method is suitable for bearing arrangements with a constant or alternating direction of rotation and for high speeds.
The adapter sleeve and locknut give concentric, force locking location of the bearing inner ring on the shaft. As a result, the speeds that can be achieved are approximately the same as with deep groove ball bearings. These bearings also give quieter running than normal radial insert ball bearings. The adapter sleeve, locknut and tab washer are all zinc-coated.
Reversing operation
The bearings are highly suitable for reversing operation. As a result of the force locking connection, there is no occurrence of fretting corrosion between the shaft and the bore of the adapter sleeve.
Interchangeability
Due to the integral adapter sleeve, the bearings have the same radial dimensions as, and slightly lower basic load ratings than, radial insert ball bearings with an eccentric locking collar, or with grub screws in the inner ring, and are interchangeable with these bearings.
Location using adapter sleeve and locknut GSH..-XL-2RSR-B |
![]() |
Radial insert ball bearings with drive slot
Suitable as non-locating bearings for low speeds
Radial insert ball bearings with a drive slot in the inner ring are non-locating bearings with good high temperature characteristics ➤ Figure. Non-locating bearings are used at low speeds and loads to compensate for elongations of the shaft.
Due to the slot, they are easy to locate in a radial direction. Rotation is
prevented by means of a drive pin on the shaft or a set collar with a pin. The non-locating bearings are suitable for drawn shafts of tolerance classes h5 Ⓔ to h7 Ⓔ.
The bearings can be relubricated.
Corrosion protection
Inner rings up to a bore diameter d = 60 mm have a Corrotect coating and are thus protected against fretting corrosion.
Location by means of drive slot GLE..-XL-KRR-B |
![]() |
Self-aligning deep groove ball bearings with bore for fit
Self-aligning deep groove ball bearings are available with a cylindrical bore for a fit seat ➤ Figure and with a reamed square or hexagonal bore ➤ Figure.
The outer ring has a spherical outside surface.
Bearings with a fit seat on the shaft can achieve the same speeds as standard ball bearings. These are suitable for bearing arrangements with an alternating direction of rotation and offer smooth running.
Self-aligning deep groove ball bearing with fit seat 2..-XL-NPP-B |
![]() |
For self-aligning deep groove ball bearings with a fit seat, the fit data for ball bearings apply.
Deep groove ball bearings with bore for fit
These bearings have a cylindrical outer ring and are fitted in cylindrical bores ➤ Figure. The inner ring is extended on both sides and is located on the shaft using a fit. Due to the extended inner ring, additional axial spacer rings are not required.
The concentric seat allows speeds equivalent to those of standard ball bearings, while the load can be either constant or alternating. Smooth running is also achieved.
The tolerance of the inner ring bore corresponds to tolerance class Normal in accordance with ISO 492.
The sheet steel washers extended outwards and angled downwards form a large grease reservoir.
Deep groove ball bearing with extended inner ring and bore for fit 2..-XL-KRR 2..-XL-KRR-AH |
![]() |
Self-aligning deep groove ball bearings with profiled bore
Transmission of high torques
Bearings with a profiled bore are used where shafts must transmit very high torques and this is only possible using square or hexagonal shafts ➤ Figure. Rotation is prevented by form fit.
These bearings have a spherical or cylindrical outer ring and an inner ring that is extended on both sides ➤ Figure and ➤ Figure. Shafts of tolerance class h11 Ⓔ are recommended.
The bearings are greased to their maximum, some designs with a spherical outside surface can also be relubricated.
Corrosion protection
The bearings have a Corrotect coating.
Self-aligning deep groove ball bearings with profiled bore
VK..-KTT-B SK..-KRR-B |
![]() |
Deep groove ball bearings with extended inner ring and profiled bore
SK..-KRR SK..-KTT |
![]() |
Radial insert ball bearings with rubber interliner
Radial insert ball bearings with a rubber interliner are located on the shaft using an eccentric locking collar. The outer ring is encased in a thick-walled NBR interliner ➤ Figure.
Radial insert ball bearings with rubber interliner
Structure of bearing designation ➤ Table |
![]() |
Damping of running noise
The interliner absorbs vibrations and shocks and thus gives damping of running noises.
Various types
The interliners have a spherical or cylindrical outside surface.
For roll bearing arrangements, one series has a locating shoulder on the rubber interliner.
Bearings with rubber interliners cannot be relubricated.
Note the tube and housing diameters for radial insert ball bearings with rubber interliner:
- CRB: tube inside diameter D –0,6 to –1,6
- RABR, RCR, RCSM: housing diameter D –0,25 to –0,35
Corrosion protection
The inner ring and locking collar have a Corrotect coating and are thus protected against fretting corrosion. This is not valid for series with the radial insert ball bearing RALE..-XL-NPP(-B).
Radial insert ball bearings with steel aligning ring
These bearings are based on radial insert ball bearings with an eccentric locking collar or on self-aligning deep groove ball bearings, but additionally have an axially split outer ring as an aligning ring ➤ Figure. They are mounted in cylindrical bores and can compensate static misalignments of the shaft up to ±5°.
In series PE, the inner ring is located on the shaft by means of a locking collar while, in series BE, it is located by a fit.
Radial insert ball bearings with an aligning ring cannot be relubricated.
Suitable for sheet metal constructions
Due to the annular slots in the outer ring to DIN 616, they are highly suitable for sheet metal constructions. In this case, they are axially located using snap rings to DIN 5417.
The fit tolerances of the aligning rings are those of the deep groove ball bearings. Select the fit for the shaft and housing such that the outer ring of the radial insert ball bearing can undergo self-alignment.
Corrosion protection
The aligning ring has a Corrotect coating and is thus protected against fretting corrosion. In the case of series PE..-XL, the inner ring and locking collar also have a coating.
Radial insert ball bearing with steel aligning ring PE..-XL |
![]() |
Corrosion-resistant bearings in a VA design or with a Corrotect coating in accordance with ISO
The radial insert ball bearings SUB, SUC and SUG, as well as the radial insert ball bearings with the suffix FA125, are designed for corrosion-resistant bearing arrangements. They are therefore equally suitable for applications involving humidity, contaminated water, salt spray mist and for cleaning agents. Their classic areas of application include the agricultural, construction and mining sector, conveying equipment, textile, paper and woodworking machinery, as well as machinery for the food and drink industry.
Corrosion-resistant VA design or with Corrotect coating
The bearings are available in a corrosion-resistant VA design or with a Corrotect thin film coating ➤ Figure. They correspond in their design to single row deep groove ball bearings 62, are ready to fit, particularly easy to fit and allow robust, economical bearing arrangements with a long operating life. They are located on the shaft by means of grub screws in the extended inner ring or by means of an eccentric locking collar.
Operation even under difficult conditions is ensured by seals and greases that are matched to the application.
Corrosion-resistant radial insert ball bearings, with Corrotect coating or in VA design
|
![]() |
Radial insert ball bearings in corrosion-resistant VA design
In the case of radial insert ball bearings SUB, SUC and SUG, the bearing rings, eccentric locking collar and rolling elements are made from high alloy, corrosion-resistant rolling bearing steel with an increased chromium and molybdenum content, material number 1.4125.
Sheet steel cages made from corrosion-resistant steel, material number 1.4301, retain and guide the rolling elements.
Location by means of corrosion-resistant VA grub screws
The inner ring is located axially on the shaft by means of two corrosion-resistant VA grub screws, material number 1.4301, offset by 120°. This location method is suitable for bearing arrangements with a constant direction of rotation or, under low speed and load, for an alternating direction of rotation.
The grub screws are self-retaining and have a fine pitch thread with cup point for secure location of the bearings when taking account of the stated tightening torques ➤ Table.
Location using corrosion‑resistant VA eccentric locking collar
The bearings are located on the shaft by means of a corrosion-resistant VA locking collar. They are thus particularly suitable for bearing arrangements with a constant direction of rotation or, under low speed and load, for an alternating direction of rotation.
The locking collar is preferably tightened in the direction of rotation and must be secured by means of a grub screw. This location method prevents damage to the shaft and can be easily loosened again.
Media resistance
In the food industry in particular, the resistance of the material in relation to various cleaning agents is of increasing importance ➤ Table.
Resistance to media
Medium + resistant (+) moderately resistant (–) barely resistant – not resistant |
Concentration |
X5CrNi18-10 |
440C |
||
---|---|---|---|---|---|
% |
+20 °C |
+80 °C |
+20 °C |
+80 °C |
|
Hydrochloric acid HCl | |||||
0,1 |
+ |
+ |
‒ |
‒ |
|
1 |
(+) |
‒ |
‒ |
‒ |
|
18 |
‒ |
‒ |
‒ |
‒ |
|
Hydrofluoric acid HF | |||||
1 |
‒ |
‒ |
‒ |
‒ |
|
5 |
–1) |
‒ |
–1) |
‒ |
|
Sulphuric acid H2SO4 | |||||
1 |
+ |
‒ |
‒ |
‒ |
|
10 |
(+) |
‒ |
‒ |
‒ |
|
96 |
+ |
(+) |
‒ |
‒ |
|
Sulphurous acid H2SO3 |
|||||
1 |
+ |
+ |
‒ |
‒ |
|
Nitric acid HNO3 | |||||
5 |
+ |
+ |
‒ |
‒ |
|
25 |
+ |
+ |
+ |
(+) |
|
65 |
+ |
+ |
+ |
(+) |
|
Phosphoric acid H3PO4 | |||||
1 |
+ |
+ |
+ |
+ |
|
10 |
+ |
+ |
(+) |
+ |
|
85 |
+ |
+ |
+ |
‒ |
|
Formic acid HCOOH | |||||
5 |
+ |
+ |
‒ |
‒ |
|
25 |
+ |
+ |
‒ |
‒ |
|
Acetic acid CH3COOH | |||||
5 |
+ |
+ |
+ |
‒ |
|
25 |
+ |
+ |
+ |
‒ |
|
Citric acid | |||||
5 |
+ |
+ |
+ |
+ |
|
25 |
+ |
+ |
‒ |
‒ |
|
Chloroacetic acid | |||||
5 |
+ |
+ |
(+) |
‒ |
|
Sodium chloride NaCl |
|||||
10 |
+ |
+ |
(–) |
(–) |
|
Sea water |
|||||
4 |
+ |
+ |
(–) |
(–) |
|
Distilled water |
|||||
‒ |
+ |
+ |
+ |
+ |
|
Ammonium hydroxide NH4OH | |||||
1 |
+ |
+ |
+ |
+ |
|
10 |
+ |
+ |
+ |
+ |
|
Potassium hydroxide solution KOH | |||||
0,1 |
+ |
+ |
+ |
+ |
|
1 |
+ |
+ |
+ |
+ |
|
10 |
+ |
+ |
+ |
+ |
|
Sodium hypochlorite solution |
|||||
1 |
+1) |
+ |
2) |
(–) |
|
Hydrogen peroxide H2O2 |
|||||
5 |
+ |
+ |
+ |
+ |
- Not tested. Estimate generated from remaining test series.
- Not tested. No estimate possible.
Radial insert ball bearings with Corrotect coating
The radial insert ball bearings GRAE..-XL-NPP-B-FA125 and GE..‑XL‑KRR‑B‑FA125 have a Corrotect thin film coating on all surfaces.
Plastic cages made from polyamide PA66 retain and guide the rolling elements.
Anti-corrosion coating system Corrotect
The Corrotect thin film coating technology is an economical alternative to radial insert ball bearings with conventional corrosion protection. The thickness of the coating film is between 2 μm and 5 μm.
The advantages of the Corrotect thin film coating are:
- All surfaces are protected against corrosion, including the turned surfaces of chamfers and radii
- Rust beneath seals is prevented in the long term
- Smaller spots that are damaged by the application and are bright as a result remain protected against corrosion by the cathodic protection effect
- Operating life is significantly longer compared to uncoated parts due to the corrosion protection
- Uncoated bearings and housings are fully interchangeable with the coated versions of the same design
- Bearings and housings made from corrosion-resistant rolling bearing steel are often no longer required
The use of the Corrotect thin film coating is not permitted for direct contact with foodstuffs.
Media resistance
The resistance of the Corrotect thin film coating to various media must be taken into consideration ➤ Table.
Resistance to media
Chemicals |
Corrotect coating1) |
---|---|
Neutral, organic fluids (oil, brake fluid, petrol) |
Resistant |
Aqueous salt solutions in the neutral range 6 ≦ pH ≧ 8 (table salt NaCl, seawater applications) |
Conditionally resistant |
Acidic liquids (pH ≦ 6) |
Not resistant |
Alkaline liquids (pH ≧ 8) |
Not resistant |
Oxidising substances (ozone, chlorine, peroxides, hypochlorides) |
Not resistant |
- Valid for Corrotect coatings based on zinc and zinc alloy.
Location by means of locking collar
The bearings are located on the shaft by a locking collar. They are thus particularly suitable for bearing arrangements with a constant direction of rotation or, under low speed and load, for an alternating direction of rotation.
The locking collar is preferably tightened in the direction of rotation and must be secured by means of a grub screw. This location method prevents damage to the shaft and can be easily loosened again.
Black Series in accordance with JIS B 1558
FAG radial insert ball bearings with a spherical outer ring are based on single row deep groove ball bearings 62 and are designed in accordance with JIS B 1558. The Black Series radial insert ball bearings are available with two location methods and one type of seal. They can be relubricated and are particularly easy to install.
The radial insert ball bearings are pregreased and can be relubricated by means of two lubrication holes in the outer ring.
Cages made from plastic
The bearings have plastic cages ➤ link and are sealed on both sides by single piece seals RSR with a vulcanised seal lip and an outer flinger shield.
Quiet running, low frictional torque
The honed raceways of the bearing rings, in conjunction with the high ball grade, ensure quiet running and a reduced frictional torque.
Basic corrosion protection Durotect BS
The inner and outer rings as well as the flinger shields are provided with the black Durotect BS coating in order to offer basic protection against corrosion.
Adapter sleeves have a Durotect BS or phosphate coating.
Location on shaft
Location by means of grub screws
In the radial insert ball bearings UC, the inner ring is located on the shaft by means of two grub screws offset by 120° ➤ Figure. They are suitable for bearing arrangements with a constant direction of rotation or, under low speed and load, for an alternating direction of rotation.
The grub screws are self-retaining and have a fine pitch thread with cup point for secure location of the bearings. In order to allow better differentiation, the metric grub screws have a Durotect BS coating while the inch size grub screws are zinc plated.
Location by means of grub screws in the inner ring UC |
![]() |
Location by means of adapter sleeve
In the radial insert ball bearings UK, the inner ring is located on the shaft by means of a concentric adapter sleeve in accordance with JIS B 1552 ➤ Figure. The inner and outer roughness of the adapter sleeve is Ra 2,5. They are suitable for bearing arrangements with an alternating direction of rotation, even under high speed and load.
Location by adapter sleeve UK |
![]() |
Comparison of radial insert ball bearing series
The possible dimensions and features of the standard bearings are presented in the following table ➤ Table. The corrosion-resistant radial insert ball bearing range and the radial insert ball bearings in accordance with JIS (Black Series) are summarised separately ➤ Table.
Features of radial insert ball bearings, comparison of standard bearing series
Series |
Shaft diameter |
Location |
Series |
Accessories |
Sealing |
Compensation of misalignment |
Internal clearance |
Cage |
Series |
Grease |
Relubrication facility |
Temperature1) |
Comments |
||||
---|---|---|---|---|---|---|---|---|---|---|---|---|---|---|---|---|---|
mm |
inch |
°C |
|||||||||||||||
from |
to |
from |
to |
Group |
from |
to |
|||||||||||
GE..-XL-KLL-B |
20 |
50 |
‒ |
‒ |
Eccentric locking collar |
GE..-XL-KLL-B |
‒ |
L |
yes |
5 |
Stahl |
GE..-XL-KLL-B |
L069 |
yes |
–40 |
+180 |
‒ |
E..-XL-KLL |
20 |
50 |
‒ |
‒ |
Eccentric locking collar |
E..-XL-KLL |
‒ |
L |
no |
3 |
PA66 |
E..-XL-KLL |
GA13 |
no |
–20 |
+1002) |
‒ |
GRAE..-XL-NPP-B |
12 |
60 |
‒ |
‒ |
Eccentric locking collar |
GRAE..-XL-NPP-B |
‒ |
P |
yes |
3 |
PA66 |
GRAE..-XL-NPP-B |
GA13 |
yes |
–20 |
+1002) |
‒ |
GRA..-NPP-B-AS2/V |
‒ |
‒ |
5/8 | 1 15/16 | Eccentric locking collar |
GRA..-NPP-B-AS2/V |
- |
P |
yes |
3 |
PA66 |
GRA..-NPP-B-AS2/V |
GA13 |
yes |
–20 |
+1002) |
‒ |
RABRB..-XL-FA106 |
12 |
50 |
‒ |
‒ |
Eccentric locking collar |
RABRB..-XL-FA106 |
Rubber interliner |
P |
yes |
3 |
PA66 |
RABRB..-XL-FA106 |
GA13 |
no |
–20 |
+85 |
‒ |
RABRA..-XL-FA106 |
30 |
‒ |
‒ |
‒ |
Eccentric locking collar |
RABRA..-XL-FA106 |
Rubber interliner | P | yes | 3 | PA66 |
RABRA..-XL-FA106 |
GA13 | no | –20 | +85 |
Light series |
RAE..-XL-NPP-B |
12 |
50 |
‒ |
‒ |
Eccentric locking collar |
RAE..-XL-NPP-B |
‒ |
P |
yes |
3 |
PA66 |
RAE..-XL-NPP-B |
GA13 |
no |
–20 |
+1002) |
‒ |
RA..-NPP-B |
‒ |
‒ |
3/4 | 1 1/2 | Eccentric locking collar |
RA..-NPP-B |
- |
P | yes | 3 | PA66 |
RA..-NPP-B |
GA13 | no | –20 | +1002) |
‒ |
RALE..-XL-NPP-B |
20 |
30 |
‒ |
‒ |
Eccentric locking collar |
RALE..-XL-NPP-B |
- |
P | yes | 3 | PA66 | RALE..-XL-NPP-B | GA13 | no | –20 | +1002) | Light series |
PE..-XL |
20 |
40 |
‒ |
‒ |
Eccentric locking collar |
PE..-XL |
Aligning ring |
P | yes | 3 | PA66 |
PE..-XL |
GA13 | no | –20 | +1002) |
Annular slots in aligning ring |
RCSMB..-XL-FA106 |
15 |
25 |
‒ |
‒ |
Eccentric locking collar |
RCSMB..-XL-FA106 |
Rubber interliner |
P |
no |
3 |
PA66 |
RCSMB..-XL-FA106 |
GA13 |
no |
–20 |
+85 |
‒ |
RCSMA..-XL-FA106 |
30 |
‒ |
‒ |
‒ |
Eccentric locking collar |
RCSMA..-XL-FA106 |
Rubber interliner | P | no | 3 | PA66 |
RCSMA..-XL-FA106 |
GA13 | no | –20 | +85 |
Light series |
RCRA..-XL-FA106 |
20 |
‒ |
‒ |
‒ |
Eccentric locking collar |
RCRA..-XL-FA106 |
Rubber interliner | P | no | 3 | PA66 |
RCRA..-XL-FA106 |
GA13 | no | –20 | +85 | Light series, mounting chamfer |
RCRB..-XL-FA106 |
20 |
‒ |
‒ |
‒ |
Eccentric locking collar |
RCRB..-XL-FA106 |
Rubber interliner | P | no | 3 | PA66 |
RCRB..-XL-FA106 |
GA13 | no | –20 | +85 |
Mounting chamfer |
CRB..-XL |
20 |
35 |
‒ |
‒ |
Eccentric locking collar |
CRB..-XL |
Rubber interliner | P | no | 3 | PA66 |
CRB..-XL |
GA13 | no | –20 | +85 |
Abutment shoulder |
Series |
Shaft diameter |
Location |
Series |
Accessories |
Sealing |
Compensation of misalignment |
Internal clearance |
Cage |
Series |
Grease |
Relubrication facility |
Temperature |
Comments |
||||
mm |
inch |
°C |
|||||||||||||||
from |
to |
from |
to |
Group |
from |
to |
|||||||||||
RAE..-XL-NPP |
12 |
60 |
‒ |
‒ |
Eccentric locking collar |
RAE..-XL-NPP |
‒ |
P |
no |
3 |
PA66 |
RAE..-XL-NPP |
GA13 |
no |
–20 |
+1002) |
‒ |
RALE..-XL-NPP |
20 |
30 |
‒ |
‒ |
Eccentric locking collar |
RALE..-XL-NPP |
- |
P | no | 3 | PA66 |
RALE..-XL-NPP |
GA13 | no | –20 | +1002) |
‒ |
RAE..-XL-NPP-NR |
20 |
40 |
‒ |
‒ |
Eccentric locking collar |
RAE..-XL-NPP-NR |
- |
P | no | 3 | PA66 | RAE..-XL-NPP-NR | GA13 | no | –20 | +1002) |
Two slots, one snap ring |
RA..-NPP |
‒ |
‒ |
5/8 | 1 1/2 | Eccentric locking collar |
RA..-NPP |
- |
P | no | 3 | PA66 |
RA..-NPP |
GA13 | no | –20 | +1002) |
‒ |
RAL..-NPP |
‒ |
‒ |
3/4 |
‒ |
Eccentric locking collar |
RAL..-NPP |
- |
P | no | 3 | PA66 |
RAL..-NPP |
GA13 | no | –20 | +1002) |
‒ |
GE..-XL-KRR-B |
17 |
120 |
‒ |
‒ |
Eccentric locking collar |
GE..-XL-KRR-B |
‒ |
R |
yes |
3 |
PA66 |
GE..-XL-KRR-B |
GA13 |
yes |
–20 |
+1002) |
‒ |
G..-KRR-B-AS2/V |
‒ |
‒ |
15/16 | 2 15/16 |
Eccentric locking collar |
G..-KRR-B-AS2/V |
‒ |
R |
yes |
3 |
PA66 |
G..-KRR-B-AS2/V |
GA13 |
yes |
–20 |
+1002) |
‒ |
GE..-XL-KRR-B-2C |
25 |
40 |
‒ |
‒ |
Eccentric locking collar |
GE..-XL-KRR-B-2C |
- |
R | yes | 3 | PA66 |
GE..-XL-KRR-B-2C |
GA13 | yes | –20 | +1002) |
Flinger shields |
GNE..-XL-KRR-B |
30 |
100 |
‒ |
‒ |
Eccentric locking collar |
GNE..-XL-KRR-B |
- |
R | yes | 3 | PA66 |
GNE..-XL-KRR-B |
GA13 | yes | –20 | +1002) |
Heavy series |
E..-XL-KRR-B |
25 |
40 |
‒ |
‒ |
Eccentric locking collar |
E..-XL-KRR-B |
‒ |
R |
yes |
3 |
PA66 |
E..-XL-KRR-B |
GA13 |
no |
–20 |
+1002) |
‒ |
NE..-XL-KRR-B |
50 |
‒ |
‒ |
‒ |
Eccentric locking collar |
NE..-XL-KRR-B |
- |
R | yes | 3 | PA66 | NE..-XL-KRR-B | GA13 | no | –20 | +1002) |
heavy series |
GE..-XL-KRR-B-FA101 |
20 |
75 |
‒ |
‒ |
Eccentric locking collar |
GE..-XL-KRR-B-FA101 |
‒ |
R |
yes |
5 |
Stahl |
GE..-XL-KRR-B-FA101 |
L069 |
yes |
–40 |
+180 |
PTFE seal lip |
GE..-XL-KRR-B-FA164 |
20 |
90 |
‒ |
‒ |
Eccentric locking collar |
GE..-XL-KRR-B-FA164 |
- |
R | yes | 5 | Stahl |
GE..-XL-KRR-B-FA164 |
GA11 |
yes |
+150 |
+250 |
PTFE seal lip |
E..-XL-KRR |
20 |
70 |
‒ |
‒ |
Eccentric locking collar |
E..-XL-KRR |
‒ |
R |
no |
3 |
PA66 |
E..-XL-KRR |
GA13 |
no |
–20 |
+1002) |
‒ |
GE..-XL-KTT-B |
20 |
80 |
‒ |
‒ |
Eccentric locking collar |
GE..-XL-KTT-B |
‒ |
T |
yes |
3 |
PA66 |
GE..-XL-KTT-B |
GA13 |
yes |
–20 |
+1002) |
‒ |
Series |
Shaft diameter |
Location |
Series |
Accessories |
Sealing |
Compensation of misalignment |
Internal clearance |
Cage |
Series |
Grease |
Relubrication facility |
Temperature |
Comments |
||||
mm |
inch |
°C |
|||||||||||||||
from |
to |
from |
to |
Group |
from |
to |
|||||||||||
GAY..-XL-NPP-B | 12 | 60 | - | - | Grub screws | GAY..-XL-NPP-B | - | P | yes | 3 | PA66 | GAY..-XL-NPP-B | GA13 | yes | –20 | +1002) | - |
GAY..-NPP-B-AS2/V | - | - | 5/8 | 1 7/16 | Grub screws | GAY..-NPP-B-AS2/V | - | P | yes | 3 | PA66 | GAY..-NPP-B-AS2/V | GA13 | yes | –20 | +1002) | - |
GYE..-XL-KRR-B | 12 | 90 | - | - | Grub screws | GYE..-XL-KRR-B | - | P | yes | 3 | PA66 | GYE..-XL-KRR-B | GA13 | yes | –20 | +1002) | - |
GY..-KRR-B-AS2/V | - | - | 1/2 | 2 15/16 | Grub screws | GY..-KRR-B-AS2/V | - | P | yes | 3 | PA66 | GY..-KRR-B-AS2/V | GA13 | yes | –20 | +1002) | - |
AY..-XL-NPP-B |
12 |
30 |
‒ |
‒ |
Grub screws |
AY..-XL-NPP-B |
‒ |
P |
yes |
3 |
PA66 |
AY..-XL-NPP-B |
GA13 |
no |
–20 |
+1002) |
‒ |
GAY..-XL-NPP-B-FA164 |
12 |
15 |
‒ |
‒ |
Grub screws |
GAY..-XL-NPP-B-FA164 |
‒ |
P |
yes |
5 |
Stahl |
GAY..-XL-NPP-B-FA164 |
GA11 |
yes |
+150 |
+250 |
PTFE seal lip |
GLE..-XL-KRR-B |
20 |
70 |
‒ |
‒ |
Drive slot |
GLE..-XL-KRR-B |
‒ |
R |
yes |
5 |
Stahl |
GLE..-XL-KRR-B |
L069 |
yes |
–40 |
+180 |
PTFE seal lip |
BE..-XL |
20 |
40 |
‒ |
‒ |
Fit |
BE..-XL |
Aligning ring |
P |
yes |
N |
PA66 |
BE..-XL |
GA13 |
no |
–20 |
+1002) |
Annular slots in aligning ring |
2..-XL-NPP-B |
12 |
50 |
‒ |
‒ |
Fit |
2..-XL-NPP-B |
‒ |
R |
yes |
N |
PA66 |
2..-XL-NPP-B |
GA13 |
no |
–20 |
+1002) |
‒ |
2..-XL-KRR(-AH) |
13 |
60 |
‒ |
‒ |
Fit |
2..-XL-KRR(-AH) |
- |
R |
no |
N |
PA66 |
2..-XL-KRR(-AH) |
GA13 |
no |
–20 |
+1002) |
‒ |
SK(E)..-KRR-B |
16,1 |
38,1 |
‒ |
‒ |
Hexagonal bore |
SK(E)..-KRR-B |
‒ |
R |
yes |
3 |
PA66 |
SK(E)..-KRR-B |
GA13 |
no |
–20 |
+1002) |
Corrosion-resistant, maximum greasing |
SK..-KRR |
‒ |
‒ |
7/8 | 1 1/4 | Hexagonal bore |
SK..-KRR |
- |
R |
no |
3 |
PA66 |
SK..-KRR |
GA13 |
no |
–20 |
+1002 |
Corrosion-resistant, maximum greasing |
SK..-KTT-B |
‒ |
‒ |
7/8 | 1 1/4 |
Hexagonal bore |
SK..-KTT-B |
‒ |
T |
yes |
3 |
PA66 |
SK..-KTT-B |
L402 |
no |
–20 |
+1002) |
Corrosion-resistant, maximum greasing |
SK..-KTT |
‒ |
‒ |
1 1/4 | 1 3/4 | Hexagonal bore |
SK..-KTT |
- |
T |
no |
GA13 |
|||||||
GSH..-XL-2RSR-B 3) |
20 |
50 |
‒ |
‒ |
Adapter sleeve |
GSH..-XL-2RSR-B |
‒ |
RSR |
yes |
4 |
PA66 |
GSH..-XL-2RSR-B |
GA13 |
yes |
–20 |
+1002) |
‒ |
GVK(E)..-KRR-B-AS2/V |
16,3 |
‒ |
‒ |
‒ |
Square bore |
GVK(E)..-KRR-B-AS2/V |
- |
R |
yes |
3 |
PA66 |
GVK(E)..-KRR-B-AS2/V |
GA13 |
yes |
–20 |
+1002) |
Corrosion-resistant, maximum greasing |
VK(E)..-KTT-B |
25,4 |
38 |
1 |
‒ |
Square bore |
VK(E)..-KTT-B |
- |
T |
yes | 3 | PA66 | VK(E)..-KTT-B |
GA13 |
no |
–20 |
+1002) |
Corrosion-resistant, maximum greasing |
GVK(E)..-KTT-B(-AS2/V) |
25,4 |
39,7 |
1 | 1 9/16 | Square bore |
GVK(E)..-KTT-B(-AS2/V) |
- |
T |
yes | 3 | PA66 | GVK(E)..-KTT-B(-AS2/V) |
GA13 |
yes |
–20 |
+1002) |
Corrosion-resistant, maximum greasing |
- Recommended application temperature. If temperatures exceed +100 °C, relubrication must be carried out regularly.
- Temporary temperature peaks are possible up to 120 °C.
- Pay attention to the interchangeability of the bearing ➤ link.
Features of radial insert ball bearings, comparison of series, corrosion‑resistant and Black Series
Series |
Shaft diameter |
Location |
Sealing |
Compensation of misalignment |
Internal clearance |
Cage |
Grease |
Relubrication facility |
Temperature1) |
Comments |
|||||
---|---|---|---|---|---|---|---|---|---|---|---|---|---|---|---|
mm |
inch |
°C |
|||||||||||||
from |
to |
from |
to |
from |
to |
||||||||||
Corrosion-resistant product range |
|||||||||||||||
GRAE..-XL-NPP-B-FA125 |
20 |
60 |
‒ |
‒ |
Eccentric locking collar |
P |
yes |
Group 3 |
PA66 |
GA47 |
yes |
–20 |
+1002) |
Corrosion-resistant, Corrotect coating |
|
GE..-XL-KRR-B-FA125 |
20 |
50 |
‒ |
‒ |
Eccentric locking collar |
R |
yes |
Group 3 |
PA66 |
GA47 |
yes |
–20 |
+1002) |
Corrosion-resistant, Corrotect coating |
|
SUB |
20 |
50 |
‒ |
‒ |
Grub screws |
RSR |
yes |
Group 3 |
Corrosion-resistant VA steel |
FM222 |
yes |
–35 |
+100 |
Corrosion-resistant, VA design |
|
SUC |
12 |
50 |
‒ |
‒ |
Grub screws |
RSR |
yes |
Group 3 |
Corrosion-resistant VA steel |
FM222 |
yes |
–35 |
+100 |
Corrosion-resistant, VA design, with flinger shield |
|
SUG |
20 |
50 |
‒ |
‒ |
Eccentric locking collar |
RSR |
yes |
Group 3 |
Corrosion-resistant VA steel |
FM222 |
yes |
–35 |
+100 |
Corrosion-resistant, VA design |
|
Black Series (radial insert ball bearings in accordance with JIS) |
|||||||||||||||
UC |
12 |
90 |
1/2 |
3 1/2 |
Grub screws |
RSR |
yes |
C3 |
PA66 |
GA13 |
yes |
–20 |
+1002) |
Black Series, Durotect BS coating, basic corrosion protection |
|
UK |
20 |
80 |
‒ |
‒ |
Adapter sleeve to JIS B 1552 |
RSR |
yes |
C4 |
PA66 |
GA13 |
yes |
–20 |
+1002) |
Black Series, Durotect BS coating, basic corrosion protection |
- Recommended application temperature. If temperatures exceed +100 °C, relubrication must be carried out regularly.
- Temporary temperature peaks are possible up to 120 °C.
Load carrying capacity
Radial load carrying capacity
Suitable for very high radial loads
The balls are in contact with the raceways at one point only. Under purely radial load, the contact points between the rolling elements and raceways lie at the centre of the raceway. As a result, the connection between the contact points passes through the radial plane, i. e. the optimum load direction is a purely radial load ➤ Figure and ➤ Figure. Radial insert ball bearings can therefore support very high radial loads.
Larger ball sets permit higher loads
The load carrying capacity is dependent on the bearing series and the size of the ball set in the reference bearings. As a result, the deep groove ball bearing series 60 with a smaller bearing cross-section cannot support loads as high as those with the standard series 62 of the same dimensions (relative to the bore diameter d) with a larger ball set. The heavy bearing series 63 with the largest ball set is suitable for even higher loads when used for the same bore diameter ➤ Figure.
Reference bearings, comparison of cross-section and load carrying capacity for bearings with d = 40 mm Cr = basic dynamic load rating |
![]() |
Axial load carrying capacity
Capable of supporting axial loads in both directions
Due to the deep raceway grooves in the bearing rings and the narrow osculation between the raceway grooves and balls, radial insert ball bearings can support axial loads in both directions ➤ Figure and ➤ Figure. The axial load carrying capacity is dependent, for example, on the bearing size, the internal construction and the operating clearance. If the axial load is too high, however, this can increase the running noise and considerably reduce the operating life of the bearings.
If there is any uncertainty regarding the axial load carrying capacity of the bearings, please consult Schaeffler.
Compensation of angular misalignments
The units must not be used to support swivelling or tumbling motion ➤ link.
Compensation of static misalignments
Bearings with a spherical outer ring outside surface, fitted in housings with a concave bore, can compensate for static misalignment of the shaft ➤ Figure, ➤ Figure and ➤ Figure.
The compensation of misalignments must be within the permissible angle of ±5° for maintenance-free housing units or ±2,5° for housing units with a relubrication facility. The precondition is that the centre axes of the inner rings must lie on a common straight line.
For units with a lubrication groove in the housing and lubrication hole in the radial insert ball bearing, the following applies:
- Up to ±2,5°, the units can be relubricated.
- Between ±2,5° and ±5°, the possibility of relubrication is dependent on the specific unit. Please contact us in this case.
- Over ±5°, relubrication is no longer possible
Compensation of static housing misalignment ±5° for maintenance-free bearings ±2,5° for bearings with relubrication facility |
![]() |
Compensation of static shaft misalignment ±5° for maintenance-free bearings ±2,5° for bearings with relubrication facility |
![]() |
Compensation of static shaft misalignment ±5° for maintenance-free bearings |
![]() |
Radial insert ball bearings are not suitable for continuous oscillating motion of the outer ring in the housing bore
Radial insert ball bearings cannot be used if the outer ring undergoes continuous oscillating motions in the housing bore. This is the case if the shaft has an excessively large undersize or the centre axes of the inner rings deviate so much from a common straight line that the tilting clearance present in the bearing is exceeded. In this case, the outer ring is included in the oscillating motion of the bearing occurring with each revolution by the ball set of the inner ring. This situation is shown in the figures for a bent shaft and a roller with journals that are parallel but not in alignment ➤ Figure and ➤ Figure. This geometrical defect of the machine parts causes tilting of the bearing during mounting and continuous oscillating motion of the outer ring during rotation.
Oscillating motion of outer rings with a bent shaft |
![]() |
Oscillating motion of outer rings with non-aligned journal |
![]() |
An underdimensioned shaft will cause continuous tumbling motions
A critical situation also arises with a bearing arrangement of an underdimensioned shaft ➤ Figure. While it is still aligned when free from load, it bends under load as shown by the example of a return roller. As a result, the bearings undergo continuous tumbling motion. If circumferential load is still present on the outer ring in this case, the deflection of the housing bore is accelerated (leading to wear).
Oscillating motion of outer rings with a deflected shaft |
![]() |
Lubrication
Radial insert ball bearings sealed on both sides are lubricated with a high quality lithium soap grease with a mineral oil base, which has good anti-corrosion characteristics ➤ Table. Bearings with a spherical outside surface can be relubricated, with the exception of a few series (such as AY..-XL-NPP-B).
Radial insert ball bearings with a cylindrical outside surface have the maximum grease filling. The grease filling is measured so that it is sufficient for the entire life of the bearing. As a result, these bearings are generally maintenance-free. Radial insert ball bearings can have sheet steel washers extended outwards and angled downwards, forming a larger grease chamber. Only a few designs with a cylindrical outside surface can be additionally relubricated.
Radial insert ball bearings with a rubber interliner or aligning ring cannot be relubricated.
Recommended greases for radial insert ball bearings
Designation1) |
Classification |
Type of grease |
Recommended Arcanol grease for relubrication |
---|---|---|---|
GA13 |
Standard ball bearing and insert bearing grease |
Lithium soap Mineral oil |
Multi3 |
GA22 |
Free-running grease |
Lithium soap Ester oil |
‒ |
L069 |
Radial insert ball bearing grease |
Polycarbamide Ester oil |
‒ |
GA11 |
Rolling bearing grease resistant |
PTFE Alkoxyfluoroether |
Temp200 |
GA47 |
Rolling bearing grease resistant |
Barium complex soap Mineral oil |
‒ |
L178 |
Rolling bearing grease |
Barium complex soap PAO oil |
‒ |
continued ▼ |
- GA stands for Grease Application Group, based on Grease Spec 00.
Recommended greases for radial insert ball bearings
Designation1) |
Operating temperature range |
Upper continuous limit temperature ϑupper limit2) |
NLGI class |
Speed parameter n · dM |
ISO VG class (base oil) |
|||
---|---|---|---|---|---|---|---|---|
°C |
°C |
min-1 · mm |
||||||
from |
to |
from |
to |
from |
to |
|||
GA13 |
–30 |
+120 |
+75 |
3 |
‒ |
500 000 |
68 |
150 |
GA22 |
–50 |
+120 |
+70 |
2 |
‒ |
1 500 000 |
10 |
22 |
L069 |
–40 |
+180 |
+120 |
2 |
‒ |
700 000 |
68 |
220 |
GA11 |
–30 |
+260 |
+200 |
2 |
‒ |
300 000 |
460 |
680 |
GA47 |
–20 |
+130 |
+70 |
1 |
2 |
350 000 |
150 |
320 |
L178 |
–20 |
+142 |
+75 |
2 |
‒ |
800 000 |
22 |
46 |
continued ▲ |
- GA stands for Grease Application Group, based on Grease Spec 00.
- The upper continuous limit temperature ϑupperlimit must not be exceeded if a temperature-induced reduction in grease operating life is to be avoided.
Compatibility with plastic cages
When using bearings with plastic cages, compatibility between the lubricant and the cage material must be ensured if synthetic oils, lubricating greases with a synthetic oil base or lubricants containing a high proportion of EP additives are used.
Radial insert ball bearings in corrosion-resistant VA design
Initial greasing is carried out with an aluminium complex soap grease with food applications approval to NSF-H1, which is sufficient in many cases for the operating life of the bearings. For relubrication, the outer rings have lubrication holes on their circumference.
Black Series
The Black Series radial insert ball bearings in accordance with JIS are greased using a grease in Grease Group GA13 ➤ Table.
Sealing
Non-contact or contact seals
A basic distinction is made between contact and non-contact seals in the adjacent construction and the bearing.
The sealing arrangement has a considerable influence on the operating life of a bearing arrangement. Its function is to retain the lubricant in the bearing and prevent the ingress of contaminants into the bearing.
Contaminants may have various effects:
- A large quantity of very small, abrasive particles causes wear in the bearing. The increase in clearance or noise brings the operating life of the bearing to an end
- Large, overrolled hard particles reduce the fatigue life since pittings occur at the indentation points under high bearing loads
Type-specific seals
The different designs of seals are explained below. The type-specific seals used in the individual radial insert ball bearings are summarised in the table of features ➤ Table and ➤ Table.
Overview of seal types
Seals for radial insert ball bearings are of a three-piece design. This concept offers, due to the rigidly rolled-in inner sheet steel washer, optimum seating in the bearing as well as concentric alignment of the seal lip to the inner ring. The contact seals on both sides of the bearing give protection against contamination and the loss of lubricant.
Seals for radial insert ball bearings are available in various designs ➤ Table. The stated suffix is included in the ordering designation and explained in the table of suffixes ➤ section.
Seal types
P seal (NPP) |
|
![]() |
Two zinc-coated sheet steel washers (or in a corrosion- In order to protect the seal lip from mechanical damage, For use in narrow radial insert ball bearings with inner ring extended on one side. |
R seal (KRR) |
|
![]() |
Two zinc-coated sheet steel washers extended outwards and angled downwards with intermediate NBR or PTFE part Substantial grease reservoir due to the sheet steel washers which are extended outwards and angled downwards. Used |
R seal with flinger shield (KRR-..-2C) |
|
![]() |
As R seal, but with outer flinger shield with corrosion Additional sealing action without restriction on speed |
continued ▼ |
Seal types
T seal (KTT) |
|
![]() |
Two zinc-coated sheet steel washers with intermediate Lower speeds due to higher friction. |
L seal (labyrinth seal) (KLL) |
|
![]() |
Two zinc-coated sheet steel washers extended outwards Substantial grease reservoir due to the sheet steel washers which are extended outwards and angled downwards. For use in bearings with inner ring extended on both sides. |
RSR seal (2RSR) |
|
![]() |
Single piece, zinc-coated sheet steel washer with vulcanised and radially preloaded seal lip made from NBR. Used in radial insert ball bearings with integral adapter sleeve. |
RSR seal with flinger shield |
|
![]() |
Single piece, sheet steel washer in corrosion-resistant In the Black Series, the flinger shield has a Durotect BS coating. |
Sealing cartridge with flinger shield |
|
![]() |
Design identical to normal cartridge seal but supplemented |
Combined sealing washer and flinger shield with protective shield |
|
![]() |
Design identical to normal sealing washer and flinger shield |
continued ▲ |
BRS seals
Bearings with BRS seals can be supplied by agreement ➤ Figure.
Suitable for very high speeds
The friction in this case is as low as that in bearings with sealing shields. They have the advantage over these, however, that the outer rubber-elastic rim gives good sealing when fitted in the slot in the outer ring. This is important in the case of a rotating outer ring, since the base oil in the grease is separated from the soap suspension by centrifugal force and would escape through the unsealed metallic seat in the outer ring if sealing shields were fitted.
BRS seals |
![]() |
Non-contact seals in the adjacent construction
With non-contact seals, only lubricant friction occurs in the lubrication gap. The seals do not undergo wear and remain capable of operation for a long period. Since they generate no heat, non-contact seals are also suitable for very high speeds.
Speeds
Speed limits for radial insert ball bearings
The speed limits are dependent on the load, the clearance between the bearing bore and shaft and the friction of the seals in the case of bearings with contact seals.
Speed limits are guide values
Guide values for the permissible speeds can be derived from the diagram ➤ Figure.
In the case of load ratios Cr/P > 13, the speeds can be increased. At Cr/P < 5, location by means of a fit is recommended for a shaft roughness of Ra 0,3 ➤ link. In order to ensure slippage-free operation, the minimum radial load must be observed ➤ section.
Permissible speeds for radial insert ball bearings n = permissible speed d = bore diameter Cr/P = load ratio h5, h6, h9 = shaft tolerance (subject to envelope requirement Ⓔ)
|
![]() |
In the stated applications with load ratios Cr/P < 5, please contact us.
Example of permissible speed calculation
Given:
- Shaft tolerance h6 Ⓔ
- Radial insert ball bearing GRAE30-XL-NPP-B
- Ball set 206
- Basic dynamic load rating Cr 20 700 N
- Load P 1 300 N
- Sealing seals P
Required:
- Load ratio Cr/P = 20 700 N/1 300 N Cr/P > 13
- Permissible speed n ≈ 4 300 min-1 ➤ Figure
Noise
Schaeffler Noise Index
The Schaeffler Noise Index (SGI) is not yet available for this bearing type ➤ link. The data for these bearing series will be introduced and updated in stages.
Temperature range
The possible operating temperatures of radial insert ball bearings may differ according to the cage design and the material of the seal lips ➤ Table.
Radial insert ball bearings for a high or expanded temperature range have the suffixes FA164 or FA101 in the designation ➤ Table.
Permissible temperature ranges
Operating temperature |
Radial insert ball bearing |
|||||||
---|---|---|---|---|---|---|---|---|
with polyamide cage PA66 |
with sheet steel cage |
with high grade steel cage |
||||||
with NBR seal lip |
with PTFE seal lip and labyrinth seal |
with NBR seal lip |
||||||
°C |
°C |
°C |
||||||
FA1013) |
FA1644) |
|||||||
from |
to |
from |
to |
from |
to |
from |
to |
|
|
–20 |
+1001)2) |
–40 |
+180 |
+150 |
+250 |
–35 |
+100 |
- Temporary temperature peaks are possible up to +120 °C.
- In the case of radial insert ball bearings with a rubber interliner, the maximum operating temperature is reduced to +85 °C.
- High and low temperature design (suffix FA101) ➤ section.
- High temperature design (suffix FA164) ➤ section.
Limiting values
The operating temperature of the bearings is limited by:
- the dimensional stability of the bearing rings and rolling elements
- the cage
- the lubricant
- the seals
In the event of anticipated temperatures which lie outside the stated values, please contact Schaeffler.
Cages
Rolling bearing cages are subdivided into sheet metal and solid cages.
Both sheet metal and solid cages for radial insert ball bearings are exclusively ball-guided.
The most important functions of the cage are:
- to separate the rolling elements from each other, in order to minimise friction and heat generation
- to maintain the rolling elements at the same distance from each other, in order to ensure uniform load distribution
- to guide the rolling elements in the unloaded zone of the bearing
Sheet metal cages
These cages are predominantly made from steel ➤ Figure. In comparison with solid cages made from metal, they are of lower mass.
Since a sheet metal cage only fills a small proportion of the gap between the inner and outer ring, lubricant can easily reach the interior of the bearing and is held on the cage.
Radial insert ball bearing with sheet metal cages
|
![]() |
Solid cages made from polyamide PA66
Solid cages made from polyamide PA66 are produced using the injection moulding process ➤ Figure and ➤ Figure. As a result, cage types can generally be realised that allow designs with particularly high load carrying capacity. The elasticity and low mass of polyamide are favourable under shock type bearing loads, high accelerations and decelerations and tilting of the bearing rings in relation to each other. Polyamide cages have very good sliding and emergency running characteristics.
Cages made from glass fibre reinforced polyamide PA66 are suitable for continuous temperatures up to +120 °C. Due to the NBR seal used, the continuous temperature for the radial insert ball bearing is reduced ➤ section.
Solid polyamide cage for standard bearings
|
![]() |
Solid polyamide cage for Black Series
|
![]() |
Internal clearance
The differentiation of radial insert ball bearings between the ISO range and JIS range (Black Series) must be taken into consideration for the radial internal clearance.
Radial internal clearance of radial insert ball bearings
The radial internal clearance of most series is Group 3 in accordance with ISO 5753-1 ➤ Table and is thus larger than for normal deep groove ball bearings ➤ Table. The radial internal clearance is subdivided into groups in accordance with ISO 5753-1 ➤ Figure.
The larger internal clearance allows better support of misalignments and shaft deflections.
Radial internal clearance |
![]() |
Radial internal clearance of radial insert ball bearings (excluding Black Series)
Bore |
Radial internal clearance |
||||||||
---|---|---|---|---|---|---|---|---|---|
d mm |
Group N μm |
Group 3 μm |
Group 4 μm |
Group 5 μm |
|||||
over |
incl. |
min. |
max. |
min. |
max. |
min. |
max. |
min. |
max. |
2,5 |
6 |
2 |
13 |
8 |
23 |
‒ |
‒ |
‒ |
‒ |
6 |
10 |
2 |
13 |
8 |
23 |
14 |
29 |
20 |
37 |
10 |
18 |
3 |
18 |
11 |
25 |
18 |
33 |
25 |
45 |
18 |
24 |
5 |
20 |
13 |
28 |
20 |
36 |
28 |
48 |
24 |
30 |
5 |
20 |
13 |
28 |
23 |
41 |
30 |
53 |
30 |
40 |
6 |
20 |
15 |
33 |
28 |
46 |
40 |
64 |
40 |
50 |
6 |
23 |
18 |
36 |
30 |
51 |
45 |
73 |
50 |
65 |
8 |
28 |
23 |
43 |
38 |
61 |
55 |
90 |
65 |
80 |
10 |
30 |
25 |
51 |
46 |
71 |
65 |
105 |
80 |
100 |
12 |
36 |
30 |
58 |
53 |
84 |
75 |
120 |
100 |
120 |
15 |
41 |
36 |
66 |
61 |
97 |
90 |
140 |
120 |
140 |
18 |
48 |
41 |
81 |
71 |
114 |
105 |
160 |
140 |
160 |
18 |
53 |
46 |
91 |
81 |
130 |
120 |
180 |
Radial internal clearance of Black Series (radial insert ball bearings in accordance with JIS)
The radial internal clearance in accordance with JIS B 1520 is C3 for radial insert ball bearings UC and C4 for radial insert ball bearings UK. It is thus larger than in the case of normal deep groove ball bearings ➤ Table.
The larger internal clearance allows better support of misalignments and shaft deflections.
Radial internal clearance of Black Series
Bore |
Ball set |
Outside |
Radial |
||||
---|---|---|---|---|---|---|---|
d |
D |
C3 |
C4 |
||||
mm |
inch |
mm |
μm |
μm |
|||
min. |
max. |
min. |
max. |
||||
12 |
‒ |
204 |
47 |
13 |
28 |
20 |
36 |
12,7 |
1/2 |
204 | 47 | 13 | 28 | 20 | 36 |
14,288 |
9/16 |
204 | 47 | 13 | 28 | 20 | 36 |
15 |
‒ |
204 | 47 | 13 | 28 | 20 | 36 |
15,875 |
5/8 |
204 | 47 | 13 | 28 | 20 | 36 |
17 |
‒ |
204 | 47 | 13 | 28 | 20 | 36 |
17,462 |
11/16 |
204 | 47 | 13 | 28 | 20 | 36 |
19,05 |
3/4 |
204 | 47 | 13 | 28 | 20 | 36 |
20 |
‒ |
204 | 47 | 13 | 28 | 20 | 36 |
20,638 |
13/16 |
205 |
52 |
13 |
28 |
23 |
41 |
22,225 |
7/8 |
205 | 52 | 13 | 28 | 23 | 41 |
23,812 |
15/16 |
205 | 52 | 13 | 28 | 23 | 41 |
25 |
‒ |
205 | 52 | 13 | 28 | 23 | 41 |
25,4 |
1 |
205 | 52 | 13 | 28 | 23 | 41 |
26,988 |
1 1/16 |
206 |
62 |
13 | 28 | 23 | 41 |
28,575 |
1 1/8 |
206 | 62 | 13 | 28 | 23 | 41 |
30 |
‒ |
206 | 62 | 13 | 28 | 23 | 41 |
30,162 |
1 3/16 |
206 | 62 | 13 | 28 | 23 | 41 |
31,75 |
1 1/4 |
206 | 62 | 13 | 28 | 23 | 41 |
31,75 |
1 1/4 |
207 | 72 | 15 | 33 | 28 | 46 |
33,338 |
1 5/16 |
207 | 72 | 15 | 33 | 28 | 46 |
34,925 |
1 3/8 |
207 | 72 | 15 | 33 | 28 | 46 |
35 |
‒ |
207 | 72 | 15 | 33 | 28 | 46 |
36,512 |
1 7/16 |
207 | 72 | 15 | 33 | 28 | 46 |
38,1 |
1 1/2 |
208 | 80 | 15 | 33 | 28 | 46 |
39,688 |
1 9/16 |
208 | 80 | 15 | 33 | 28 | 46 |
40 |
‒ |
208 | 80 | 15 | 33 | 28 | 46 |
41,275 |
1 5/8 |
209 | 85 | 18 | 36 | 30 | 51 |
42,862 |
1 11/16 |
209 | 85 | 18 | 36 | 30 | 51 |
44,45 |
1 3/4 |
209 | 85 | 18 | 36 | 30 | 51 |
45 |
‒ |
209 | 85 | 18 | 36 | 30 | 51 |
46,038 |
1 13/16 |
210 | 90 | 18 | 36 | 30 | 51 |
47,625 |
1 7/8 |
210 | 90 | 18 | 36 | 30 | 51 |
49,212 |
1 15/16 |
210 | 90 | 18 | 36 | 30 | 51 |
50 |
‒ |
210 | 90 | 18 | 36 | 30 | 51 |
50,8 |
2 |
210 | 90 | 18 | 36 | 30 | 51 |
continued ▼ |
Radial internal clearance of Black Series
Bore |
Ball set |
Outside |
Radial |
||||
---|---|---|---|---|---|---|---|
d |
D |
C3 |
C4 |
||||
mm |
inch |
mm |
μm |
μm |
|||
min. |
max. |
min. |
max. |
||||
50,8 |
2 |
211 | 100 | 23 | 43 | 38 | 61 |
52,388 |
2 1/16 |
211 | 100 | 23 | 43 | 38 | 61 |
53,975 |
2 1/8 |
211 | 100 | 23 | 43 | 38 | 61 |
55 |
‒ |
211 | 100 | 23 | 43 | 38 | 61 |
55,562 |
2 3/16 |
211 | 100 | 23 | 43 | 38 | 61 |
57,15 |
2 1/4 |
212 | 110 | 23 | 43 | 38 | 61 |
58,738 |
2 5/16 |
212 | 110 | 23 | 43 | 38 | 61 |
60 |
‒ |
212 | 110 | 23 | 43 | 38 | 61 |
60,325 |
2 3/8 |
212 | 110 | 23 | 43 | 38 | 61 |
61,912 |
2 7/16 |
212 | 110 | 23 | 43 | 38 | 61 |
63,5 |
2 1/2 |
213 | 120 | 23 | 43 | 38 | 61 |
65 |
‒ |
213 | 120 | 23 | 43 | 38 | 61 |
65,09 |
2 9/16 |
213 | 120 | 23 | 43 | 38 | 61 |
66,675 |
2 5/8 |
214 | 125 | 25 | 51 | 46 | 71 |
68,262 |
2 11/16 |
214 | 125 | 25 | 51 | 46 | 71 |
69,85 |
2 3/4 |
214 | 125 | 25 | 51 | 46 | 71 |
70 |
‒ |
214 | 125 | 25 | 51 | 46 | 71 |
71,438 |
2 13/16 |
215 | 130 | 25 | 51 | 46 | 71 |
73,025 |
2 7/8 |
215 | 130 | 25 | 51 | 46 | 71 |
74,612 |
2 15/16 |
215 | 130 | 25 | 51 | 46 | 71 |
75 |
‒ |
215 | 130 | 25 | 51 | 46 | 71 |
76,2 |
3 |
215 | 130 | 25 | 51 | 46 | 71 |
77,787 |
3 1/16 |
216 | 140 | 25 | 51 | 46 | 71 |
79,375 |
3 1/8 |
216 | 140 | 25 | 51 | 46 | 71 |
80 |
‒ |
216 | 140 | 25 | 51 | 46 | 71 |
80,962 |
3 3/16 |
216 | 140 | 25 | 51 | 46 | 71 |
82,55 |
3 1/4 |
217 | 150 | 30 | 58 | 53 | 84 |
84,137 |
3 5/16 |
217 | 150 | 30 | 58 | 53 | 84 |
85 |
‒ |
217 | 150 | 30 | 58 | 53 | 84 |
87,312 |
3 7/16 |
217 | 150 | 30 | 58 | 53 | 84 |
88,9 |
3 1/2 |
218 | 160 | 30 | 58 | 53 | 84 |
90 |
‒ |
218 | 160 | 30 | 58 | 53 | 84 |
93,662 |
3 11/16 |
219 | 170 | 30 | 58 | 53 | 84 |
95 |
‒ |
219 | 170 | 30 | 58 | 53 | 84 |
100 |
‒ |
220 | 180 | 30 | 58 | 53 | 84 |
100,012 |
3 15/16 |
220 | 180 | 30 | 58 | 53 | 84 |
101,6 |
4 |
220 | 180 | 30 | 58 | 53 | 84 |
continued ▲ |
Dimensions, tolerances
The dimensions of special bearings (F../Z..) may deviate from the standard.
The main dimensions of the standard bearings and corrosion-resistant radial insert ball bearings correspond to ISO 9628 and DIN 626‑1 ➤ link.
The main dimensions of the Black Series correspond to JIS B 1558 ➤ link.
The limiting dimensions for chamfer dimensions correspond to DIN 620‑6. Overview and limit values ➤ link.
Symmetrical ring cross-section with identical chamfer dimensions on both rings d = inside diameter r1, r2 = chamfer dimensions
|
![]() |
Normal tolerances of standard bearings
The outside diameter of the bearings corresponds to tolerance class Normal in accordance with ISO 492 ➤ Table. The inner ring bore has a plus tolerance to facilitate mounting of the bearing.
Tolerances of radial insert ball bearings
Inner ring |
Outer ring |
||||||
---|---|---|---|---|---|---|---|
Nominal dimension Bore d |
Deviation tΔdmp |
Nominal dimension Outside diameter D |
Deviation1)2) tΔDmp |
||||
mm |
μm |
mm |
μm |
||||
over |
incl. |
L |
U |
over |
incl. |
U |
L |
12 |
18 |
0 |
+18 |
30 |
50 |
0 |
–11 |
18 |
24 |
0 |
+18 |
50 |
80 |
0 |
–13 |
24 |
30 |
0 |
+18 |
80 |
120 |
0 |
–15 |
30 |
40 |
0 |
+18 |
120 |
150 |
0 |
–18 |
40 |
50 |
0 |
+18 |
150 |
180 |
0 |
–25 |
50 |
60 |
0 |
+18 |
180 |
250 |
0 |
–30 |
60 |
90 |
0 |
+25 |
‒ |
‒ |
‒ |
‒ |
90 |
120 |
0 |
+30 |
‒ |
‒ |
‒ |
‒ |
- In the case of sealed bearings, the largest and smallest values of the outside diameter can deviate from the mean value by approximately 0,03 mm.
- Outside diameter tolerances also valid for 2..-KRR and 2..-NPP-B.
Tolerance symbols ➤ Table
U = upper limit deviation
L = lower limit deviation
Standard tolerances of corrosion-resistant radial insert ball bearings
The outside diameter of the bearings corresponds to tolerance class Normal in accordance with ISO 492 ➤ Table and ➤ Table. The inner ring bore has a plus tolerance to facilitate mounting of the bearing.
Tolerances of radial insert ball bearings, with Corrotect coating
Inner ring |
Outer ring |
||||||
---|---|---|---|---|---|---|---|
Nominal dimension Bore d |
Deviation tΔdmp |
Nominal dimension Outside diameter D |
Deviation1) tΔDmp |
||||
mm |
μm |
mm |
μm |
||||
over |
incl. |
L |
U |
over |
incl. |
U |
L |
12 |
18 |
0 |
+18 |
30 |
50 |
0 |
–11 |
18 |
24 |
0 |
+18 |
50 |
80 |
0 |
–13 |
24 |
30 |
0 |
+18 |
80 |
120 |
0 |
–15 |
30 |
40 |
0 |
+18 |
120 |
150 |
0 |
–18 |
40 |
50 |
0 |
+18 |
150 |
180 |
0 |
–25 |
50 |
60 |
0 |
+18 |
180 |
250 |
0 |
–30 |
60 |
90 |
0 |
+25 |
‒ |
‒ |
‒ |
‒ |
90 |
120 |
0 |
+30 |
‒ |
‒ |
‒ |
‒ |
- In the case of sealed bearings, the largest and smallest values of the outside diameter can deviate from the mean value by approx. 0,03 mm.
U = upper limit deviation
L = lower limit deviation
Tolerances of radial insert ball bearings, corrosion-resistant VA design
Inner ring |
Outer ring |
||||||
---|---|---|---|---|---|---|---|
Nominal dimension Bore d |
Deviation tΔdmp |
Nominal dimension Outside diameter D |
Deviation1) tΔDmp |
||||
mm |
μm |
mm |
μm |
||||
over |
incl. |
L |
U |
over |
incl. |
U |
L |
18 |
24 |
0 |
+25 |
50 |
80 |
0 |
–13 |
24 |
30 |
0 |
+25 |
80 |
120 |
0 |
–13 |
30 |
40 |
0 |
+25 |
120 |
150 |
0 |
–13 |
40 |
50 |
0 |
+25 |
150 |
180 |
0 |
–13 |
50 |
60 |
0 |
+25 |
180 |
250 |
0 |
–13 |
- In the case of sealed bearings, the largest and smallest values of the outside diameter can deviate from the mean value by approx. 0,03 mm.
Tolerance symbols ➤ Table
U = upper limit deviation
L = lower limit deviation
Normal tolerances of Black Series (radial insert ball bearings in accordance with JIS)
The outside diameter tolerances of the bearings correspond to the tolerances in accordance with JIS B 1558 ➤ Table. The inner ring bore has a plus tolerance to facilitate mounting of the bearing.
Tolerances of inner ring, Black Series
Nominal bearing bore diameter |
Deviation1) |
Width deviation |
|||
---|---|---|---|---|---|
d |
Δdmp |
ΔBs |
|||
mm |
μm |
μm |
|||
over |
incl. |
min. |
max. |
min. |
max. |
10 |
18 |
0 |
+15 |
–120 |
0 |
18 |
31,75 |
0 |
+18 |
–120 |
0 |
31,75 |
50,8 |
0 |
+21 |
–120 |
0 |
50,8 |
80,962 |
0 |
+24 |
–150 |
0 |
80,962 |
120 |
0 |
+28 |
–200 |
0 |
- This corresponds to the arithmetic mean value derived from the largest and smallest diameters (measured using a two-point measuring device).
Tolerances of outer ring, Black Series
Nominal outside diameter |
Deviation1) |
||
---|---|---|---|
Dsp |
ΔDm |
||
mm |
μm |
||
over |
incl. |
min. |
max. |
30 |
50 |
–11 |
0 |
50 |
80 |
–13 |
0 |
80 |
120 |
–15 |
0 |
120 |
150 |
–18 |
0 |
150 |
180 |
–25 |
0 |
180 |
250 |
–30 |
0 |
- In the case of sealed bearings, the largest and smallest values of the outside diameter can deviate from the mean value by approx. 0,03 mm.
Suffixes
The suffix defines special designs and features and follows the basic designation in the ordering designation ➤ Table and ➤ Table.
Suffixes and corresponding descriptions
Suffix |
Description |
|
---|---|---|
AS2/V |
Bearing outer ring with two lubrication holes |
Standard |
B |
Bearing with spherical outside surface of outer ring |
Standard |
2C |
Flinger shield on both sides |
Standard |
FA |
Manufacturing variant |
Standard |
FA101 |
High and low temperature design –40 °C to +180 °C |
Standard |
FA106 |
Bearing subjected to special noise testing |
Standard |
FA107 |
Bearing with lubrication holes on the locating side |
Standard |
FA125 |
With Corrotect coating, corrosion-resistant |
Standard |
FA164 |
High temperature design from +150 °C to +250 °C |
Standard |
KRR |
Lip seal on both sides (seal R) |
Standard |
KLL |
Labyrinth seal on both sides (seal L) |
Standard |
KTT |
Triple lip seal on both sides (seal T) |
Standard |
NPP |
Lip seal on both sides (seal P) |
Standard |
2RSR |
Lip seal on both sides (vulcanised) |
Standard |
AH |
Features differing from the original |
Standard |
NR |
Slot and snap ring for radial insert ball bearing |
Standard |
OSE |
Bearing without locking element |
Standard |
XL |
Bearing design in X-life quality |
Standard |
Suffixes and corresponding descriptions, additional notations for (self‑aligning) deep groove ball bearings
Suffix |
Description |
|
---|---|---|
L402/70 |
Grease code according to Schaeffler standard, 70% grease quantity |
Available by agreement |
GA47/70 |
Grease Group, 70% grease quantity |
Available by agreement |
Structure of bearing designation
The designations of radial insert ball bearings with an extended inner ring and (self-aligning) deep groove ball bearings follow an almost identical model ➤ Table, ➤ Figure and ➤ Figure. Radial insert ball bearings with a steel aligning ring or rubber interliner differ from this model ➤ link, which is also the case for Black Series and corrosion-resistant radial insert ball bearings ➤ link.
Basic designations and corresponding descriptions for radial insert ball bearings with extended inner ring or (self‑aligning) deep groove ball bearings
Basic designation |
Description of basic designation |
||
---|---|---|---|
Stated in designation |
Not stated |
||
|
G |
Relubrication facility |
Without relubrication facility |
![]() |
N |
Heavy bearing series (bearing series 63) |
Standard bearing series (bearing series 62) |
![]() |
RA |
Location of inner ring by meansof eccentric locking collar, with inner ring extended on one side |
Standard bearing series (bearing series 62) |
![]() |
AY |
Location of inner ring by means of two grub screws, with inner ring extended on one side |
Standard bearing series (bearing series 62) |
![]() |
SH |
Location of inner ring by means of adapter sleeve (special ball set) |
Standard bearing series (bearing series 62) |
|
RAL |
Location of inner ring by means of eccentric locking collar, light bearing series (bearing series 60) |
Standard bearing series (bearing series 62) |
![]() ![]() |
VK |
Inner ring with square bore |
Inner ring with a cylindrical bore |
![]() ![]() |
SK |
Inner ring with hexagonal bore |
Inner ring with a cylindrical bore |
|
Y |
Location of inner ring by means of two grub screws, with inner ring extended on both sides |
Location of inner ring by means of eccentric locking collar, with inner ring extended on both sides |
![]() |
L |
Inner ring with drive slot (non-locating bearing) |
Location of inner ring by means of eccentric locking collar, with inner ring extended on both sides |
|
E |
Metric bore |
Inch size bore |
![]() |
1 |
Inch size bore (only for inner ring extended on both sides) |
Inch size bore |
|
50 |
Bore code; bore diameter in mm (example: 50 = 50 mm) |
‒ |
![]() |
0121) |
Bore code; bore diameter in inches (example: 012 = 3/4 inch) |
‒ |
|
2042) |
Ball set code (sole notation for (self-aligning) deep groove ball bearings; inner ring with fit) |
‒ |
|
214 |
Ball set 214 (additional notation) |
Standard (ball set 213) |
- Three-digit notation for bore diameter. The first digit is complete inches, while the last two digits are stated in sixteenths, for example 12/16.
- The first digit of the ball set code corresponds to the standardised series designation for radial deep groove ball bearings without the leading 6, for example bearing series 62.
The other digits represent the bore code, for example 04. For all rolling bearings in the range from d = 20 mm to d = 480 mm, the bore code is created by dividing the dimension of the bearing bore by 5.
Radial insert ball bearing with extended inner ring:
Example: |
![]() |
(Self-aligning) deep groove ball bearing:
Example: |
![]() |
Radial insert ball bearings with steel aligning ring or rubber interliner
Radial insert ball bearings with a steel aligning ring or rubber interliner follow a separate designation model ➤ Table and ➤ Table.
Basic designations and corresponding descriptions for radial insert ball bearings with steel aligning ring
Basic designation |
Description of basic designation |
|
---|---|---|
|
B |
Self-aligning deep groove ball bearing |
![]() |
P |
Radial insert ball bearing with eccentric locking collar |
|
E |
Aligning ring |
Basic designations and corresponding descriptions for radial insert ball bearings with rubber interliner
Basic designation |
Description of basic designation |
|
---|---|---|
|
CR |
Rubber interliner with locating shoulder |
![]() |
RABR |
Rubber interliner with spherical outside surface |
![]() |
RCR |
Rubber interliner with cylindrical outside surface and mounting chamfer |
![]() |
RCSM |
Rubber interliner with cylindrical outside surface |
|
B |
Radial insert ball bearing RAE..-NPP-B ➤ Table |
![]() |
A |
Radial insert ball bearing RALE..-NPP-B ➤ Table |
Radial insert ball bearing with steel aligning ring: designation structure
|
![]() |
Radial insert ball bearing with rubber interliner: designation structure
|
![]() |
Black Series and corrosion-resistant radial insert ball bearings
Radial insert ball bearings in accordance with JIS (Black Series) and corrosion-resistant radial insert ball bearings follow a separate designation model ➤ Table.
Basic designations and corresponding descriptions for Black Series and corrosion‑resistant radial insert ball bearings
Basic designation |
Description of basic designation |
|
---|---|---|
Stated in designation |
Not stated |
|
S |
High grade steel design of radial insert ball bearing |
Normal design (for Black Series) |
UB |
Inner ring extended on one side, |
‒ |
UC | Inner ring extended on both sides, with grub screws and flinger shields on both sides | |
UG | Inner ring extended on one side, with eccentric locking collar | |
UK | With adapter sleeve in accordance with JIS B 1552 and flinger shields on both sides | |
2081) | Ball set code, metric dimensions | |
208-242) | Ball set code, bore diameter in inch dimensions |
- The first digit of the ball set code corresponds to the standardised series designation for radial deep groove ball bearings without the leading 6, for example bearing series 62.
The other digits represent the bore code, for example 08. For all rolling bearings in the range from d = 20 mm to d = 480 mm, the bore code is created by dividing the dimension of the bearing bore by 5. - Notation for bore diameter in sixteenths, for example 24/16 = 1 1/2 inch.
Black Series and corrosion‑resistant radial insert ball bearings: designation structure Basic designation ➤ Table |
![]() |
Dimensioning
Equivalent dynamic bearing load
P = Fr under purely radial load of constant magnitude and direction
The basic rating life equation L = (Cr/P)p used in the dimensioning of bearings under dynamic load assumes a load of constant magnitude and direction. In radial bearings, this is a purely radial load Fr. If this condition is met, the bearing load Fr is used in the rating life equation for P (P = Fr).
P is a substitute force for combined load and various load cases
If this condition is not met, a constant radial force must first be determined for the rating life calculation that (in relation to the rating life) represents an equivalent load. This force is known as the equivalent dynamic bearing load P.
Fa/Fr ≦ e or Fa/Fr > e
The calculation of P is dependent on the load ratio Fa/Fr and the calculation factor e ➤ Equation and ➤ Equation.
Equivalent dynamic load
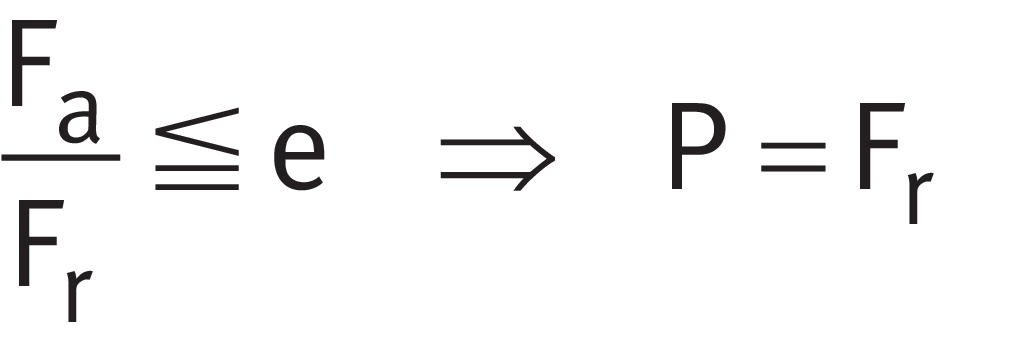
Equivalent dynamic load

Legend
P | N |
Equivalent dynamic bearing load |
Fr | N |
Radial load |
Fa | N |
Axial load |
e, X, Y | - |
Factors ➤ Table |
Factors e, X, Y and f0
The values for the factors e, X and Y are valid for normal fits (shaft produced to j5 Ⓔ or k5 Ⓔ, housing bore produced to J6 Ⓔ). If the calculation values lie between the stated values (for example 0,4), read off the table values for 0,3 and 0,5 and determine the intermediate values using linear interpolation.
Factors e, X and Y
|
Factor for radial internal clearance |
||||||||
---|---|---|---|---|---|---|---|---|---|
Group N |
Group 3 |
Group 4 |
|||||||
e |
X |
Y |
e |
X |
Y |
e |
X |
Y |
|
0,3 |
0,22 |
0,56 |
2 |
0,32 |
0,46 |
1,7 |
0,4 |
0,44 |
1,4 |
0,5 |
0,24 |
0,56 |
1,8 |
0,35 |
0,46 |
1,56 |
0,43 |
0,44 |
1,31 |
0,9 |
0,28 |
0,56 |
1,58 |
0,39 |
0,46 |
1,41 |
0,45 |
0,44 |
1,23 |
1,6 |
0,32 |
0,56 |
1,4 |
0,43 |
0,46 |
1,27 |
0,48 |
0,44 |
1,16 |
3 |
0,36 |
0,56 |
1,2 |
0,48 |
0,46 |
1,14 |
0,52 |
0,44 |
1,08 |
6 |
0,43 |
0,56 |
1 |
0,54 |
0,46 |
1 |
0,56 |
0,44 |
1 |
Legend
f0 | - |
Factor ➤ Table |
Fa | N |
Axial dynamic bearing load |
C0r | N |
Basic static load rating ➤ link |
Factor f0
Bore code |
Factor f0 |
||
---|---|---|---|
60 |
62 |
63 |
|
3 |
‒ |
12,9 |
‒ |
4 |
‒ |
12,2 |
12,4 |
5 |
‒ |
13,2 |
12,2 |
6 |
‒ |
13 |
‒ |
7 |
13 |
12,4 |
‒ |
8 |
12,4 |
13 |
‒ |
9 |
13 |
12,4 |
‒ |
00 |
12,4 |
12,1 |
11,3 |
01 |
13 |
12,3 |
11,1 |
02 |
13,9 |
13,1 |
12,1 |
03 |
14,3 |
13,1 |
12,3 |
04 |
13,9 |
13,1 |
12,4 |
05 |
14,5 |
13,8 |
12,4 |
06 |
14,8 |
13,8 |
13 |
07 |
14,8 |
13,8 |
13,1 |
continued ▼ |
Factor f0
Bore code |
Factor f0 |
||
---|---|---|---|
60 |
62 |
63 |
|
08 |
15,3 |
14 |
13 |
09 |
15,4 |
14,3 |
13 |
10 |
15,6 |
14,3 |
13 |
11 |
15,4 |
14,3 |
12,9 |
12 |
15,5 |
14,3 |
13,1 |
13 |
15,7 |
14,3 |
13,2 |
14 |
15,5 |
14,4 |
13,2 |
15 |
15,7 |
14,7 |
13,2 |
16 |
15,6 |
14,6 |
13,2 |
17 |
15,7 |
14,7 |
13,1 |
18 |
15,6 |
14,5 |
13,9 |
19 |
15,7 |
14,4 |
13,9 |
20 |
15,9 |
14,4 |
13,8 |
21 |
15,8 |
14,3 |
13,8 |
22 |
15,6 |
14,3 |
13,8 |
24 |
15,9 |
14,8 |
13,5 |
26 |
15,8 |
14,5 |
13,6 |
28 |
16 |
14,8 |
13,6 |
30 |
16 |
15,2 |
13,7 |
continued ◆ |
Factor f0
Bore code |
Factor f0 |
||
---|---|---|---|
60 |
62 |
63 |
|
32 |
16 |
15,2 |
13,9 |
34 |
15,7 |
15,3 |
13,9 |
36 |
15,6 |
15,3 |
13,9 |
38 |
15,8 |
15 |
14 |
40 |
15,6 |
15,3 |
14,1 |
44 |
15,6 |
15,2 |
14,1 |
48 |
15,8 |
15,2 |
14,2 |
52 |
15,7 |
15,2 |
‒ |
56 |
15,9 |
15,3 |
‒ |
60 |
15,7 |
‒ |
‒ |
64 |
15,9 |
‒ |
‒ |
68 |
15,8 |
‒ |
‒ |
72 |
15,9 |
‒ |
‒ |
76 |
‒ |
‒ |
‒ |
80 |
‒ |
‒ |
‒ |
84 |
‒ |
‒ |
‒ |
88 |
‒ |
‒ |
‒ |
92 |
‒ |
‒ |
‒ |
96 |
‒ |
‒ |
‒ |
continued ▲ |
Equivalent static bearing load
Radial insert ball bearings are based on single row deep groove ball bearings 60, 62 or 63.
F0a/F0r ≦ 0,8 or F0a/F0r > 0,8
For deep groove ball bearings under static loading ➤ Equation and ➤ Equation. The calculation of P0 is dependent on the load ratio F0a/F0r and the factor 0,8.
Equivalent static load
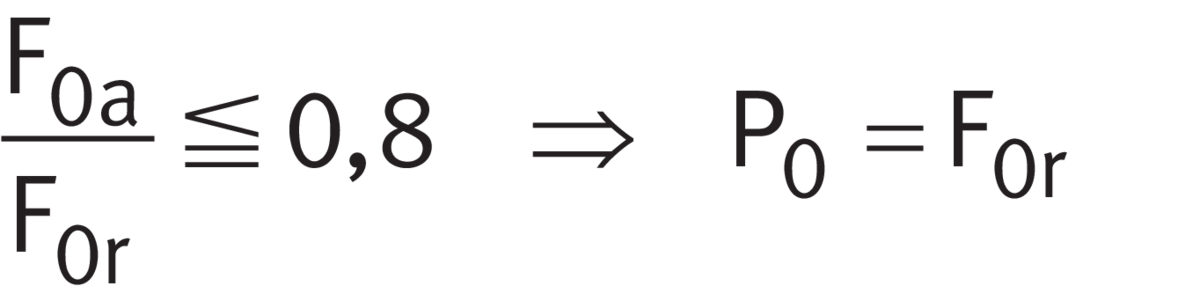
Equivalent static load

Legend
P0 | N |
Equivalent static bearing load |
F0r, F0a | N |
Largest radial or axial load present (maximum load) |
Static load safety factor
S0 = C0/P0
In addition to the basic rating life L (L10h), it is also always necessary to check the static load safety factor S0 ➤ Equation.
Static load safety factor
Legend
S0 | - |
Static load safety factor |
C0 | N |
Basic static load rating |
P0 | N |
Equivalent static bearing load |
Minimum load
Rolling bearings under low loads are particularly prone to slippage
If the lubricant film between the rolling elements and raceways is broken as a result of slippage, the contact partners will be in contact at a very high relative velocity and there will be an erratic increase in wear in the bearing. The risk of slippage is particularly high in the case of bearings under low loads.
Minimum radial load
In order to ensure slippage-free operation, the bearings must be subjected to a minimum radial load. This applies particularly in the case of high speeds and high accelerations. In continuous operation, ball bearings with cage must therefore be subjected to a minimum radial load of the order of P ≧ 0,01 · Cr.
Design of bearing arrangements
Shaft tolerances for radial insert ball bearings
The permissible shaft tolerance is dependent on the speed and load. Shafts up to tolerance class h9 Ⓔ can be used.
Drawn shafts will suffice for most applications.
Roughness of cylindrical bearing seating surfaces
Ra must not be too high
The roughness of the bearing seats must be matched to the tolerance class of the bearings. The mean roughness value Ra must not be too high, in order to maintain the interference loss within limits. The shafts must be ground, while the bores must be precision turned. The roughness values stated as a function of the IT grade of the bearing seating surfaces are guide values ➤ Table.
Roughness values for cylindrical bearing seating surfaces – guide values
Nominal diameter d (D) |
Recommended mean roughness value Ramax |
||||
---|---|---|---|---|---|
mm |
μm |
||||
Diameter tolerance (IT grade) |
|||||
over |
incl. |
IT7 |
IT6 |
IT5 |
IT4 |
‒ |
80 |
1,6 |
0,8 |
0,4 |
0,2 |
80 |
500 |
1,6 |
1,6 |
0,8 |
0,4 |
Suitable housing units for radial insert ball bearings
For radial insert ball bearings, Schaeffler offers the appropriate plummer block, flanged and take-up housings made from cast iron, sheet steel and plastic. The housings can, like the radial insert ball bearings themselves, also be provided in a corrosion-resistant design ➤ Table. Cast iron housings are always one-piece units and can support high loads. Sheet steel housings are two-piece units and are used where the priority is not the load carrying capacity of the housing but the low mass of the unit.
Plummer block housing unit Cast iron housing with integrated radial insert ball bearing |
![]() |
Flanged housing unit Sheet steel housing with integrated radial insert ball bearing |
![]() |
Ready-to-fit units eliminate the need for in-house production of the mounting environment for the bearings
The housing units comprise radial insert ball bearings with a spherical outer ring and a housing with a spherical bore to form ready-to-fit units. The user is thus spared the need for costly production of the mounting environment required for these bearings. The areas of application correspond to those of the radial insert ball bearings.
Example of the location of radial insert ball bearings with four-bolt flanged housing units PCJ in a pallet transport system Design of shaft to tolerance class h9 Ⓔ |
![]() |
Roller chain idler sprocket units and idler pulley units
Roller chain idler sprocket units and idler pulley units are tensioning elements for return units or belt drives ➤ Figure. Roller chain idler sprocket units can compensate for chain stretch resulting from operation and give smoother system running under high loads and velocities. Idler pulley units increase the wrap angle in belt drives and can therefore transmit higher power levels.
Roller chain idler sprocket units and idler pulley units from Schaeffler
|
![]() |
Overview of possible combinations
The following overviews represent the possible combinations of radial insert ball bearings with housings from Schaeffler:
- standard cast iron housings, ISO range ➤ Table
- standard sheet steel housings, ISO range ➤ Table
- corrosion-resistant cast iron and sheet steel housings ➤ Table
- corrosion-resistant plastic housings ➤ Table
- Black Series, cast iron housings, JIS range ➤ Table
Product tables and descriptions of the catalogue range of housing units as well as roller chain idler sprocket units and idler pulley units:
- Catalogue Radial Insert Ball Bearings and Housing Units SG 1
- Download and ordering http://www.schaeffler.de/std/1B64
Possible combinations of radial insert ball bearings with cast iron housings
Radial insert ball bearing |
Standard cast iron housing |
Radial insert ball bearing |
Standard cast iron housing |
Radial insert ball bearing |
Standard cast iron housing |
|||||||||
---|---|---|---|---|---|---|---|---|---|---|---|---|---|---|
Plummer block housing |
Two-bolt flanged housing |
Three-bolt flanged housing |
Four-bolt flanged housing |
Take-up housing |
||||||||||
![]() |
![]() |
![]() |
![]() |
![]() |
![]() |
![]() |
![]() |
![]() |
![]() |
![]() |
||||
Designation |
ASE | SHE | LCTE | CJT |
Designation |
CFTR | ME | CJ |
Designation |
TUE |
HUE GEH..-HUSE |
HE | SFT | |
Shaft diameter d |
SAO | GLCTE | CFT |
Shaft diameter d |
MEO2) | CJO2) |
Shaft diameter d |
TUEO2) | ||||||
CJTZ | FE | CF | ||||||||||||
RAE..-XL-NPP-B 12 mm –50 mm |
![]() |
![]() |
![]() |
FLCTE..-XL1) |
![]() |
RAE..-XL-NPP-B 12 mm –50 mm |
![]() |
|
|
RAE..-XL-NPP-B 12 mm –50 mm |
|
|
|
|
GRAE..-XL-NPP-B 12 mm – 60 mm |
![]() |
PASE..-XL |
PSHE..-XL |
GLCTE..-XL |
PC(J, F)T..-XL |
GRAE..-XL-NPP-B 12 mm – 60 mm |
PCFTR..-XL |
PME..-XL |
PCJ..-XL, PCF..-XL |
GRAE..-XL-NPP-B 12 mm – 60 mm |
PTUE..-XL |
PHUSE..-XL |
PHE..-XL |
PSFT..-XL |
GRA..-NPP-B-AS2/V 5/8″ – 1 15/16″ |
![]() |
Available by agreement |
Available by agreement |
Available by agreement |
Available by agreement |
GRA..-NPP-B-AS2/V 5/8″ – 1 15/16″ |
Available by agreement |
Available by agreement |
Available by agreement |
GRA..-NPP-B-AS2/V 5/8″ – 1 15/16″ |
Available by agreement |
Available by agreement |
Available by agreement |
Available by agreement |
GE..-XL-KRR-B 17 mm – 120 mm |
![]() |
RASE..-XL |
RSHE..-XL |
![]() |
RCJT(Z)..-XL |
GE..-XL-KRR-B 17 mm – 120 mm |
Available by agreement |
RME..-XL, RFE..-XL |
RCJ..-XL |
GE..-XL-KRR-B 17 mm – 120 mm |
RTUE..-XL |
Available by agreement |
RHE..-XL |
Available by agreement |
G..-KRR-B-AS2/V 5/8″ – 2 15/16″ |
![]() |
Available by agreement |
Available by agreement |
![]() |
Available by agreement |
G..-KRR-B-AS2/V 5/8″ – 2 15/16″ |
Available by agreement |
Available by agreement |
Available by agreement |
G..-KRR-B-AS2/V 5/8″ – 2 15/16″ |
Available by agreement |
Available by agreement |
Available by agreement |
Available by agreement |
GE..-XL-KTT-B 20 mm – 80 mm |
|
TASE..-XL |
TSHE..-XL |
|
TCJT..-XL |
GE..-XL-KTT-B 20 mm – 80 mm |
Available by agreement |
TME..-XL |
TCJ..-XL |
GE..-XL-KTT-B 20 mm – 80 mm |
TTUE..-XL |
Available by agreement |
THE..-XL |
Available by agreement |
TFE..-XL |
||||||||||||||
GE..-XL-KLL-B 20 mm – 50 mm |
|
LASE..-XL |
Available by agreement |
![]() |
LCJT..-XL |
GE..-XL-KLL-B 20 mm – 50 mm |
Available by agreement |
Available by agreement |
Available by agreement |
GE..-XL-KLL-B 20 mm – 50 mm |
Available by agreement |
Available by agreement |
Available by agreement |
Available by agreement |
Designation |
ASE | SHE | LCTE | CJT |
Designation |
CFTR | ME | CJ |
Designation |
TUE |
HUE GEH..-HUSE |
HE | SFT | |
Shaft diameter d |
SAO | GLCTE | CFT |
Shaft diameter d |
MEO | CJO |
Shaft diameter d |
TUEO | ||||||
CJTZ | FE | CF | ||||||||||||
GNE..-XL-KRR-B 30 mm – 100 mm |
|
RSAO..-XL |
![]() |
![]() |
![]() |
GNE..-XL-KRR-B 30 mm – 100 mm |
![]() |
RMEO..-XL |
RCJO..-XL |
GNE..-XL-KRR-B 30 mm – 100 mm |
RTUEO..-XL |
|
|
|
GLE..-XL-KRR-B 20 mm – 70 mm |
|
RASEL..-XL |
Available by agreement |
![]() |
Available by agreement |
GLE..-XL-KRR-B 20 mm – 70 mm |
Available by agreement |
Available by agreement |
RCJL..-XL |
GLE..-XL-KRR-B 20 mm – 70 mm |
Available by agreement |
Available by agreement |
Available by agreement |
Available by agreement |
GSH..-XL-2RSR-B 20 mm – 50 mm |
|
RASEA..-XL |
Available by agreement |
![]() |
RCJTA..-XL |
GSH..-XL-2RSR-B 20 mm – 50 mm |
Available by agreement |
Available by agreement |
Available by agreement |
GSH..-XL-2RSR-B 20 mm – 50 mm |
Available by agreement |
Available by agreement |
Available by agreement |
Available by agreement |
AY..-XL-NPP-B 12 mm – 30 mm |
|
![]() |
![]() |
FLCTEY..-XL1) |
![]() |
AY..-XL-NPP-B 12 mm – 30 mm |
![]() |
|
|
AY..-XL-NPP-B 12 mm – 30 mm |
|
|
|
|
GAY..-XL-NPP-B 12 mm – 60 mm |
|
PASEY..-XL |
PSHEY..-XL |
FLCTEY..-XL1) |
PCJTY..-XL |
GAY..-XL-NPP-B 12 mm – 60 mm |
Available by agreement |
PMEY..-XL |
PCJY..-XL |
GAY..-XL-NPP-B 12 mm – 60 mm |
PTUEY..-XL |
Available by agreement |
PHEY..-XL |
Available by agreement |
GAY..-NPP-B(-AS2/V) 1/2″ – 1 7/16″ |
![]() |
Available by agreement |
Available by agreement |
Available by agreement |
Available by agreement |
GAY..-NPP-B(-AS2/V) 1/2″ – 1 7/16″ |
Available by agreement |
Available by agreement |
Available by agreement |
GAY..-NPP-B(-AS2/V) 1/2″ – 1 7/16″ |
Available by agreement |
Available by agreement |
Available by agreement |
Available by agreement |
GYE..-XL-KRR-B 12 mm – 90 mm |
|
RASEY..-XL |
RSHEY..-XL |
|
RCJTY..-XL |
GYE..-XL-KRR-B 12 mm – 90 mm |
Available by agreement |
RMEY..-XL |
RCJY..-XL |
GYE..-XL-KRR-B 12 mm – 90 mm |
RTUEY..-XL |
Available by agreement |
Available by agreement |
Available by agreement |
GY..-KRR-B-AS2/V 1/2″ – 2 15/16″ |
![]() |
Available by agreement |
Available by agreement |
![]() |
Available by agreement |
GY..-KRR-B-AS2/V 1/2″ – 2 15/16″ |
Available by agreement |
Available by agreement |
Available by agreement |
GY..-KRR-B-AS2/V 1/2″ – 2 15/16″ |
Available by agreement |
Available by agreement | Available by agreement | Available by agreement |
- Without lubrication hole.
- Heavy series.
![]() |
Combinations not possible or not advisable. |
Further information: SG 1 http://www.schaeffler.de/std/1B64
Housing selection wizard: http://www.schaeffler.de/std/1B6A
Possible combinations of radial insert ball bearings with sheet steel housings
Radial insert ball bearing |
Standard sheet steel housing1) |
Radial insert ball bearing |
Standard sheet steel housing |
Radial insert ball bearing |
Standard sheet steel housing |
Radial insert ball bearing |
Standard sheet steel housing |
|||||||||
---|---|---|---|---|---|---|---|---|---|---|---|---|---|---|---|---|
Plummer block housing |
Two-bolt flanged housing |
Three-bolt flanged housing |
Take-up housing |
|||||||||||||
![]() |
![]() |
![]() |
![]() |
![]() |
![]() |
![]() |
![]() |
![]() |
![]() |
![]() |
![]() |
|||||
Designation Shaft diameter d |
GEH..-PBS | GEH..-BT |
GEH..-BT GRG..-RABR |
Designation Shaft diameter d |
FLAN..-LST (2 piece) |
FLAN..-MST (2 piece) |
FLAN..-CSLT FLAN..-CST |
FLAN..-RCSMF GRG..-RCSM |
Designation Shaft diameter d |
FLAN..-MSB (2 piece) |
FLAN..-MSA FLAN..-MSB |
FLAN..-LSTR (2 piece) |
FLAN..-MSTR (2 piece) |
Designation Shaft diameter d |
GEH..-MSTU |
|
RALE..-XL-NPP(-B) 20 mm – 30 mm |
![]() |
|
|
RPB..-XL d = 30 mm |
RALE..-XL-NPP(-B) 20 mm – 30 mm |
RALT..-XL |
|
PCSLT..-XL |
RCSMF..-XL d = 30 mm |
RALE..-XL-NPP(-B) 20 mm – 30 mm |
|
|
RALTR..-XL |
|
RALE..-XL-NPP(-B) 20 mm – 30 mm |
|
RAE..-XL-NPP(-B) 12 mm – 40 mm |
![]() |
PBS..-XL |
PB..-XL |
RPB..-XL |
RAE..-XL-NPP(-B) 12 mm – 40 mm |
|
RAT..-XL |
|
RCSMF..-XL |
RAE..-XL-NPP(-B) 12 mm – 40 mm |
RA..-XL |
|
|
RATR..-XL |
RAE..-XL-NPP(-B) 12 mm – 40 mm |
MSTU..-XL |
GRAE..-XL-NPP-B 20 mm – 60 mm |
![]() |
|
|
|
GRAE..-XL-NPP-B 20 mm – 60 mm |
|
|
|
|
GRAE..-XL-NPP-B 20 mm – 60 mm |
RA..-XL |
GRA..-XL |
|
|
GRAE..-XL-NPP-B 20 mm – 60 mm |
|
(G)E..-XL-KRR-B 17 mm – 60 mm |
![]() |
To be ordered separately |
To be ordered separately |
To be ordered separately |
(G)E..-XL-KRR-B 17 mm – 60 mm |
|
To be ordered separately |
|
|
(G)E..-XL-KRR-B 17 mm – 60 mm |
To be ordered separately |
To be ordered separately |
|
RRTR..-XL |
(G)E..-XL-KRR-B 17 mm – 60 mm |
To be ordered separately |
GE..-XL-KTT-B 20 mm – 60 mm |
|
To be ordered separately |
To be ordered separately |
|
GE..-XL-KTT-B 20 mm – 60 mm |
|
To be ordered separately |
|
|
GE..-XL-KTT-B 20 mm – 60 mm |
To be ordered separately |
To be ordered separately |
|
To be ordered separately |
GE..-XL-KTT-B 20 mm – 60 mm |
To be ordered separately |
Radial insert ball bearing |
Plummer block housing |
Radial insert ball bearing |
Two-bolt flanged housing |
Radial insert ball bearing |
Three-bolt flanged housing |
Radial insert ball bearing |
Take-up housing |
|||||||||
Designation Shaft diameter d |
GEH..-PBS | GEH..-BT |
GEH..-BT GRG..-RABR |
Designation Shaft diameter d |
FLAN..-LST (2 piece) |
FLAN..-MST (2 piece) |
FLAN..-CSLT FLAN..-CST |
FLAN..-RCSMF GRG..-RCSM |
Designation Shaft diameter d |
FLAN..-MSB (2 piece) |
FLAN..-MSA FLAN..-MSB |
FLAN..-LSTR (2 piece) |
FLAN..-MSTR (2 piece) |
Designation Shaft diameter d |
GEH..-MSTU |
|
GE..-XL-KLL-B 20 mm – 50 mm |
![]() |
To be ordered separately |
To be ordered separately |
|
GE..-XL-KLL-B 20 mm – 50 mm |
|
To be ordered separately |
|
|
GE..-XL-KLL-B 20 mm – 50 mm |
To be ordered separately |
To be ordered separately |
|
To be ordered separately |
GE..-XL-KLL-B 20 mm – 50 mm |
To be ordered separately |
GLE..-XL-KRR-B 20 mm – 60 mm |
![]() |
To be ordered separately |
To be ordered separately |
|
GLE..-XL-KRR-B 20 mm – 60 mm |
|
To be ordered separately |
|
|
GLE..-XL-KRR-B 20 mm – 60 mm |
To be ordered separately |
To be ordered separately |
|
To be ordered separately |
GLE..-XL-KRR-B 20 mm – 60 mm |
To be ordered separately |
GSH..-XL-2RSR-B 20 mm – 50 mm |
![]() |
To be ordered separately |
To be ordered separately |
|
GSH..-XL-2RSR-B 20 mm – 50 mm |
|
To be ordered separately |
|
|
GSH..-XL-2RSR-B 20 mm – 50 mm |
To be ordered separately |
To be ordered separately |
|
To be ordered separately |
GSH..-XL-2RSR-B 20 mm – 50 mm |
To be ordered separately |
(G)AY..-XL-NPP-B 12 mm – 60 mm |
|
To be ordered separately |
PBY..-XL |
|
(G)AY..-XL-NPP-B 12 mm – 60 mm |
|
RATY..-XL |
|
|
(G)AY..-XL-NPP-B 12 mm – 60 mm |
RAY..-XL |
|
|
RATRY..-XL |
(G)AY..-XL-NPP-B 12 mm – 60 mm |
To be ordered separately |
GYE..-XL-KRR-B 12 mm – 60 mm |
![]() |
To be ordered separately |
To be ordered separately |
|
GYE..-XL-KRR-B 12 mm – 60 mm |
|
To be ordered separately |
|
|
GYE..-XL-KRR-B 12 mm – 60 mm |
|
|
|
To be ordered separately |
GYE..-XL-KRR-B 12 mm – 60 mm |
To be ordered separately |
- Housings have a Corrotect coating, suffix FA125.
![]() |
Combinations not possible or not advisable. |
Further information: SG 1 http://www.schaeffler.de/std/1B64
Housing selection wizard: http://www.schaeffler.de/std/1B6A
Possible combinations of radial insert ball bearings with cast iron or sheet steel housings, corrosion-resistant
Radial insert ball bearing1) |
Cast iron housing1) |
Radial insert ball bearing |
Sheet steel housing1) |
||||
---|---|---|---|---|---|---|---|
Plummer block housing |
Two-bolt flanged housing |
Four-bolt flanged housing |
Three-bolt flanged housing |
||||
![]() |
![]() |
![]() |
![]() |
![]() |
|||
Designation |
ASE |
CJT |
CJ |
Designation |
FLAN..-MSB-VA (2 piece) |
FLAN..-MSA-VA FLAN..-MSB-VA |
|
Shaft diameter d |
Shaft diameter d |
||||||
GRAE..-XL-NPP-B-FA125 20 mm – 60 mm |
![]() |
PASE..-XL-N-FA125 |
PCJT..-XL-N-FA125 |
PCJ..-XL-N-FA125 |
GRAE..-XL-NPP-B-FA125 20 mm – 60 mm |
Available by agreement |
Available by agreement |
GE..-XL-KRR-B-FA125 20 mm – 50 mm |
![]() |
RASE..-XL-N-FA125 |
RCJT..-XL-N-FA125 |
RCJ..-XL-N-FA125 |
GE..-XL-KRR-B-FA125 20 mm – 50 mm |
Available by agreement |
Available by agreement |
SUC 12 mm – 30 mm |
![]() |
Available by agreement |
Available by agreement |
Available by agreement |
SUC 12 mm – 30 mm |
RRY..-VA |
GRRY..-VA |
- With Corrotect coating.
Catalogue range; other dimensions and combinations available by agreement.
Further information: SG 1 http://www.schaeffler.de/std/1B64
Housing selection wizard: http://www.schaeffler.de/std/1B6A
Possible combinations of radial insert ball bearings with plastic housings
Radial insert ball bearing |
Plastic housing |
Radial insert ball bearing |
Plastic housing |
||||||
---|---|---|---|---|---|---|---|---|---|
Plummer block housing |
Two-bolt flanged housing |
Four-bolt flanged housing |
Take-up housing |
||||||
![]() |
![]() |
![]() |
![]() |
![]() |
![]() |
![]() |
|||
Designation |
GEHPP | GEHPPA |
GEHPFL |
GEHPCTL |
Designation |
GEHPF |
GEHPT |
GEHPHE |
|
Shaft diameter d |
Shaft diameter d |
||||||||
SUB 20 mm – 50 mm |
![]() |
SUBPP |
SUBPPA |
SUBPFL |
SUBPCTL |
SUB 20 mm – 50 mm |
SUBPF |
SUBPT |
SUBPHE |
SUC 20 mm – 50 mm |
![]() |
SUCPP |
SUCPPA |
SUCPFL |
![]() |
SUC 20 mm – 50 mm |
SUCPF |
SUCPT |
SUCPHE |
SUG 20 mm – 50 mm |
![]() |
SUGPP |
SUGPPA |
SUGPFL |
SUGPCTL |
SUG 20 mm – 50 mm |
SUGPF |
SUGPT |
SUGPHE |
GRAE..-XL-NPP-B-FA107/125 20 mm – 50 mm |
![]() |
CUGPP |
CUGPPA |
CUGPFL |
CUGPCTL |
GRAE..-XL-NPP-B-FA107/125 20 mm – 50 mm |
CUGPF |
CUGPT |
CUGPHE |
Catalogue range; other dimensions and combinations available by agreement.
![]() |
Combinations not possible or not advisable. |
Further information: SG 1 http://www.schaeffler.de/std/1B64
Housing selection wizard: http://www.schaeffler.de/std/1B6A
Possible combinations of JIS radial insert ball bearings with JIS housings (Black Series)
Radial insert ball bearing1) |
Cast iron housing1) |
Radial insert ball bearing |
Cast iron housing |
||||||
---|---|---|---|---|---|---|---|---|---|
Plummer block housing |
Two-bolt flanged housing |
Four-bolt flanged housing |
Take-up housing |
||||||
![]() |
![]() |
![]() |
![]() |
![]() |
![]() |
![]() |
|||
Designation |
P | PA | FL |
Designation |
F | FC |
T |
FA | |
Shaft diameter d |
Shaft diameter d |
||||||||
UC 12 mm – 90 mm 1/2″ – 3 1/2″ |
![]() |
UCP |
UCPA |
UCFL |
UC 12 mm – 90 mm 1/2″ – 3 1/2″ |
UCF |
UCFC |
UCT |
UCFA |
UK 20 mm – 80 mm |
![]() |
UKP |
Available by agreement |
UKFL |
UK 20 mm – 80 mm |
UKF |
UKFC |
UKT |
Available by agreement |
- With Durotect BS coating
Catalogue range; other dimensions and combinations available by agreement.
Further information: SG 1 http://www.schaeffler.de/std/1B64
Housing selection wizard: http://www.schaeffler.de/std/1B6A
Mounting and dismounting
The detailed guidelines on the mounting and dismounting of radial insert ball bearings must be observed. These can be found in Catalogue SG 1, Radial Insert Ball Bearings and Housing Units http://www.schaeffler.de/std/1B64.
Tightening torques for grub screws
The tightening torques for metric and inch size grub screws from Schaeffler are dependent on the material of the screws ➤ Table and ➤ Table. The tightening torques are valid only for original grub screws from Schaeffler (INA or FAG brand).
Fully tightening the grub screws or locknut in the inner ring |
![]() |
Tightening torques for standard grub screws
Width across flats W |
Thread |
Tightening torque1) MA |
||
---|---|---|---|---|
mm |
inch |
ISO |
UNF |
Nm |
2,5 |
3/32 |
M5 |
N10-32 |
3,6 |
3 |
1/8 |
M6×0,75 |
1/4″-28 |
6 |
4 |
5/32 |
M8×1 |
5/16″-24 |
14 |
5 |
3/16 |
M10×1,25 |
3/8″-24 |
26 |
6 |
1/4 |
M12×1,5 |
1/2″-20 |
42 |
- Grub screws from Schaeffler.
- GYE90-KRR-B.
Tightening torques for metric grub screws, corrosion‑resistant VA design
Width across flats W |
Thread |
Tightening torque1) MA |
---|---|---|
mm |
Nm |
|
2,5 |
M5 |
2,4 |
3 |
M6×0,75 |
3,9 |
4 |
M8×1 |
8,3 |
5 |
M10×1,25 |
16 |
- High grade steel grub screws from Schaeffler.
Tightening torques for locknuts
The tightening torques for the locknuts differ between the two brands INA and FAG ➤ Table and ➤ Table.
Hook wrenches and tightening torques for radial insert ball bearings of the INA brand
Shaft diameter |
Hook wrench, type A to DIN 1810 |
Tightening torque Locknut |
||
---|---|---|---|---|
d |
for tightening |
for countertensioning of adapter sleeve |
MA |
|
min. |
max. |
|||
mm |
Nm |
Nm |
||
20 |
A 30–32 (HN 4) |
A 25–28 (HN 2) |
13 |
17 |
25 |
A 40–42 (HN 5) |
A 30–32 (HN 3) |
22 |
28 |
30 |
A 45–50 (HN 6) |
A 34–36 (HN 4) |
33 |
40 |
35 |
A 52–55 (HN 7) |
A 40–42 (HN 5) |
47 |
56 |
40 |
A 58–62 (HN 8) |
A 45–50 (HN 6) |
70 |
80 |
50 |
A 68–75 (HN 10) |
A 52–55 (HN 7) |
90 |
105 |
Tightening torques for locknuts, Black Series, FAG brand
Shaft d |
Locknut |
Tightening torque MA |
---|---|---|
±5% |
||
mm |
Nm |
|
20 |
AN05 |
25 |
25 |
AN06 |
30 |
30 |
AN07 |
40 |
35 |
AN08 |
50 |
40 |
AN09 |
60 |
45 |
AN10 |
75 |
50 |
AN11 |
100 |
55 |
AN12 |
130 |
60 |
AN13 |
150 |
65 |
AN15 |
170 |
70 |
AN16 |
200 |
75 |
AN17 |
230 |
80 |
AN18 |
270 |
Legal notice regarding data freshness
The further development of products may also result in technical changes to catalogue products
Of central interest to Schaeffler is the further development and optimisation of its products and the satisfaction of its customers. In order that you, as the customer, can keep yourself optimally informed about the progress that is being made here and with regard to the current technical status of the products, we publish any product changes which differ from the printed version in our electronic product catalogue.
We therefore reserve the right to make changes to the data and illustrations in this catalogue. This catalogue reflects the status at the time of printing. More recent publications released by us (as printed or digital media) will automatically precede this catalogue if they involve the same subject. Therefore, please always use our electronic product catalogue to check whether more up-to-date information or modification notices exist for your desired product.
Further information
In addition to the data in this chapter, the following chapters in Technical principles must also be observed in the design of bearing arrangements:
- Determining the bearing size ➤ link
- Rigidity ➤ link
- Friction and increases in temperature ➤ link
- Speeds ➤ link
- Bearing data ➤ link
- Lubrication ➤ link
- Sealing ➤ link
- Design of bearing arrangements ➤ link
- Mounting and dismounting ➤ link
The complete catalogue range of the available radial insert ball bearings and housing units, together with all the technical principles, descriptions and product tables, is presented in Catalogue SG 1, Radial Insert Ball Bearings and Housing Units.
- Download and ordering http://www.schaeffler.de/std/1B64
- Housing selection wizard http://www.schaeffler.de/std/1B6A